Flow Chemistry
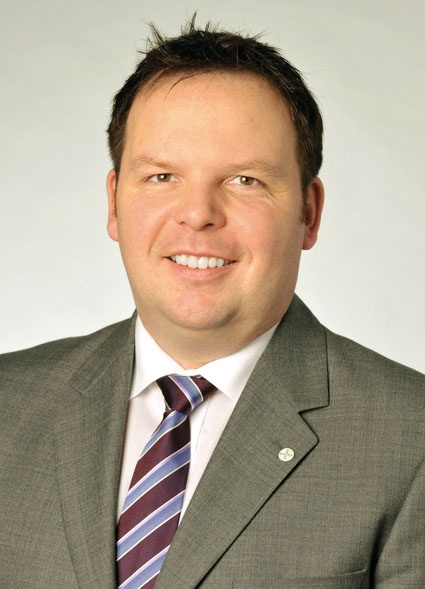
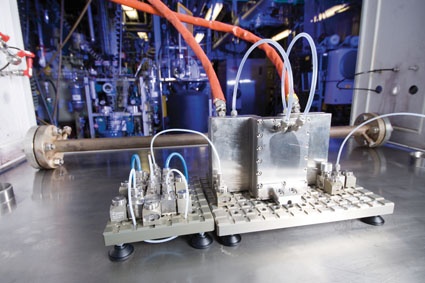
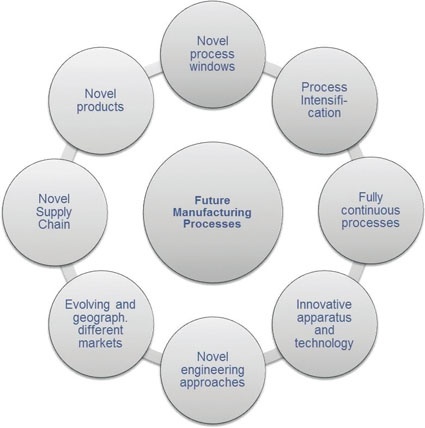
A Comprehensive Approach - The development of future chemical processes requires a truly holistic approach that employs standardized methodologies allowing for fast implementation of both innovative synthesis procedures and innovative process equipment. Figure 1 depicts the necessary broadness of this approach comprising the analysis and optimization of the whole value added chain from novel products over the evaluation and implementation of innovative process equipment to the market developments.
The following common needs can be identified:
- Shorter time to process/market
- Reduction of product and process development costs
- Reduction of both capital and operational expenditures
- Maintain and/or improve robustness and quality simultaneously increasing manufacturing flexibility
Thus tasks for future chemical manufacturing can be derived:
- Introduce efficiency and scalability to multi-purpose, multi-product facilities
- Move risk of process development to early phases
- Engineer modular and standardized processing units
Flow Chemistry and Process Intensification
Flow chemistry approaches integrating process intensification and modular engineering aim to solve these tasks. Flow chemistry is here understood as the systematic combination of chemical characterization, innovative hardware and unit operations, process development, design and reaction engineering employing especially the benefits of continuous flow systems but not restricting to the latter.
Introduction of a batch-to-conti transfer chemical was first successful for critical reaction conditions, sometimes even being the only safe access to the target molecule and for opening up new process windows. A typical production size micro reactor set-up for the synthesis of an intermediate requiring a very high heat transfer capacity and excellent mixing capability is shown in figure 2. Though a number of different reaction classes have been successfully demonstrated and operated up to production scale in the last decade, the continuous instead of batch manufacturing is still not established as a standard in chemical manufacturing. Reasons for this can be development workflows; usage of existing (batch) assets; and high implementation effort for innovative approaches at comparatively low total sales volumes of a single product.
Very often, the selection of synthesis procedures of organic chemists focus on availability of starting material and yield/quality of the product, but the detailed knowledge of the reaction pathway is not considered to be as important as in the development of a heterogeneously catalyzed petrochemical process. In the flow chemistry approach, the time- and space-dependency of the process steps are investigated at an early stage of development, allowing for the design of processes exactly according to the requirements of the chemical transformation and pushing the reaction "to its limits." The overall process design does not restrict to classical equipment but includes also process intensified equipment and technologies for novel reaction pathways employing e.g. innovative solvents. Sustainable processes with superior performance and less consumption of starting materials and auxiliaries can be designed by this approach.
Standardization And Modularization
A systematic process design requires robust and fully scalable equipment and process design; engineering and equipment cost must not exceed the limits of an economic and sustainable process. A truly modular approach employing standardized, robust equipment that is easily fully scalable will significantly decrease the expenditures related to design, engineering and construction. Thus, the implementation effort mentioned above can be decreased, which will enable integration of innovative process technology.
But not only manufacturers of small- to medium-sized projects experience increasing pressure resulting from shorter innovation cycles, markets evolving and decreasing in geographically different locations, global competition and increasing process for resources. This is also valid for large, world-scale plants that are designed for high-process efficiency rather than flexibility. Here, standardized small units can decrease initial investment risks, allow for rapid market entry also in remote locations and enable novel flexible and decentralized production concepts with optimized supply chains.
In order to realize this step change in the chemical and pharmaceutical process industries, a joined and interdisciplinary approach is necessary comprising academia, chemical industry, equipment manufacturers and engineering companies. In order to achieve technical standardization rather than technical differentiation, company borders have to be overcome and joint developments in non-competitive areas are important to develop this approach. Prominent examples for this open innovation approach are current projects of the 7th European Frame Work program such as Copiride and F³ Factory aiming at novel process equipment, a standardized infrastructure and demonstrating a number of example processes. The development of highly integrated and thus flexible catalytic continuous-flow processes is part of the project Synflow.
A modular platform approach will enable the scale up of innovative processes over a broad range of capacities at beneficial manufacturing costs. Standardized processes and their interfaces have to be developed in close exchange by project partners from all stake holders employing and developing methodologies for whole modular process and plant design.
INVITE Joint Research Center
Bayer Technology Services and the TU Dortmund University just recently announced the foundation of a new joint research center - INVITE - for innovative and modular production concepts and their demonstration. INVITE is a nonprofit research organization and a true public-private partnership. It will act as an open innovation platform allowing different partners to work together on this challenging target. The INVITE research center will host lecturer rooms, a chemical laboratory and a technical hall for the development, test and operation of container-based fully modular process units and process management systems. This standardized "backbone" plant located at the Chempark site in Leverkusen will also serve for demonstration purposes of the projects F³ Factory and Synflow. In order to assess the capabilities of the novel modular approach, case studies on products of the key industrial project partners ranging from APIs over intermediates, polymers towards renewable feedstock will be demonstrated here. The research center will have own R&D staff as well as extensive capabilities for development and demonstration of modularized processes and equipment.
Implementation of resource efficient chemical routes and processes will be a joint effort for chemists, engineers, equipment suppliers and supply chain experts. Commercialization will however only be possible if processes are robust and both ecologically and economically superior. In order to achieve this, a flow chemistry approach must integrate process innovation, modularization and equipment standardization in a comprehensive way. Projects such as e.g. F³ Factory will foster and widespread implementation of continuous cost beneficial equipment and manufacturing platforms.