Flow Chemistry — The Right Tool for CDMOs
For CDMOs, the adoption of flow chemistry can provide a competitive advantage by improving efficiency, safety and quality, while reducing costs and development times.
Small and medium-sized enterprises (SMEs) face specific challenges, particularly due to the complex and highly regulated environment in the chemical and pharmaceutical industries. In the pharmaceutical sector, strict regulatory requirements for the approval of new products result in high costs and long development times. In addition, companies must constantly adapt to changing regulations such as REACh in Europe as well as GMP (Good Manufacturing Practice) and GCP (Good Clinical Practice). This inevitably leads to high resource requirements for the company’s own employees.
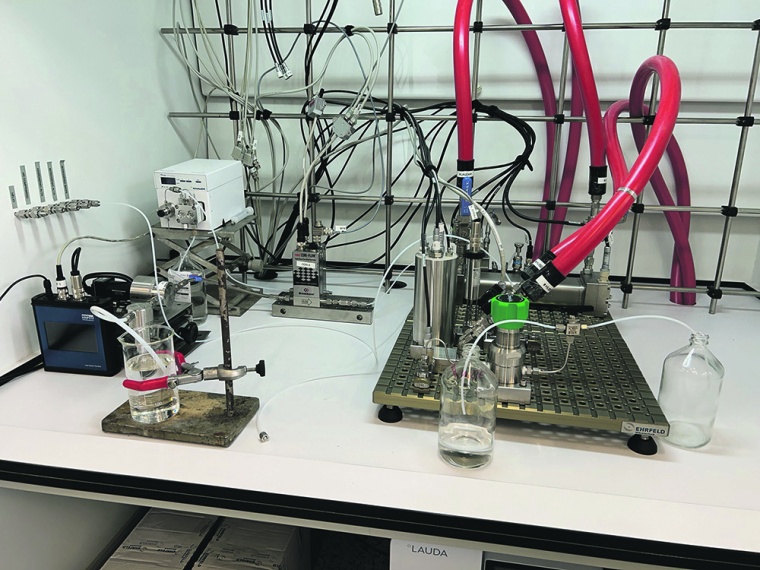
As a result, many manufacturing SMEs are unable to focus on their core competencies such as research and development, marketing and sales of their products. Consequently, these companies are increasingly turning to so-called CDMOs (contract development and manufacturing organizations) for outsourcing their production. These companies are specialized in contract research and manufacturing of chemical and pharmaceutical products in compliance with all regulatory requirements. They also provide access to expert knowledge, state-of-the-art technology, scalability and production flexibility. Through this collaboration, SMEs can reduce their time to market, strengthen their own innovative power and at the same time reduce production costs and risks.
CDMOs Need to Rethink
CDMOs are also facing enormous challenges, especially on the European market, as they have to compete with the often-cheaper competitors from the Indian or Asian market. In order to remain competitive, these companies must invest in future-proof technologies and skilled workers and be able to master the complex global supply chains. These are becoming increasingly disrupted, especially in the current geopolitical uncertainties, making it more difficult for SMEs and CDMOs to obtain the necessary raw materials and intermediate products. This increases costs and delays production. These boundary conditions are now slowly leading to a rethink on the part of companies to produce certain intermediate products on the domestic market. However, the technologies used to date cannot be used to ensure that this is competitive. Historically, almost all chemical syntheses still take place in classic discontinuous vessel operation (batch operation). This method of operating chemical reactions has many advantages but has the major disadvantage that in many cases it is already fully optimized. Any further increase in efficiency requires a high input of resources and investment for a relatively small gain in efficiency. This necessitates a rethink and the use of a different mode of operation and technology.
Flow Chemistry — a “New” Technology?
As a relatively new technology, flow chemistry addresses precisely these disadvantages of the optimized batch process. The chemical syntheses take place in continuous operation, for example in a flow-through pipe. Another feature of this technology is the small reaction volume (factor 1,000 compared to batch) of these reactors with dimensions on a millimeter scale. This combination leads to better control and reproducibility as well as higher reaction rates than in classic batch operation, as the reaction conditions such as temperatures can be increased due to precise control of these parameters. Thus, different process windows than in classical batch can be obtained and chemical reactions which normally need several hours can be processed within minutes at higher yields and selectivity. As an example, a millistructured reactor with a volume of 300 mL can process within an annual operation of 8,000 h already around 50 metric tons. Depending on the reaction time also 100 metric tons are possible to process in such a small reactor. While combining this technology with automation and the usage of real-time online and inline monitoring of the individual reaction parameters the product quality can be always ensured. This approach can already be used in the development of new products in lab scale for optimizing reactions according to their requirements e.g. yield, selectivity, etc. The reactor volumes hereby range between 0.5 mL and 50 mL.
Subsequently, the results obtained can be directly applied to production-scale reactors through a seamless scale-up concept and in addition, this technology can be scaled up e.g. up to 20,000 tons per year easily by parallelizing the reactor channels similar like tube bundle or plate-type heat exchanger. The small volume of the reactors enhances safety, as only a small amount of hazardous material is processed under reaction conditions in the reactors, allowing potentially hazardous reactions to be better controlled. This reduces the risk of accidents and explosions. Particularly in Europe, where chemical companies are struggling to find space for new plants, flow chemistry can play to another strength: the need for a small footprint. A small footprint in a chemical plant is important because it saves space and therefore costs, especially in expensive industrial areas. It also minimizes material and energy consumption, resulting in lower operating costs and increased efficiency. A smaller footprint also reduces the plant’s environmental impact, helps meet environmental regulations and facilitates future expansion or adaptation to new technologies. The above 100 ton plant requires only 4–6 m² of floor space for the dosing, reactor and automation sections.
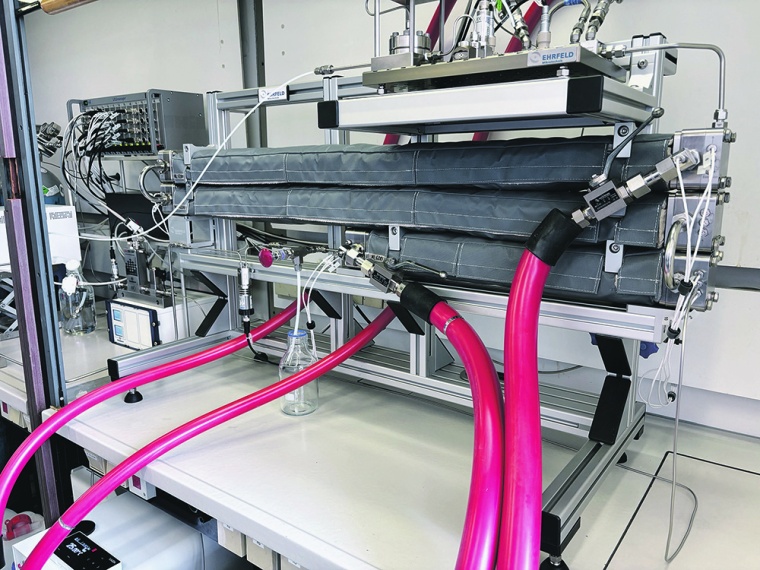
Flowchemistry — Intermediates and Development on Demand
The benefits of this technology are particularly evident in the production of intermediates for CDMOs. Toxic or explosive raw materials are often used for these intermediates and the syntheses present a high safety risk. In many cases, the products themselves do not pose a safety risk, which simplifies storage. The otherwise high regulatory requirements for the manufacture of these products can be significantly reduced through the use of flow chemistry, as the reactive reaction volume is simply small and corresponds to a normal volume in the research department. In addition to the production of intermediates, this technology can also be used in research and development at CDMOs. Due to the small reaction volume and short reaction times (a few minutes), a large number of different process parameters can be tested in a very short time, allowing the reaction to be rapidly screened and quickly optimized in a resource-conserving manner. This enables the use of efficient and scalable reactor technology and minimizes the use of raw materials right from the development stage of new products. Thanks to their versatile reactor design, flow chemistry reactors can be adapted to a wide range of chemical reactions, from simple syntheses to complex multi-step processes. This flexibility allows CDMOs to tailor their processes to the specific needs of each customer.
For CDMOs, the adoption of flow chemistry can provide a competitive advantage by improving efficiency, safety and quality, while reducing costs and development times. As the pharmaceutical industry increasingly demands fast, flexible and sustainable manufacturing solutions, CDMOs that integrate flow chemistry into their offerings will be well positioned to meet these needs and drive innovation in drug development and manufacturing.
Rafael Kuwertz, Managing Director, Ehrfeld Mikrotechnik GmbH,
Wendelsheim, Germany
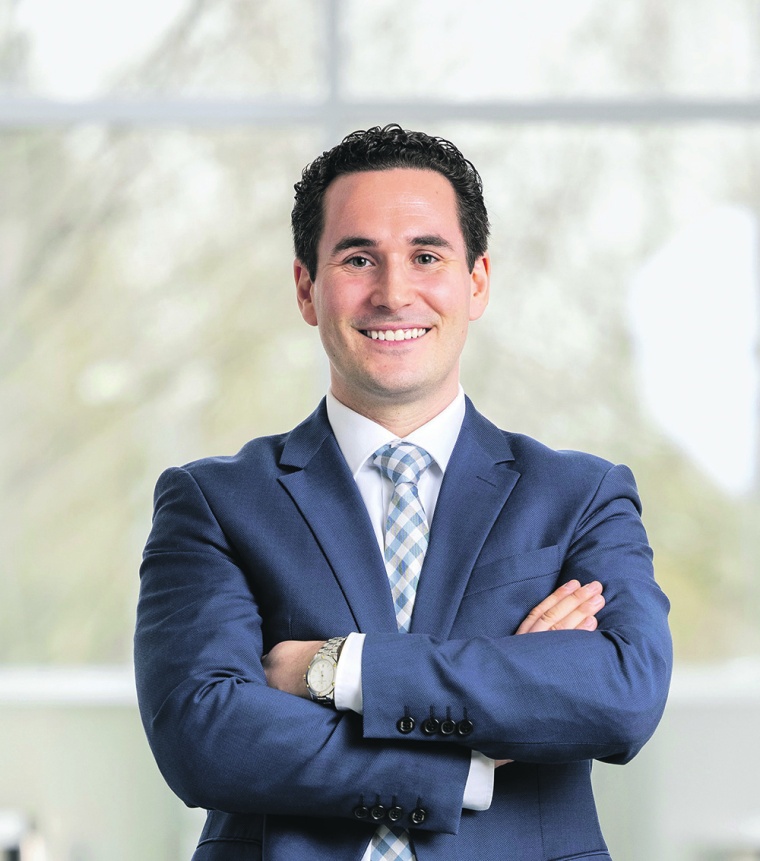