A Circular Economy for Batteries
Interview with Leon Ferrant, Green Li-ion
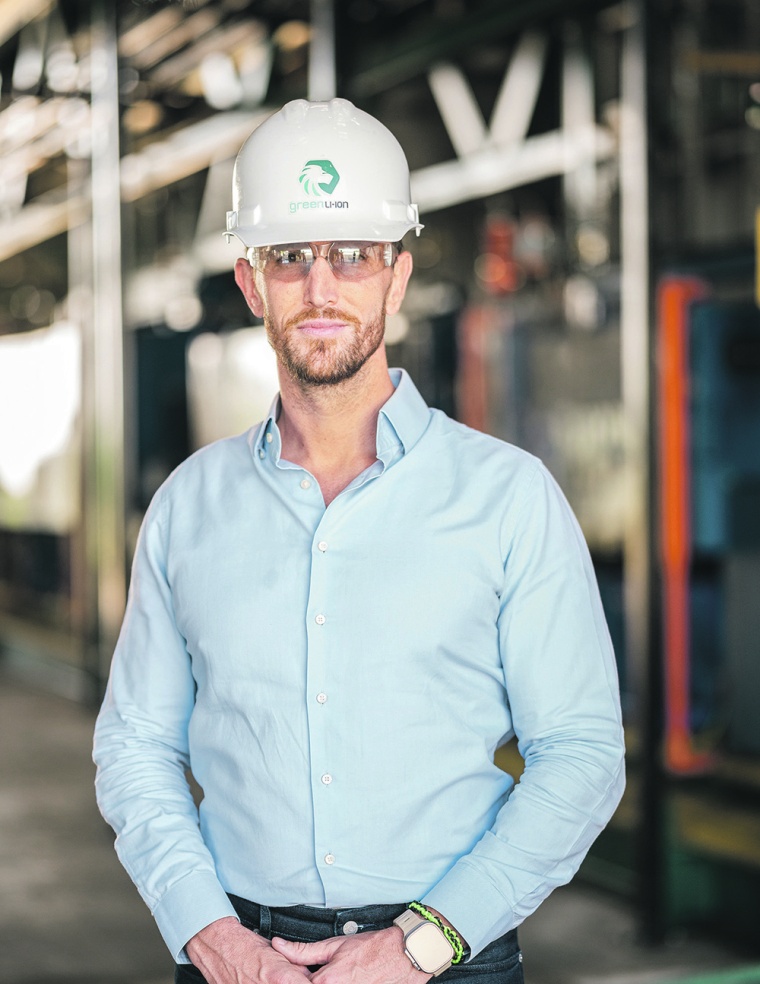
While working in oil and gas, Leon Ferrant identified battery storage as a key challenge in the energy transition, which required upscaling recycling to satisfy demand. Partnering with Reza Katal, a battery recycling technology advancement expert, they recognized the battery recycling supply chain was unsustainable. A key step in the process, pCAM production, was mainly scaled in China. They envisioned a technological revolution that would make domestic pCAM production possible globally and founded Green Li-ion.
CHEManager: Mr. Farrant, what distinguishes your solution from those proposed by other battery recycling companies?
Leon Farrant: Precursor cathode active material (pCAM), a critical stage in battery manufacturing, involves processing black mass — shredded spent batteries comprised of a mix of impurities and critical minerals — from recycled batteries. Traditionally, this black mass must first be sorted into sulfates before being formulated into pCAM. Once produced, pCAM is converted into CAM, which can then be used for new batteries.
Green Li-ion’s Green-hydrorejuvenation technology streamlines this process, creating pCAM directly from black mass feedstock in under 12 hours.
Green Li-ion offers an affordable way for those with black mass to create more value and close the loop for domestic battery production. This gives them an option other than to send black mass to Asia for processing and refinement into battery-grade materials.
Whereas other battery recycling companies plan to build centralized plants where clients can send their black mass for recycling, Green Li-ion’s modular units are customizable to fit any battery cell producer’s needs and deploy quickly into existing facilities. They integrate seamlessly into existing production lines, unlike competitors who require the buildout of entirely new infrastructure.
Why is it important to have domestic battery recycling capabilities?
L. Farrant: Many of the countries where these critical minerals are sourced and mined have unstable governments and unpredictable political systems. Disruption of battery mineral supplies can result in supply problems and price spikes for important consumer goods like computers and cars. Batteries are made with many critical minerals, the most important being cobalt, lithium, and nickel. These three minerals were added to the US government’s critical mineral list in 2022, with all three classified as having ‘high supply risk’ between 2025 and 2035.
Batteries are critical in the energy transition, but the current supply chain has potentially catastrophic pitfalls. A domestic supply chain utilizing battery recycling can boost bottom lines, reduce carbon footprints, and mitigate human rights concerns. Green Li-ion’s recycling units will create a whole new market within the US and open new revenue streams for OEMs, diversified industrials using battery recycling as a business unit like the automotive industry, and pure-play recyclers.
What makes the company’s recent Atoka installation unique?
L. Farrant: The Atoka installation is the first plant producing pCAM from black mass in North America, representing a giant leap forward for the battery recycling industry. Located within an existing recycling facility, the plant produces valuable battery-grade cathode and anode materials from concentrated components of spent batteries using Green Li-ion’s patented multi-cathode-producing Green-hydrorejuvenation technology. The Atoka plant is expected to process two tons of black mass, or the equivalent of 72,000 smartphone batteries per day, with plans to quadruple this capacity within the coming year.
What hurdles must the industry and Green Li-ion overcome?
L. Farrant: Battery recycling is a nascent industry, and our technology’s novelty poses significant challenges. Convincing customers and investors requires proof of concept, which is why we prioritize achieving operational milestones before seeking funding. In the US, for instance, we’re waiting until our plant in Oklahoma produces high-quality pCAM graded by third parties before applying for federal grants. This strategy simplifies grant applications and reassures potential customers seeking grant eligibility.
Another hurdle lies in spent battery collection. Battery manufacturers rely primarily on virgin materials and lack efficient collection processes; OEMs or third parties implementing a robust collection system is crucial for cost reduction and risk mitigation.
Where is Green Li-ion headed next?
L. Farrant: Green Li-ion has already established a solid supply line and off-taker for the Atoka plant and is currently working to sign more deals to get our modular recycling units in more factories across the world. With the proven success of the Atoka installation, we aim to scale and deploy our modular technology worldwide, with a specific focus on North America and Europe for our next partnerships.
“Green Li-ion offers an affordable way for those with black mass to create more value and close the loop for domestic battery production.”
-------------------------------------------------
Personal Profile
Leon Farrant, CEO and co-founder of Green Li-ion, brings two decades of global energy sector expertise. With a history of entrepreneurial spirit and vision, he has led established companies and start-ups across multiple continents to success. Leon excels at consensus-building and fostering diverse, high-performing teams aligned with social and environmentally conscious values.
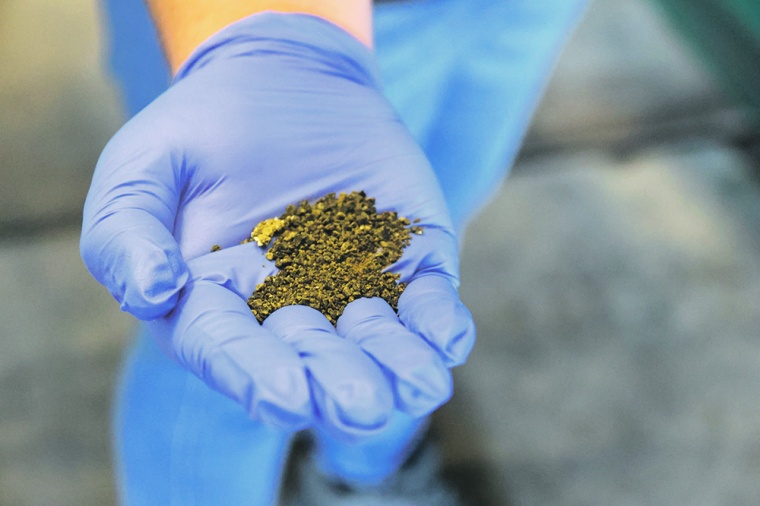
Business Idea
Ready-Made Recycling Units
The clean energy boom has led to a surge in global demand for lithium-ion batteries, creating a serious waste crisis. Despite being 95% recyclable, only 5% of these batteries are currently recycled worldwide, with the vast remainder ending up in landfills, posing environmental risks and leaving profit on the table.
Green Li-ion is working to create a commercially viable closed-loop battery recycling system, reducing reliance on virgin materials and landfill waste. This will not only create a more sustainable battery industry but also enhance the security of the supply chain for critical minerals needed in clean energy technologies.
Their patented Green-hydrorejuventation process, facilitated by their modular recycling units, runs black mass through special solutions to filter out impurities and reformulate the feedstock into pCAM. The process takes less than 12 hours and produces a product with 99% purity levels, ready to be dropped into new batteries.
Green Li-ion offers flexible options for manufacturers and recyclers to utilize its technology either through a licensing agreement that allows the plant to be installed in their own facilities or through a tolling agreement where they can send their black mass to Green Li-ion-owned plants for processing directly into battery materials. The modular nature of Green Li-ion systems allows for rapid deployment and setup that enables operations to begin in a few months instead of building dedicated infrastructure over several years.
Green Li-ion has already established a solid supply line and off-taker for the Atoka plant and is currently working to sign more deals to get their modular recycling units in more factories across the world.
The company is based in Singapore, with supporting teams in the US, South Korea, Germany, and Australia.
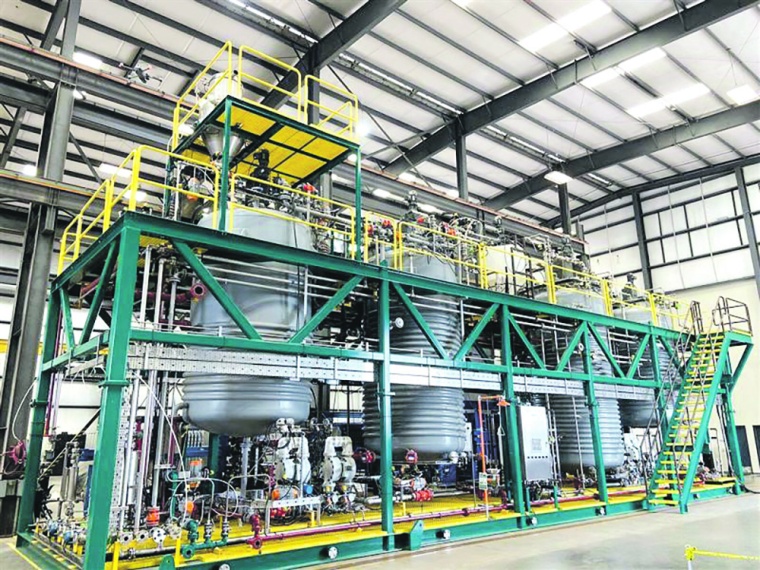
Elevator Pitch
Scaling Across the World
Green Li-ion has raised over 30M USD with partners including HSBC, Equinor Ventures, SOSV, EDP, Banpu NEXT, SK TES, Energy Revolution Ventures, TRIREC, and Petronas.
With the success of the Atoka installation, the first pCAM-producing plant in North America, the next step for the company will be scaling and incentivizing industry buy-in.
Milestones
- 2020
- Green Li-ion was founded
- Filing of the first family of patents
- Finalized R&D optimization on its breakthrough technology, GLMC-1
- 2021
- Continuing progress with its R&D, filing an additional patent family
- Start of work on new technologies GL LFP and GLMC-2
- Raised $3.5 million in seed funding round
- 2022
- Global strategic development team set up in the US, Europe and Asia
- Raised $12 million Series A funding
- 2023
- Filing of patents across eight families
- Construction of six working plants; first plant begins commissioning; remaining five plants ready to be shipped
- Setup of global R&D and engineering team in Australia and Singapore
- Raised $25 million Series pre-B funding
- Series pre-B extension round
- 2024
- Process for removing impurities in Li-ion batteries recycling patented
- LCA confirms that Green Li-ion’s process reduces climate impact of pCAM production by nearly 90% compared to production using virgin materials
- Fully commissioned Atoka plant with the modular recycling unit successfully producing pCAM
Roadmap
- 2024
- Setup of first machines in Europe
- 2025
- Further scaling of technology to deploy GL TRAIN, with approx. 4x the capacity of current GLMC 1 unit
- Further refining GLMC 2 to allow for flexibility in producing either pCAM or metal salts and enable lower operating costs