Pharma Production: Preparing for Serialization

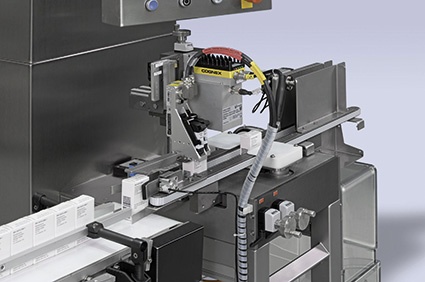
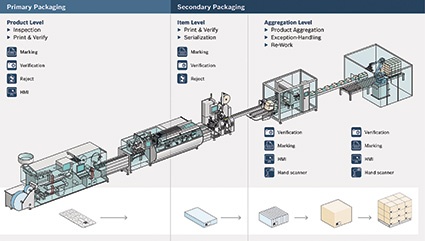
This year is an important year for the serialization of pharmaceutical packaging. Time is pressing, as numerous laws and guidelines are coming into effect all over the world. While some countries are still discussing how to transpose their guidelines into legislation, others are already well on their way to implementation. Pharmaceutical manufacturers are facing the challenge of finding suitable technologies, as well as connecting them with their production and packaging processes. A multi-layer machine and software concept undoubtedly is the safest approach.
Barack Obama’s signature of the “Drug Quality and Security Act” (H.R 3204) in November 2013 set the pharmaceutical industry in motion. The act grants the US Food and Drug Administration (FDA) more authority to advance the long-awaited system for pharmaceutical supply chain integrity. The FDA aspires to apply a standardized code identifier (standard numerical identification, SNI), more precisely a 2D data matrix code to the packaging of all prescription drugs. As of today, complete implementation including nationwide, public databases will presumably be due in 2023/2024.
In parallel, many other countries, for instance Brazil, China and Argentina, are busy developing and implementing new guidelines and laws. The Brazilian national authority for medical assessment ANVISA published a resolution in 2013, which is supposed to be implemented by December 2016. The Turkish serialization program ITS even mandates the serialization of all over-the-counter (OTC) and prescription drugs with a 2D data matrix code from production right through to patient level.
EU Directive with Additional Safety Layer
The European Union’s directive 2011/62/EU (Falsified Medicines Directive) was enacted in 2011. It stipulates the adoption of encoded packaging with unique serial numbers for almost all prescription drugs. Similar to many other countries, the serialization feature is a 2D data matrix code. It contains the code of the pharmaceutical manufacturer, a randomized serial number, the batch number and the expiry date, as well as a national number for reimbursement, if applicable. Prescription drugs and some OTC products will presumably be ready for verification in pharmacies by the second half of 2018.
At the same time, the EU demands a second level of security in form of tamper-proof closures, such as integrity seals or glue safety closures. They clearly indicate whether a package has been previously opened or tampered with. While some countries such as Italy and Belgium already have vignettes on the outer packaging, and France has even been applying a 2D data matrix code for some time, the main goal of directive 2011/62/EU is an EU-wide harmonization of legislation, as well as the applicable codes and seals.
Learning from the Automotive Industry
In the coming years, the pharmaceutical industry will face huge challenges. Drug producers are required to apply the respective guidelines within a given time frame. And this implementation is not going to be an easy task. Most companies will not be able to avoid developing and applying a global strategy for a consistent serial number assignment first. This requires solutions that are compatible with in-house processes, leading to the adaptation of often highly demanding packaging processes. Furthermore, new processes must be established for both management and storage of serial numbers.
Track & Trace systems have been successfully applied in the automotive industry for many years, especially to trace security-related parts such as brakes or steering components. Bosch Packaging Technology has adapted this know-how to suit the demands of the pharmaceutical industry. The requirements can be subsumed in a single key word: “modular”. A Track & Trace system should not only be able to mass-serialize the packed product in the sense of printing a code onto each pack. These codes also need to be verified unambiguously. Moreover, the packs are usually also equipped with a label or integrity seal, before the next packaging layer is added. The entire process needs to be controlled, and the data retrieved at any time. Only this way do producers – and later on the issuing authorities and legislators – have an exact overview of all process steps.
From Application to Enterprise Level
Serialization and aggregation present the IT departments with particularly demanding challenges. Not only must the packaging processes be synchronized with the newly integrated procedures. At the same time, entirely new processes have to be developed for the consistent and safe management and storage of serial numbers. The integration of packaging machines into these new procedures is an essential component of each serialization project. It requires careful planning to unambiguously and permanently store the serial numbers at the required integration level – from application level, line process and line management through to production and enterprise level.
Individual components such as printers and cameras are situated at the application level. The central HMI operates the modules and documents all data. To control both operating condition and data at any time, the connection between the physical machine level and the control software must be integrated across many stages of the company’s IT. The MES (Manufacturing Execution System), for instance, can function as a translation platform between the machine and the EPR (Enterprise Resources Planning) system and map the entire production area.
The Track & Trace system should be able to evaluate data in real time and answers the following questions: Where exactly is which product located? Which information is available about this product? This includes information on the code content, the current overall aggregation and production status, as well as quality data such as possible error patterns and weight indications. All results are reported to superordinate ERP systems on the enterprise level.
Facilitating the Implementation
The CPS (Carton Printing System) 1900 with Tamper Evident labeler, for instance, shows how Bosch Packaging Technology has transferred and expanded the Track & Trace principle from the automotive industry to pharmaceutical applications. The modular system prints up to 300 folded cartons per minute and applies additional safety seals. To protect the packaging and its content from manipulation, both side flaps of the folded carton can be sealed either from the top or bottom and the seal’s presence can be checked. Once the tracking data has been printed onto the package, it is automatically verified by a camera system that records every single printed character.
Equipped with a central HMI, the CPS transforms into a complete solution that centrally manages and configures all production, printing and layout data. Based on a generic, object-orientated and result-based software platform, the system can be extended by all requested aggregation levels, including bundling, shipping cartons and pallets. Subsequent upgrades of existing packaging lines are also possible.