Double Mechanical Seal vs. Magnetic Coupling
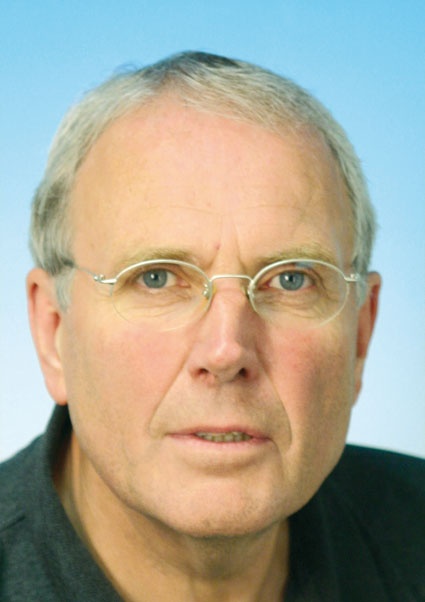
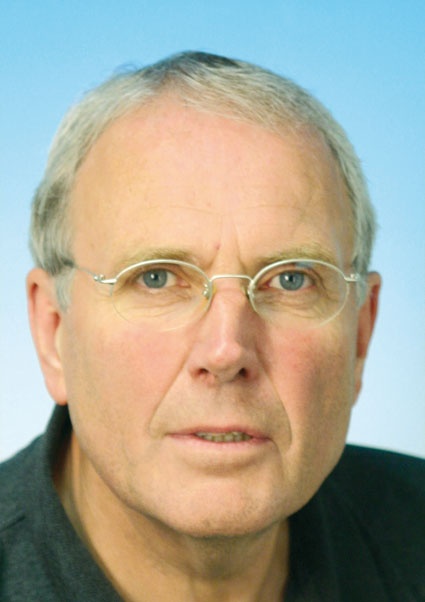
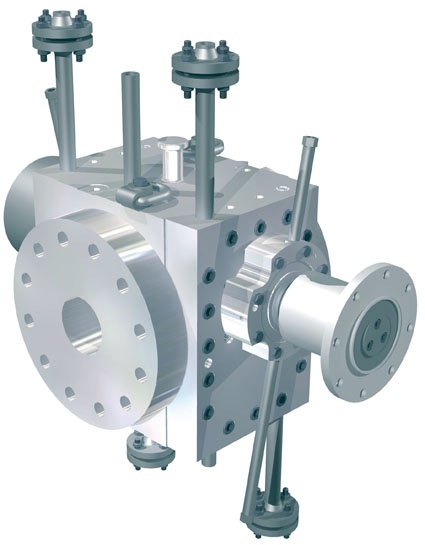
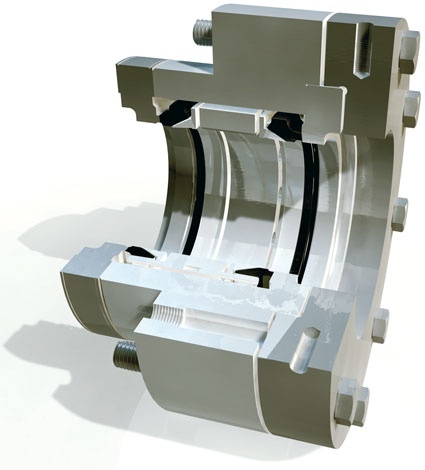
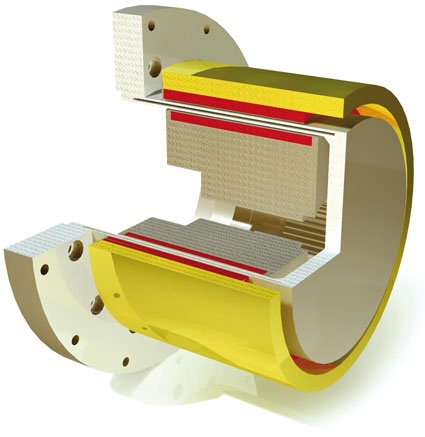
In industry today topics such as safety and the protection of the environment are a constant companion during the selection of system components. The usage of gear pumps is also defined by directives such as TA Luft (German Technical Instructions on Air Quality Control) or ATEX. In particular, the sealing systems used must meet very high requirements. Decision criteria such as maintenance costs and system availability also affect the usage of a seal.
A medium-sized business faced a major challenge. Our customer wanted to pump a polymer in an environment with very high safety requirements. The throughput per pump is 35,000 kg/h at a pressure of 6 bar and an operating temperature of 240 °C. In this system the material is pumped with viscosities from 500 - 2500 mPas.
In comparison to other plastics, the polymer is very expensive. The challenge was to enable the pumping of the product with minimum losses while maintaining the quality of the material. Furthermore, the molecular structure of the polymer is very sensitive to temperature fluctuations.
While on-site, our customer consultant found out that the customer wanted a "single pump concept". For cost reasons the customer did not want a "standby" pump. This meant that all possible sources of faults had to be eliminated in advance, as in the event of a failure there would be no replacement component.
First the organization had to decide on a pump type. For this purpose the customer consultant explained the principle operation of the gear pump and its advantages. Even the low pulsation pumping was convincing: the gaps between the teeth on the rotating gear shafts fill with pumping medium and transport it along the housing wall to the pressure side. In the case of gear wheels that engage, the medium is displaced and pumped to the outlet pipe. During this process little energy is added to the product, the temperature increase is very low and therefore ensures gentle pumping. As a result the quality of the polymer and the end product is safeguarded. Unlike the quick decision for a gear pump, its design was a little more difficult to define.
The application limits defined made it possible to use two different seals. The customer had the choice of a double mechanical seal or magnetic coupling. To meet the requirements to the best possible degree, various criteria were considered and discussed jointly.
ATEX and TA-Luft Directives
In general, it must be ensured that a potentially explosive atmosphere is avoided in an ATEX environment, or, if this is not possible, that there are no sources of ignition with equipment used in this zone. TA-Luft defines certain limits on the emission pollutants for environmental reasons, and defines technical requirements to meet these limits.
Based on these two directives, the seal types can be considered as follows: the main components of the double mechanical seal are two parts that slide against each other, the sprung seal ring and a mating ring. One of the two rings sits rigidly in the gear pump's housing, the other is fastened to the rotating shaft with the aid of fixing pins. As a rule an O-ring is used to additionally seal the shaft. To comply with the data relevant for TA-Luft, a sealing medium is used. The pressure in the sealing medium is always higher than in the pump. That way it ensures that in the event of a leak, the sealing medium flows into the pump cavity or into the surrounding environment, but the medium to be pumped never leaves the pump cavity. The sealing medium also contributes to minimizing the friction at the sliding surfaces. If the seal is correctly sealed and level monitoring is used, this seal is ATEX and TA-Luft compliant.
Optimal sealing for media of relevance for TA-Luft in the low viscosity range is provided by the magnetic coupling. If used it is possible to avoid entirely the usage of the shaft seal and therefore any dynamic sealing points. The product cavity in the pump is hermetically separated from the surrounding environment by a containment shell. The torque is transferred from the motor shaft to the pump shaft without any physical contact by powerful permanent magnets, which are outside the containment shell. The pump shaft is inside the containment shell. The sealing liquid is not required for the magnetic coupling, an aspect that considerably simplifies their handling compared to seals with sealing. Given correct design and installation, there is also nothing against operation in ATEX applications.
Maintenance Costs
The magnetic coupling offers a further advantage in relation to the maintenance costs. It is practically maintenance-free and the availability of the pump and therefore the entire system is correspondingly high. The avoidance of rubbing sealing elements minimizes the wear to zero. The double mechanical seal has a higher level of abrasion, as the moving part rubs against the fixed part. The higher procurement costs of the magnetic coupling in comparison to the "life cycle costs" of the double mechanical seal are amortized in approximately one to two years. The two solutions are equivalent in relation to the risk assessment with no major differences.
Experience
In the past the customer found that the majority of pump failures occurred on pumps with mechanical seals. Due to the "single pump concept," the decision was quick: a thermorex RT140 gear pump with magnetic coupling was integrated into the system. The magnetically coupled gear pump has been running for two years without problems.