Rail Cargo: Back to the future
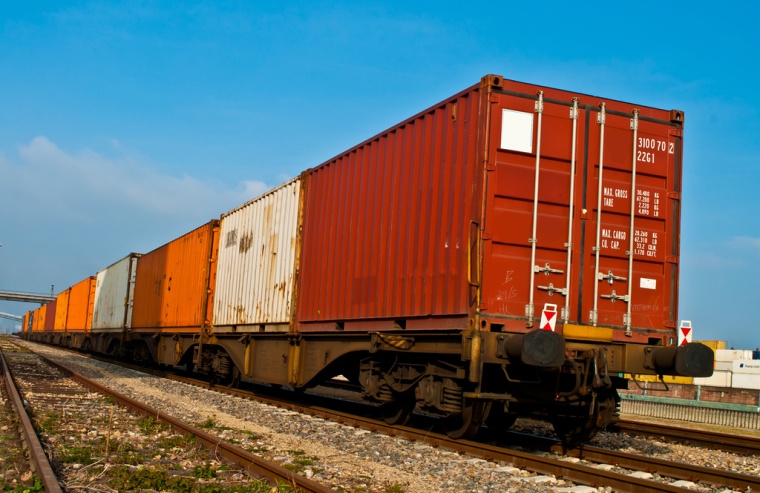
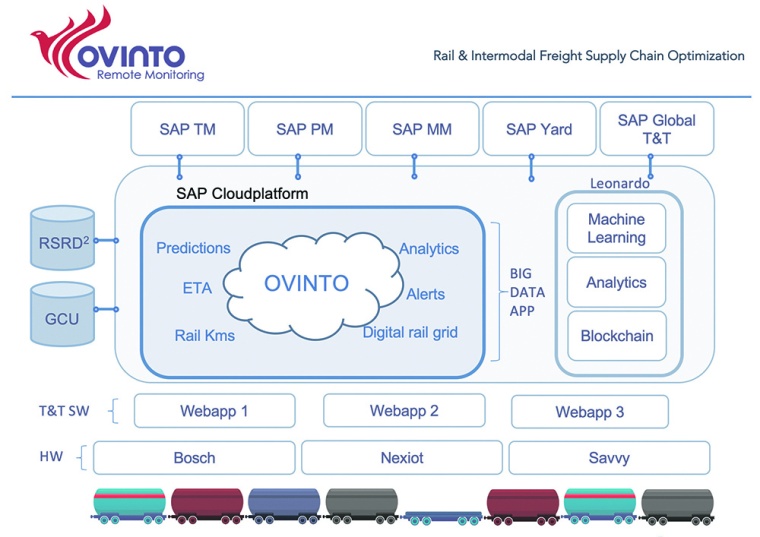
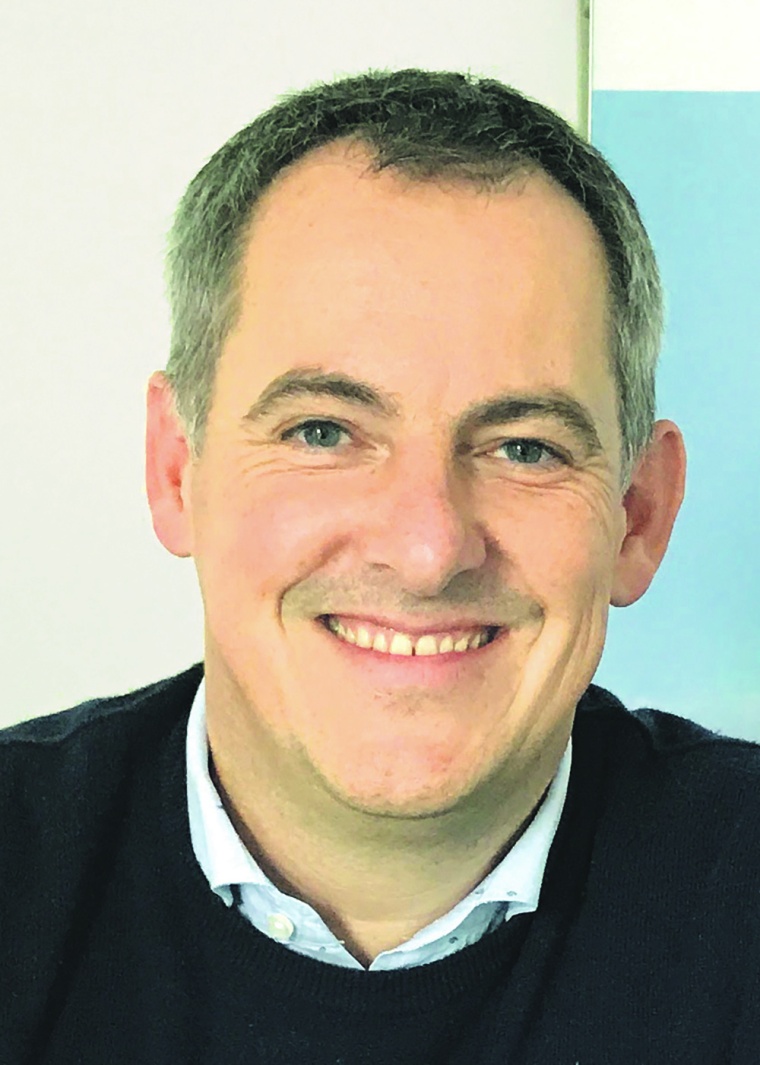
An intelligent enterprise is, as we know, data and process driven. The data feeds intelligence which in turn feeds process automation and innovation. This implies that the available data at least have to be connected — a statement that seems very logical but sadly not always is the case. The chemical industry is known for its professionality and innovation. Chemical industries are used to spend large amounts of money on R&D year by year, but sometimes certain aspects of business doing tend to be forgotten when it comes to innovation.One of those aspects is rail freight transport.
Rail cargo is still being handled and executed like 100 years ago, heavily depending on manual, human interventions. Where all other transport modes are connected and being automated, rail freight mostly is not, often remaining a blind spot to the chemical companies.
In a way this is very strange as rail freight stands for “bulk in & out,” meaning that most of all invoiced goods will travel via rail implying that however efficient the production may become, the real capacity will be dictated by the bottleneck called “rail”. So why hasn’t there been a much stronger focus on the rail transport efficiency until now?
Just imagine that rail freight transport tomorrow would suddenly become 30% easier. The efforts to increase production and sales of more products would be marginal, so that the improvement of the railways, i. e. the innovation in rail transport, could be a real driver for sales and earnings increases.
Reduce Repetitive Manual Labor
At Ovinto we were amazed to see how the industry is putting effort in operational efficiency on the one hand but continues to handle rail cargo in a very archaic way on the other hand. We noticed that large industrial players invest very heavily in back office software platforms, connect trucks, planes and ships but often forget to connect and automate rail freight.
From this came the idea and mission for us to develop a platform, dedicated to help the existing software infrastructure in these industries when it comes to rail freight.
The goal and purpose of this platform is to connect all relevant internal and external data sources, digitize all data, automate repetitive manual actions, enrich and preprocess the gathered data to feed the results into the relevant existing software modules that were before constantly waiting for manual input.
By doing so we drastically reduce repetitive manual labor and we also drastically reduce errors. The existing software infrastructure is able to speed up and become even more efficient as it doesn’t have to wait for input all the time.
Summarized this means that we have developed a platform dedicated to feed and be of service to existing SAP modules to enable them to speed up with less input errors when it comes to rail and intermodal freight of course. Following are some examples and use cases.
Predictive ETA Services
From the moment we start to analyze rail freight trajectories, the generated data can be used to create intelligence that is being fed back to the planning system. By analyzing all historical transports/trajectories of a fleet of rail cars it becomes possible to calculate the exact average speed per specific segment of rail track in the grid. Next to the speed, also the percentage of risk of having a delay can be calculated leading to the possibility of comparing actual data with calculated and analyzed historical data to find out how the current trajectory is related to the planning and the created intelligence out of the history.
By doing this, predictive services can be created to warn shipper, operator but also the customer about possible delays and anomalies during transports. Because of the repetitiveness of the transports, predictions only become better in time offering a better and better accuracy to all stakeholders taking the biggest pain away in the rail freight sector: the blind spot.
Integrating ETA analysis (ETA = estimated times of arrival) back into the planning software module will allow a higher rotation because of a much faster adaptation to new situations as the transport planning module will be informed sooner and better.
Thus, not only the maintenance can be improved but also the transport rotation — a.k.a. real business — can be improved.
Safety Stock and Production Planning
As from the moment anomalies can be predicted and planning is improved this can be connected to the production planning of the company. Until today, industrial production facilities often encounter near shutdowns or even shutdowns because of hitches in the supply of raw materials.
Trains come in late, don’t come in at all or don’t carry all planned rail cars. To cope with these irregularities, companies tend to increase their safety stock but even that is not always sufficient.
Predictive services enable production sites to respond faster and avoid costly downtime. Because of the already mentioned improving character of predictive services, the “peak” anomalies constantly become smaller leading to the situation where companies can start to lower their safety stocks as the irregularities become smaller.
A reduced safety stock will have an immense impact on the business as next to the financial impact there often will be also a “safety related impact” when considering dangerous goods.
In Transition: Machine Learning Services
The famous saying “garbage in, garbage out” is of course also applicable to the rail freight industry. Bill of ladings in planning software will often be based on the manual input regarding which assets are being used.
Many times the trains are assembled in the yard of industrial companies, where pen and paper are still used, and these documents are then manually translated by another colleague into a software program. These procedures leave a lot of room for errors that cannot easily be traced or filtered by the software afterwards.
Countering this problem can be done by implementing machine learning services such as optical recognition services by using a camera or smart device. By scanning the rail cars, exact ID recognition can allow for an automatic train composition and leading to an automatic creation of the bill of lading avoiding costly, repetitive, manual actions and more important also avoiding a lot of errors which will, again, have a direct impact on the business and efficiency.
We could continue to list use cases, but the above-mentioned examples should already give an impression of the phenomenal impact on business we can generate when making rail cargo much more efficient.
Summary
As we want to connect as much data sources and feed existing software modules, we deliberately chose to build our platform in the SAP Cloud Platform using the power of the in-memory database HANA. The cloud platform is the ideal development environment enabling us to start very small and simple but always keeping the possibility of scaling up and connecting more and more components (see figure).
Making rail and intermodal freight transparent and more efficient is not only helping the supply chain of the stakeholders involved. Studies of the European Union showed that if we were able to put 4% more freight in rail transport, this would immediately result in more than 9% less road transport! Thus, making rail freight more efficient will drastically help us in reducing our emissions and improve our congestion and mobility problems.