Circular Economy
The chemical industry is on the threshold of a new era – the age of circularity. We asked industry experts to share their opinions on this transformational topic.
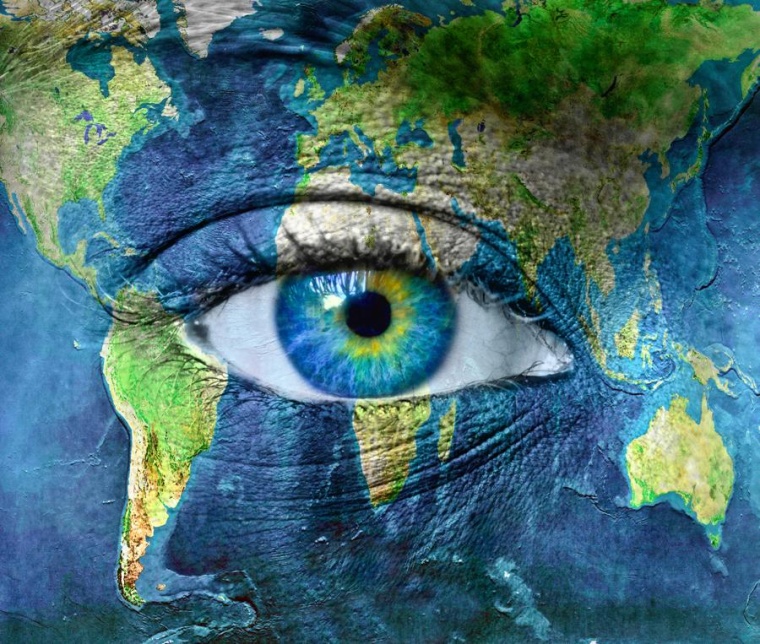
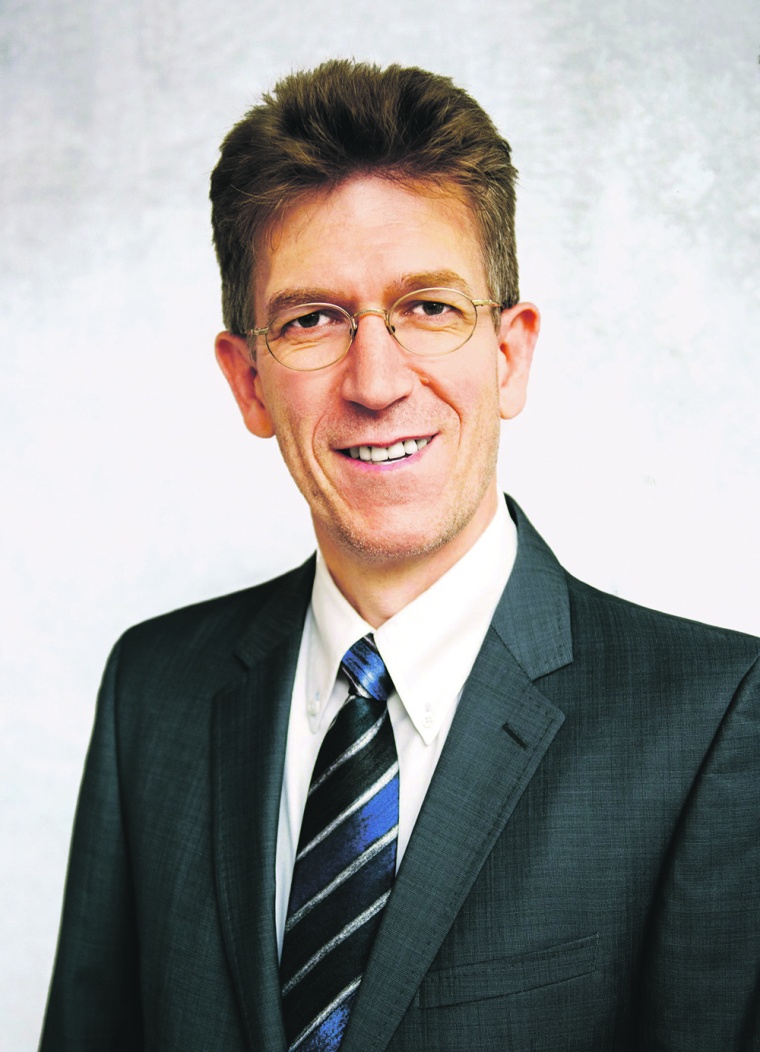
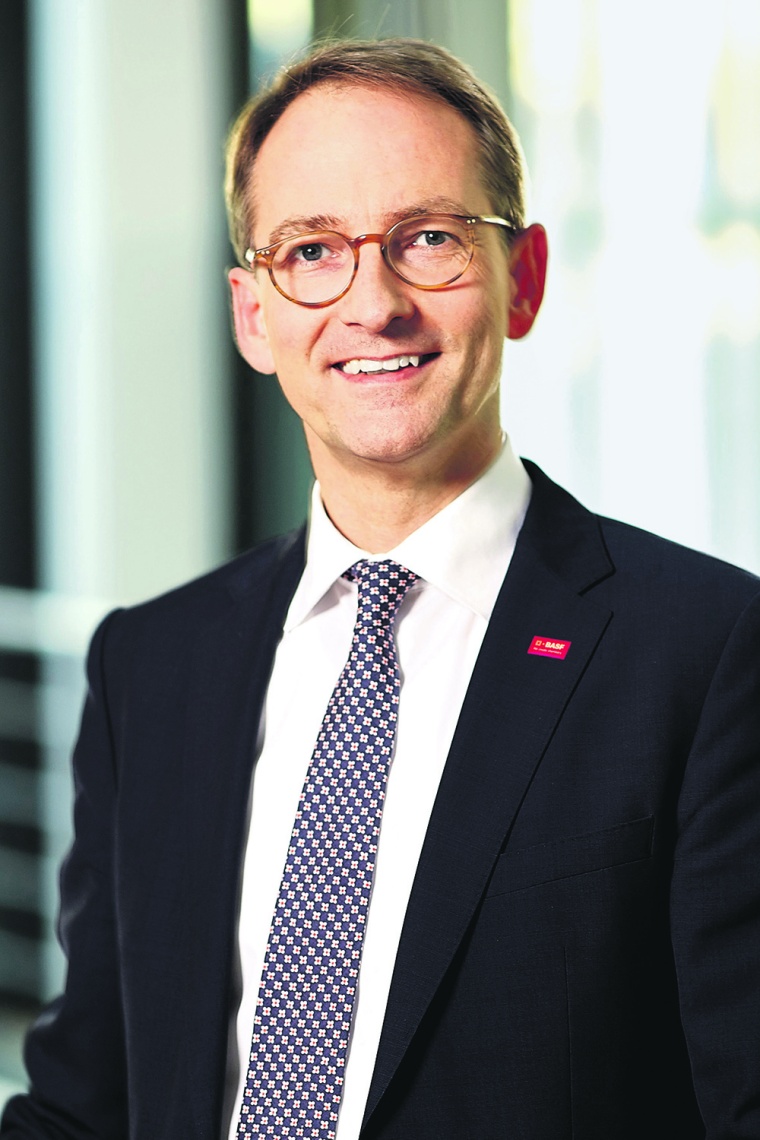
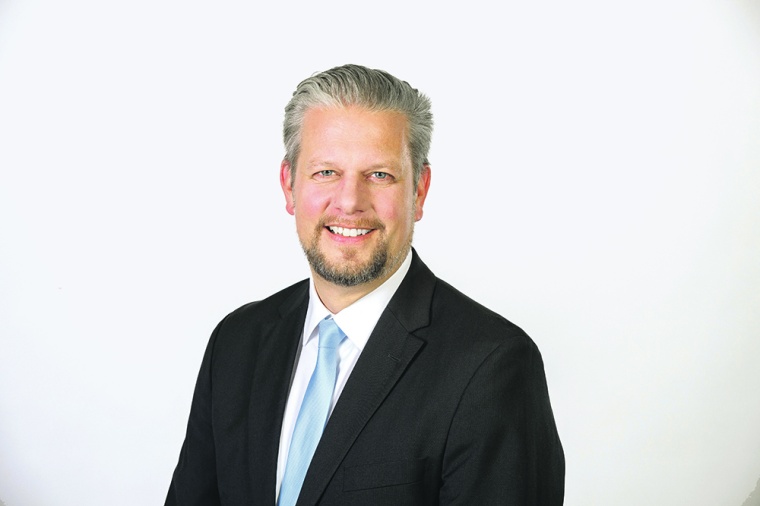
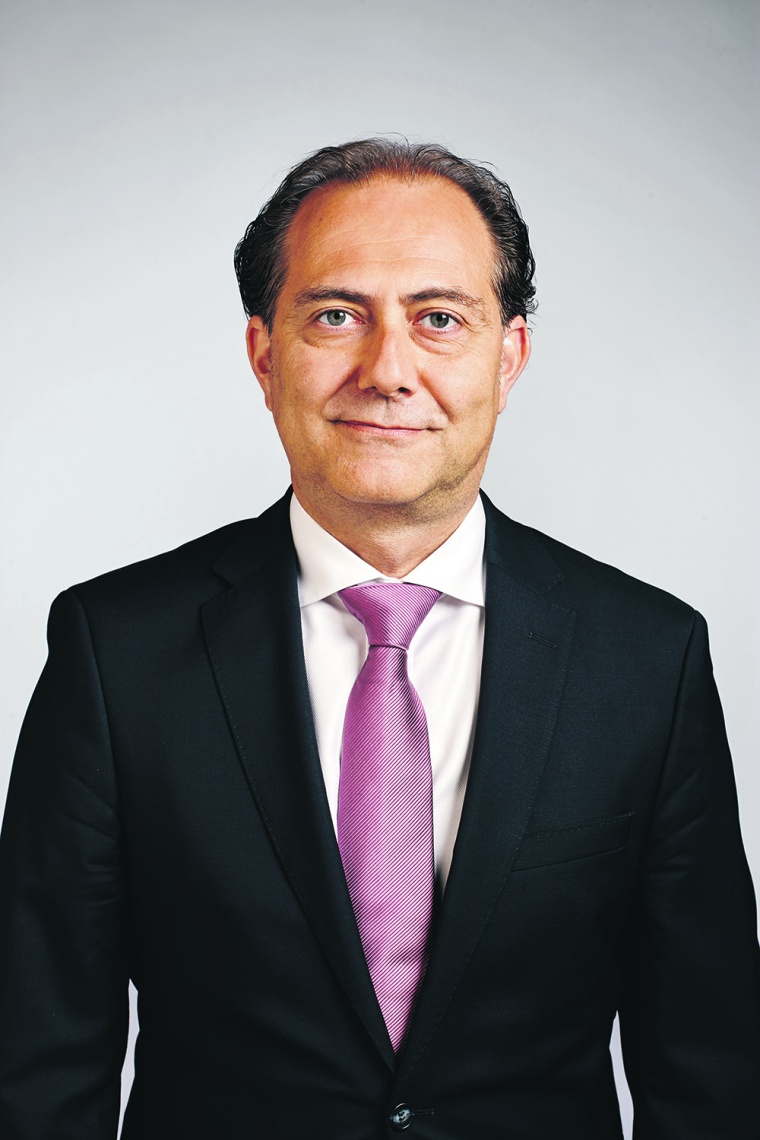

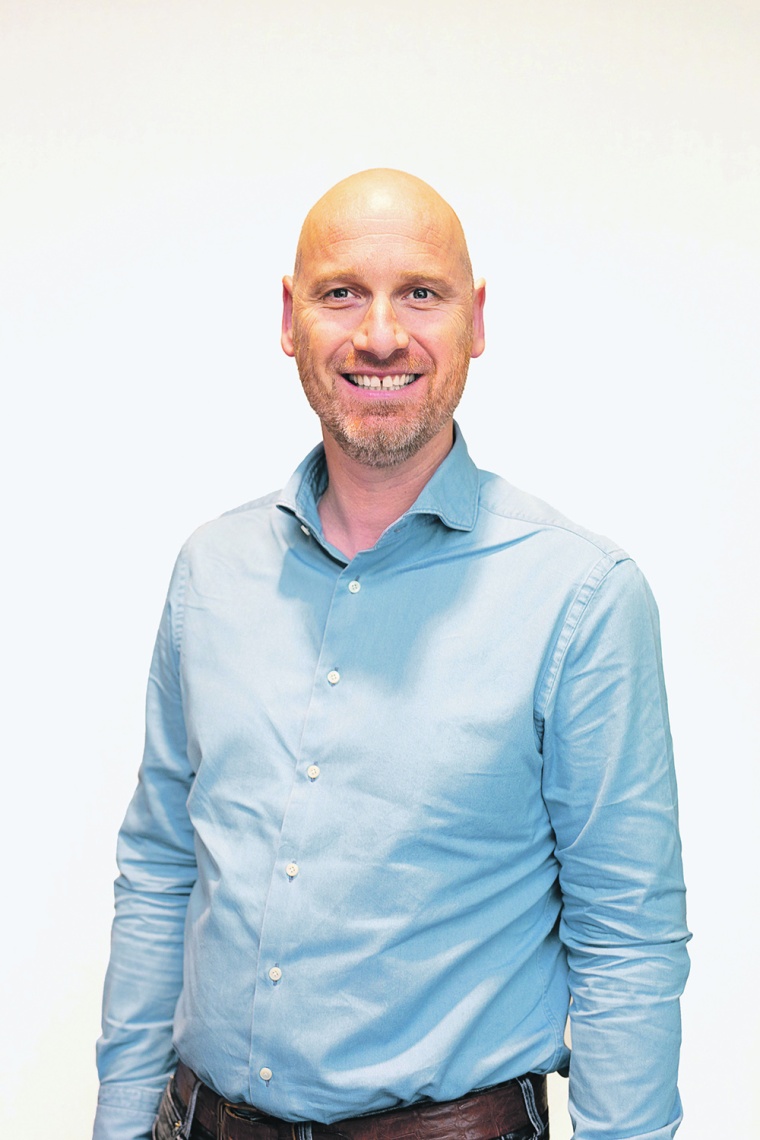
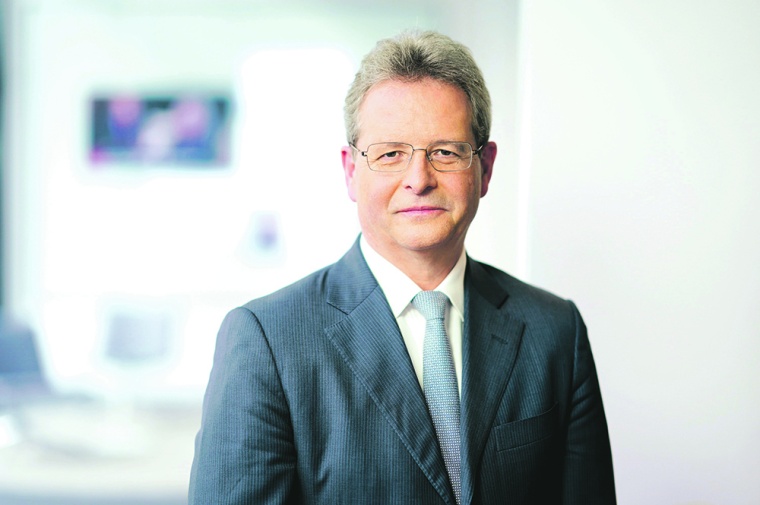
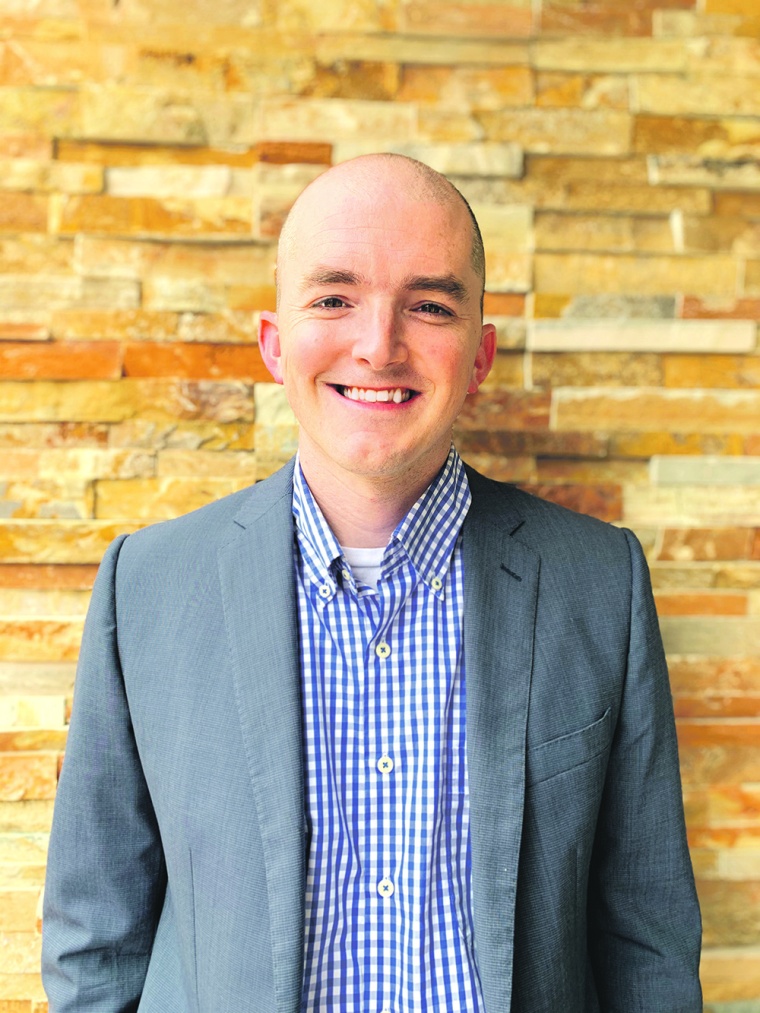
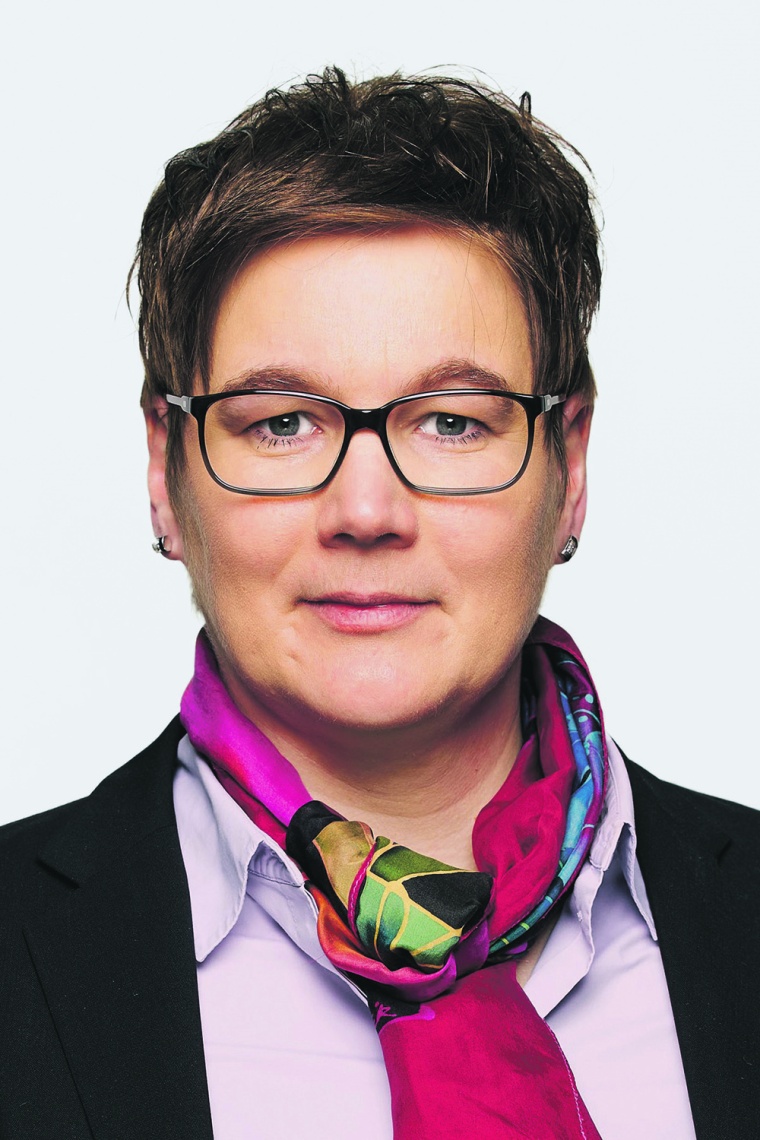
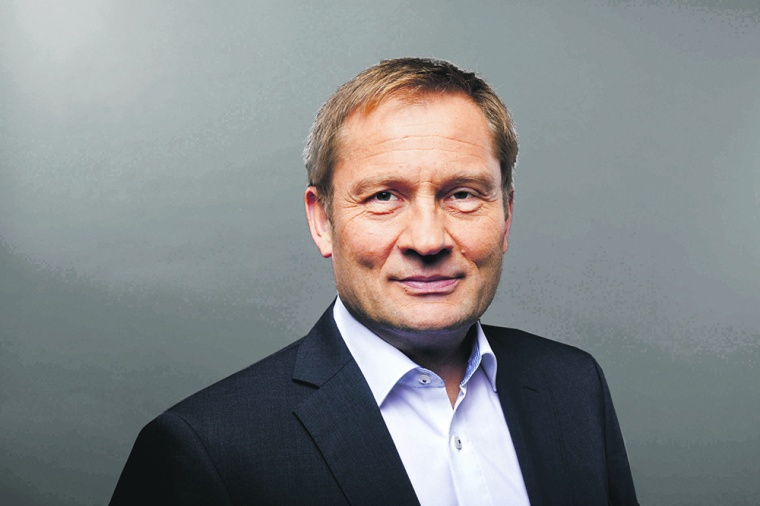
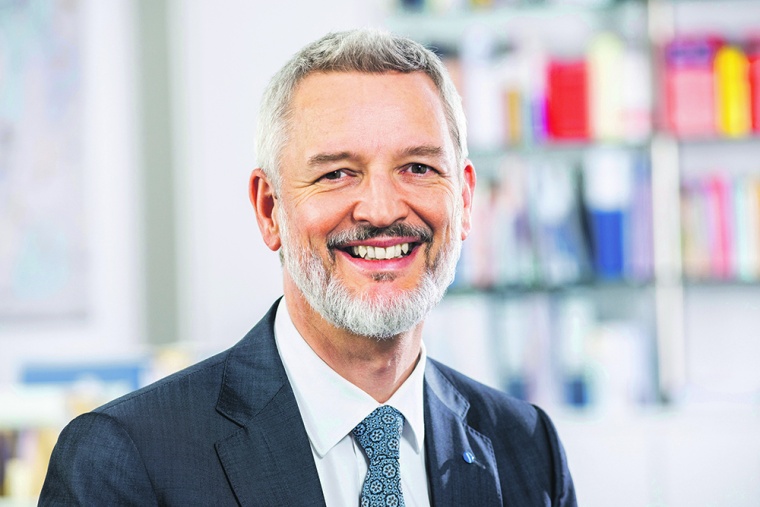

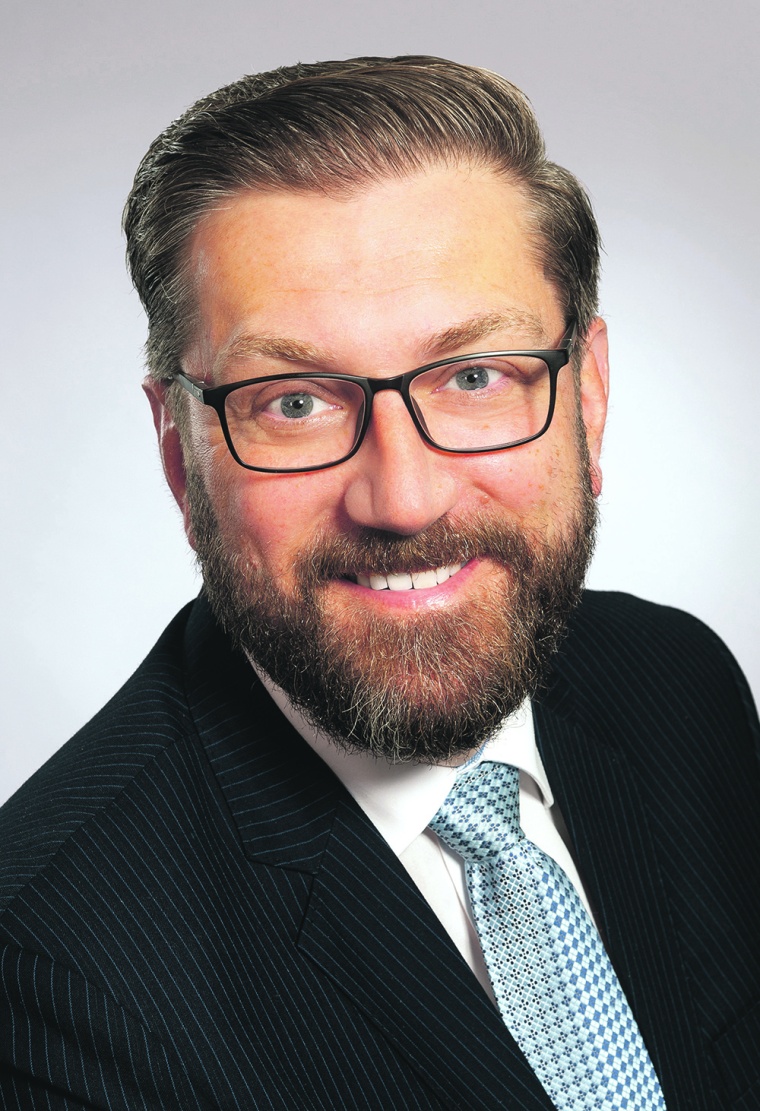
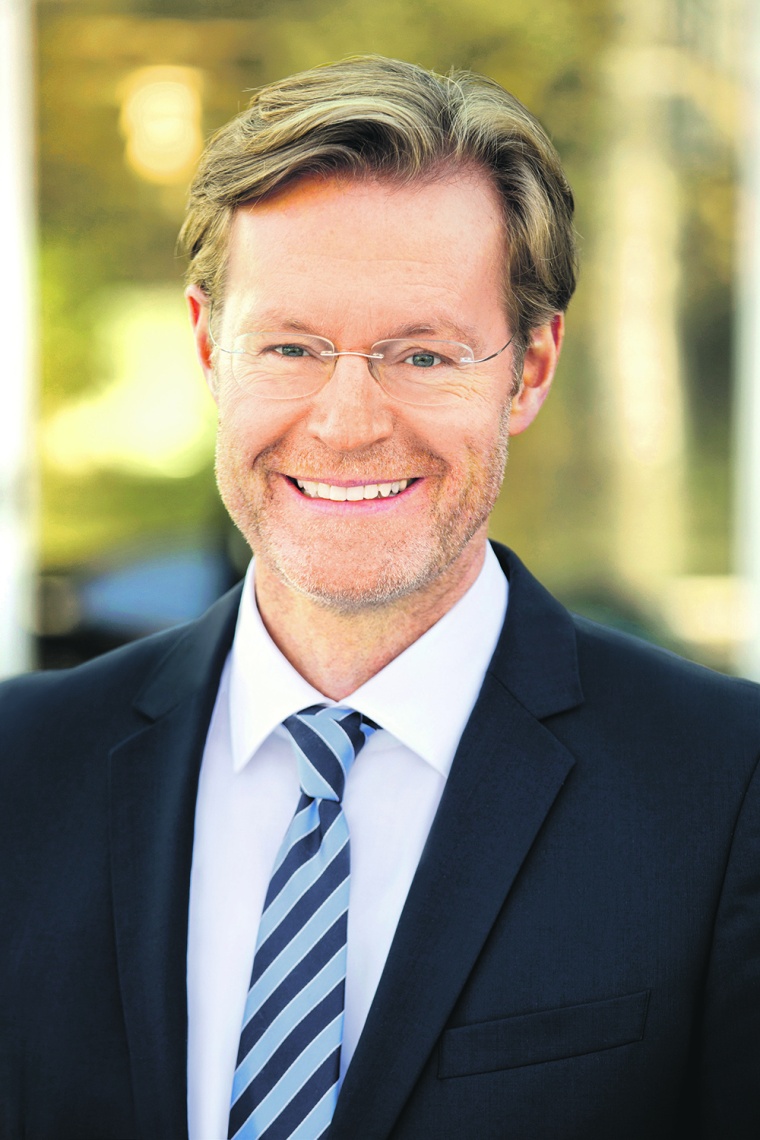
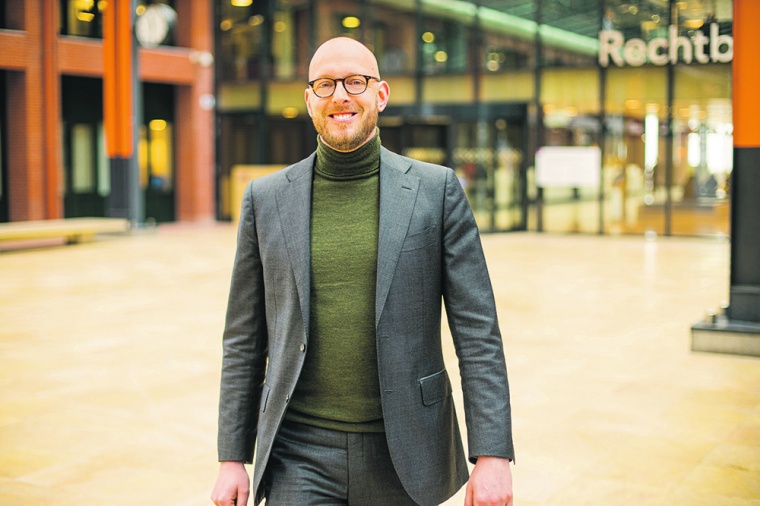
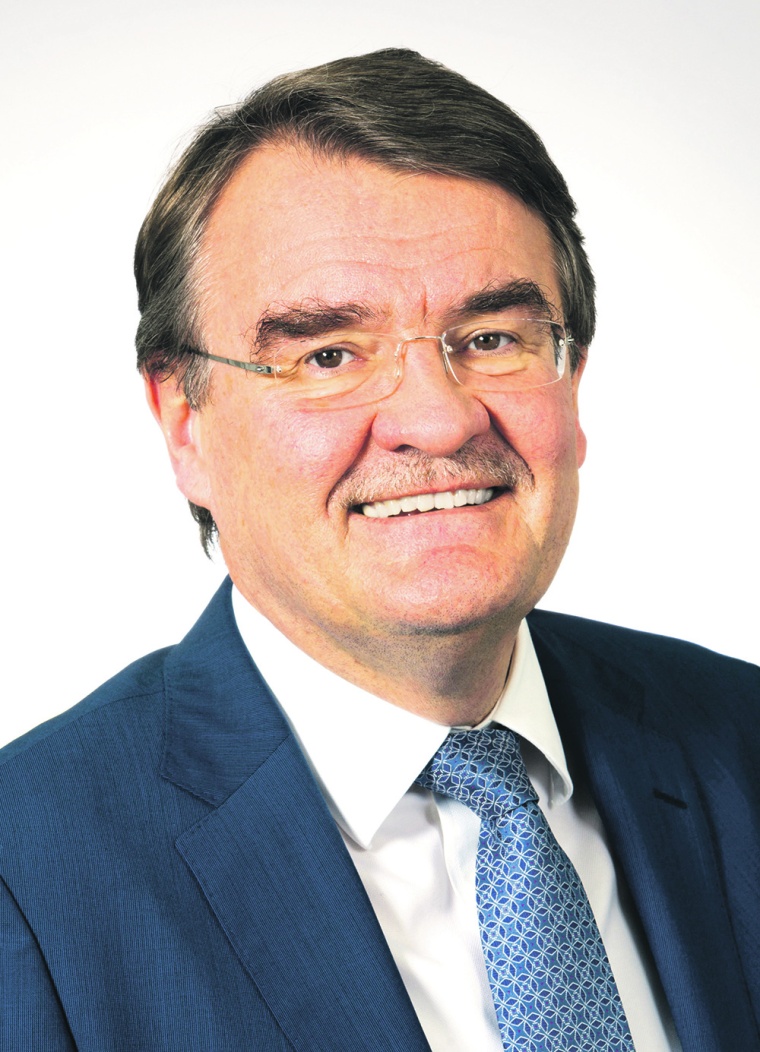
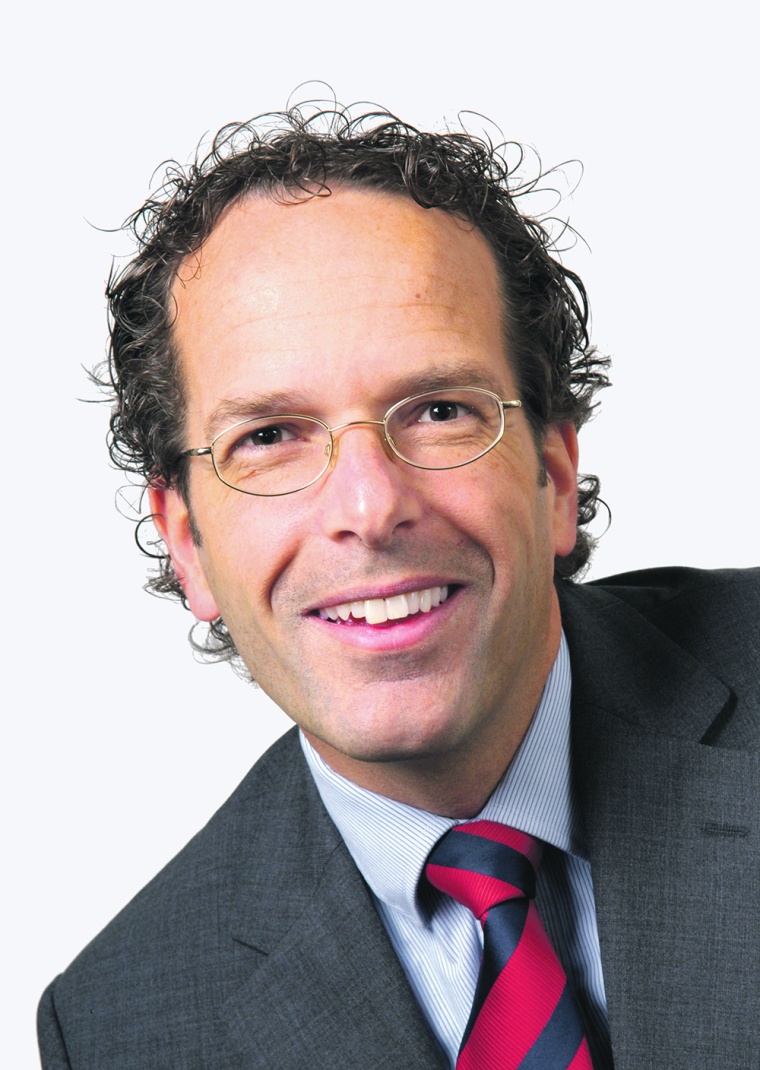
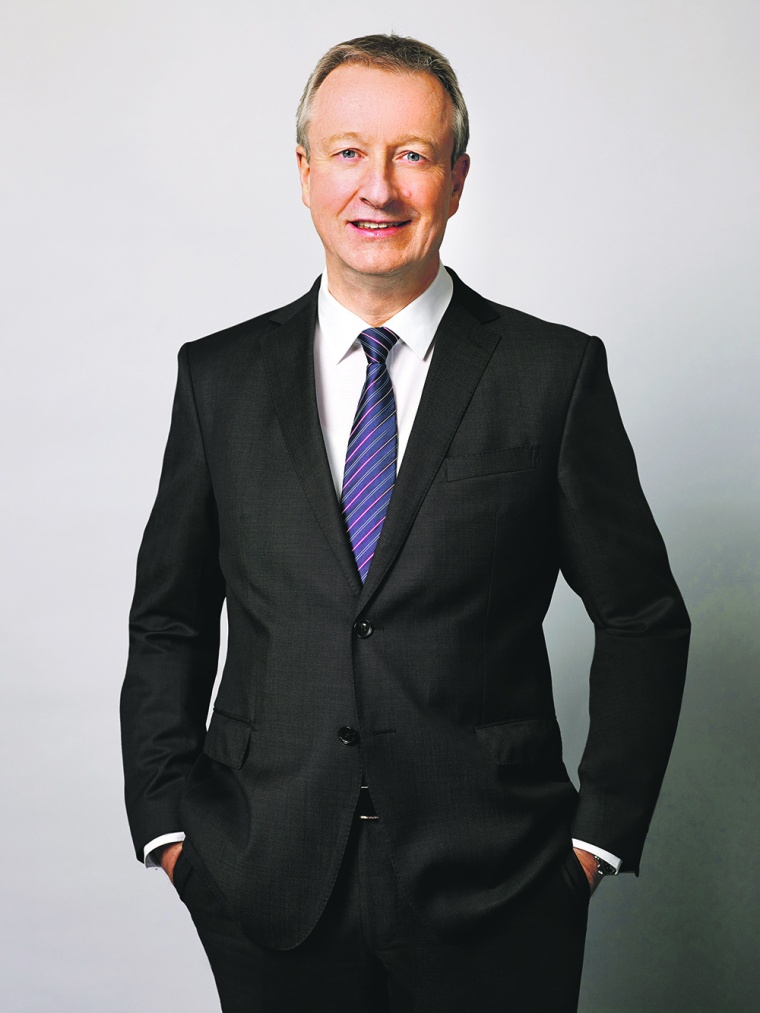
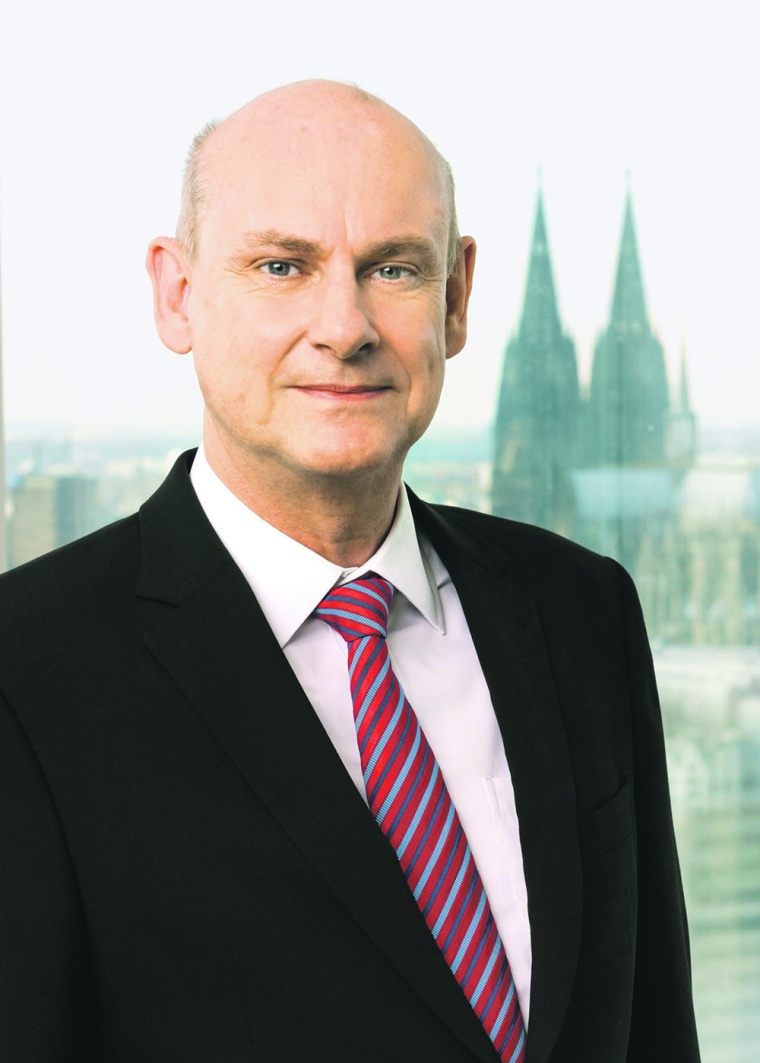
The chemical industry is on the threshold of a new era – the age of circularity, where products are based on closed-loop value chains and made from renewable or recycled raw materials.
The technical, political and social conditions for progressing on this path are encouraging. However, this development is not a sure-fire success. Whether it will be successful depends on the attitude with which the key players along the value chain approach the problems.
The shift requires intensive cooperation along the value chain and across industries. There is little doubt that the chemical industry plays an essential role in establishing the circular economy model and closing loops. The time is now for chemical companies to (re-)define their role as non-traditional opportunities and new players emerge. The circular economy is here to stay, with exciting opportunities for the chemical industry to stand out!
These are excerpts from our feature articles published in this issue (see previous pages).
CHEManager asked industry experts from well-established players along the chemical/plastics value chain to share their opinions on challenges and opportunities of the circular economy. We proposed to discuss the following aspects:
- Public criticism of our industry in the context of the climate and environmental debate.
- Alternatives to the circular economy approach.
- Ways to support the circular economy concept.
- Challenges that have to be overcome on the way to a circular economy.
Read the insightful answers of the experts here.
Recycling Plastics into new Raw Material
Martin Jung, President of Performance Materials, BASF
Currently the key basic steps of chemical production produce substantial greenhouse gas (GHG) emissions. To address GHG emissions, we will pursue breakthrough technologies and utilize renewable energy while focusing on increased processes and energy efficiency. Our Carbon Management R&D program has a project that reduces CO2 emissions from steam cracking by up to 90% using electrification of exothermic processes such as the steam cracker.
As a plastic producer, BASF aims to contribute to a better use of plastics as plastic is a valuable resource that can provide benefits to our society if handled appropriately at the end of its life.
Plastic pollution is a multifaceted challenge which calls for well-orchestrated efforts from consumers, businesses, partners in the entire value chain and policymakers. Genuine impact can be made with an infrastructure to collect and process plastic waste, a regulatory system that supports the process, and motivated people who change their disposal behavior.
As a founding member of the global Alliance to End Plastic Waste (AEPW), BASF is dedicated to advance solutions to eliminate unmanaged plastic waste in the environment. Some examples include recycling TPU from worn-out shoes; scaling our ChemCycling project quickly where we transform mixed plastic waste into valuable products; producing engineering plastics from post-consumer recycled carpets or recycled PET bottles.
BASF covers substantial parts of several plastic value chains from monomers to polymers and their formulated specialties including a broad portfolio of plastic additives. This offers numerous opportunities to close circles of a different size, utilizing our expertise mainly for chemical recycling. Our ChemCycling project, for instance, is to build closed circles to recycle plastics into new raw material. We are developing a recycling process of polyurethane foams while looking to increase the use of new bio-based monomers. Collaboration with a partner to develop solutions for plastics traceability and circularity as well as the investment in a carbon recycling company – all these are prime examples that demonstrate we put this concept into action across the entire value chain.
Designing for Recyclability Requires Innovative Approaches
Lucrèce Foufopoulos, Executive Vice President Polyolefins, Innovation & Technology, Borealis
Collection, waste management and innovation are key factors in closing material loops on the way to a circular economy. In order to stop marine littering, the focus needs to be on collection and waste management. We know that many items that are leaking into the environment today are perfectly recyclable but unless we can collect them, the recyclability & technological advancement will be in vain. To reduce leakage of waste and plastic waste and accelerate the transition of our industry towards a more circular one, we need to focus on collection and waste management. We need collection systems with incentives to make them work. Collecting the plastic is the essential first step in building a circular economy. Collecting in the right way is critical to clean streams of inputs into recycling infrastructure, and is thus a strategic component of the circular economy. Production and use of plastics do not inherently cause pollution. It is the lack of collection that creates pollution, not the plastic itself. It is therefore paramount we address with speed and focus the waste collection issue to develop towards a true circular economy of plastics.
Innovation is just as crucial in closing the loops. Borealis is creating value with its new plastics recycling technology brand Borcycle, which can be used to manufacture high-quality compounds made of recycled polyolefins. One Borcycle grade launched last year contains 80% rPO and can be used for visible appliances parts. Innovative approaches are also required if designing for recyclability is to become the default mode. Again here, Borealis is working with its value chain partners to penetrate the EverMinds mind-set of recycling, re-use, and design for circularity.
On another level, Borealis has invested in state-of-the-art upgrades of our own recycling plants, including Wildon, Austria in 2019, where we increased our recycling capacity by 60%. We are also excited about our ReOil collaboration with OMV, which is advancing the chemical recycling of post-consumer plastics.
In essence, in order to allow our industry to accelerate its conversion towards a more circular industry and address the plastic waste issue, the following key issues will need to be addressed:
- The right kind of collection system that is efficient, low cost but also effective in feeding circularity.
- The right kind of recycling - to minimize environmental impacts and to produce high quality, high value outputs.
- The right kind of demand from the market, with the appropriate pricing for clean, recycled content.
- The right economics for collectors, recyclers and for customers of recycled materials.
Driving the Chemical Industry towards a more Sustainable Future
Christian Kohlpaintner, CEO, Brenntag Group
The Circular Economy approach is an important driver to rethink the production, usage and end phases of products. It is needed to reduce waste and to reflect the scarcity of resources. It is thus an essential element to drive the chemical industry towards a more sustainable future.
Brenntag as the leading chemical distributor connects an enormous number of producers and users of chemicals. Therefore, Brenntag will play an active role towards a circular economy. We do this already to some extent as we sell and promote reused as well as recycled chemicals (e.g. acids and solvents) and recycled plastics. By doing so we help our customers to reduce waste, extend the lifetime of products, and improve the ecological footprint.
For a stronger move towards a circular economy we see different challenges, like the scarcity of certain recycled materials in high quality, or strong price competition with virgin materials and also regulations which make it difficult to use reused or recycled materials for certain applications.
Circular Solutions Are Economically and Environmentally Viable
Christian Haessler, Global Circular Economy Program Lead, Covestro
To address global challenges such as climate change, resource depletion and the needs of a growing world population, a systemic change of our economy and ways of value creation are necessary.
It is essential to find and implement sustainable practices to stop environmental pollution and the overexploitation of the world’s increasingly scarce resources to be able to meet these challenges. At Covestro, we are convinced that a transition to a circular economy is the right answer.
As a raw materials manufacturer, we play a key role in enabling circular solutions for a broad range of industries, from electronics, to health care, construction and mobility.
Mimicking nature as a blueprint for the circular economy, we are focused on integrating renewable resources into our production processes and developing innovative recycling pathways for our materials. To realize this, we work closely and exchange with various actors: our customers and suppliers, research institutes as well as totally new players in the value cycle. Our goal is to ultimately move away from fossil-fuel resources by introducing a supply of alternative raw materials.
With our breakthrough in using CO2 as a resource for polyurethane applications – our product cardyon – we have proved that circular solutions are economically and environmentally viable. Ultimately, we also aim to develop innovative energy-efficient technologies to convert materials at the end of their lifetime back into their building blocks and use them again as a raw material source in production. In order to deliver on the challenge of recycling, we are putting our brightest minds to work to develop new solutions which bring those technologies to the market in a fast and efficient way. We are confident that in collaboration with partners and by prioritizing new technologies, we can lead our industry towards a circular economy.
Leading Efforts to Find the Feedstocks of the Future
Marco Jansen, Circular Economy & Sustainability Leader in Europe & Asia, Braskem
We are now entering a crucial phase that will determine how plastics can respond to our societal and environmental needs. We know the scale of the challenge ahead of us, and it is up to us to find ways to deliver innovative and sustainable materials that can meet the demands of our customers, the public and policy-makers.
Developing and bringing “I’m green” to the market was one of the first steps Braskem made on our journey towards the circular economy. It was 10 years ago – perhaps before the concept was as mainstream as it is now – that we launched our bio-based polyethylene. The revolutionary idea was to replace the conventional fossil-based building block, with a plant-based alternative.
As a company operating in that space between raw material sourcing and the brand owner, Braskem can play a fundamental role in developing a new and more responsible approach. I see our role as follows: to lead efforts to find the feedstocks of the future. This vision is something I call a “low carbon circular economy” – resource efficiency primarily determined by our ability to reduce or even eliminate a product’s carbon impact. We’re combining sustainable bio-sourcing with increased use of post-consumer material, so that we can offer our customers a range of materials that achieve the twin goals of, one, fighting climate change, and two, increasing recycling.
That’s why we have set out to develop plastic recycling technology, mainly by working with partners. Braskem has agreed to work with a number of market leaders to develop advanced recycling techniques, and last year we ran successful initial trials of pyrolysis oil – derived from plastic waste feedstock – in one of our Brazilian crackers.
For Recycling to Be Successful, it must Be Economically Viable
Anno Borkowsky, Member of the Board of Management, Lanxess
The chemical industry has substantially expanded its production volume during the last 30 years. At the same time, energy consumption was reduced by about 15% through increasing efficiency, innovation and technological upgrades. Also, greenhouse gases have been reduced by 48%. We need to continue on this path and Lanxess is fully aware of its responsibility in this regard. We support the transformation towards a sustainable, resource efficient and carbon neutral economy with its activities and products. We have therefore declared to become climate neutral by 2040, and already today, our products enable climate-friendly solutions for new mobility and other technological areas.
Another key issue in this regard is the circular economy concept, to which the chemical industry can make significant contributions, e.g. by implementing reverse reaction processes that allow “chemical recycling”. We are intensively working on respective projects. But chemical recycling is only economically feasible under certain conditions. Here, politics must create the right framework. Effective incentive systems for the transition from the use of primary feedstock to recycled feedstock are needed. In particular, chemical recycling should be promoted to the same extent as mechanical recycling. For recycling to be successful, it must be economically viable. And last but not least, processes need to be developed in cooperation with all stakeholders involved in the value networks.
Various Approaches to a Plastics Circular Economy
Jens Schuermann, Manager of Segment Marketing and Technical Solutions, Biesterfeld Plastic
We use our technical expertise to advise our international customers and suppliers and help them to develop innovative solutions. Thanks to our extensive product portfolio, we can influence the design of new applications and we pursue an integrated approach to ensure their recyclability. As a signatory to the UN Global Compact, we believe that every product is still of value after its primary use.
Developing concepts and technologies that enable plastics to be reused after their primary use is an area in which all industry sectors are working hard. However, given the sheer variety of the associated challenges, the result won't be a single patent formula.
Currently there are two main solutions: mechanical and chemical recycling. Today our partners are focusing more on mechanical recycling, i.e. the collection and processing of assorted raw materials or waste materials which cover the whole plastics pyramid, from standard polyolefins to recyclable high-performance polymers.
This is where our consulting services come in. We work with our partners to develop solutions tailored to a given application. On a case-by-case basis, we evaluate what costs and benefits need to be taken into consideration from an economic and environmental perspective and how they can be optimized.
Essentially, the separation and reuse of materials gets more difficult the greater the number of materials used is. Thus, it could be advantageous, to develop products from a single polymer base or from related materials if this makes them easier to recycle. The processing method used (e.g. multi-component injection molding) and subsequent processes such as optimized joining techniques also need to be considered.
Since not all waste streams are recyclable, industries are focusing a great deal of effort on chemical recycling solutions. This involves transforming plastic waste into raw materials and/or monomers, which can then be turned into polymers of the same quality as prime plastics.
In our active role in plastics value creation, we are committed to environmental, economic and social sustainability. You can read more about our commitment in our annual sustainability report.
Driven by the Transition from a Linear to a Circular Economy
Carsten Larsen, Managing Director, Dow Nordics, Commercial Director Plastic Circularity EMEA & APAC, Dow
Modern society has come to rely on plastic’s social and economic benefits. But plastic’s low-cost, everyday presence in our lives means we take it for granted and it is often thoughtlessly discarded, resulting in the global plastic waste issue we face today.
As one of the world’s biggest plastics manufacturers, we are responding to the plastics waste challenge. We believe our future license to operate depends on ensuring that all parts of our portfolio are driven by the transition from a linear to a circular economy.
Helping this become a reality requires action at every stage, from manufacturing to stimulating new markets for recovery. We are constantly developing new initiatives to ensure plastics’ value is retained throughout its lifespan. We know we can have most impact in five key areas.
Designing with recyclability in mind: We are providing innovative design solutions that help brand owners deliver on their sustainability commitments by ensuring plastics are both functional and easier to recycle at end of life.
Mechanical recycling: We are improving the quality of recyclate from flexible packaging and last year launched Agility CE – a pivotal milestone in our journey to incorporate a high percentage of post-consumer plastic waste into our product offering, without sacrificing quality.
Feedstock recycling: The process of breaking down mixed waste plastics into their original form to manufacture new virgin polymers. Last year we announced a new partnership with Fuenix Ecogy Group and launched our first product made from pyrolysis oil feedstock.
Renewable feedstocks: Our partnership with UPM BioFuels is turning waste residue from paper pulp production into naphtha to produce bio-based polyethylene (PE).
Bridging solutions: We are working to find interim solutions to remove plastic waste from the environment in emerging economies, while advancing the circular economy where we can in the long term.
Need of a Changed Consciousness when Dealing with Materials
Jürgen Rietschle, Managing Director, Bodo Möller Chemie
This is not about an either-or solution, but about many components that should prevent to avoid the increasingly larger waste flows. The circular economy should play an essential role here. However, I consider it inevitable to think about the recyclable material plastic. I see an opportunity in a more needs-based production without surplus, smaller series provided with a higher value that is also perceived by the consumer. We need a changed consciousness when dealing with materials. Here, 3D printing could play an essential role towards a positive change. This is only one reason why we have decided to invest more in this market.
2) We must wait and see to what extent the coronavirus will keep changing consumer behavior in a lasting way after the crisis. When consumers take it for granted that all substances and materials are available at all times, it makes them inferior in their minds. The crisis has taught us to reconsider taking things for granted. I think that the industry has gone much further in many things than is the case with consumers and politicians. There are numerous sustainability projects when I think, for example, about using CO2 as raw material for plastic production or the increasing importance of the high-quality processing of recycled materials.
We keep checking our portfolio to adapt it further to market conditions, focusing on polymer compatibilizers in order to recycle them better, and on recycled HDPE compounds. Likewise, for the last 10 years, we have been noted experts in the additivation and stabilization of thermoplastic recycling materials. With our additives, we influence oxidative processes so we can make an important contribution to a part of the circular economy.
The biggest challenge is still in the material flows themselves, as they have come to a halt due to the corona crisis. In order to close the material cycle, it is necessary in many cases to switch to mono- instead of multi-materials. Part of conscious recycling is when those materials with good recycling characteristics are already considered during manufacturing. In order to better identify and track the flows of materials, digital solutions are necessary. Inefficient situations must be avoided to enable the circular economy to have the necessary future horizon.
Driving Sustainable Practices to Protect our Natural Resources
Kevin Norfleet, Senior Program Manager, Engineered Materials Sustainability, Celanese
As a global producer of basic chemicals as well as engineered materials and performance polymers, Celanese’s wide product portfolio covers most critical industries and applications essential for everyday living. We see sustainability and promoting a circular economy as a core part of our strategy and our future and so are honing our focus on three key areas: bio-based feedstocks, increased recycled content and materials designed for end-of-life versatility. By preventing the disposal of valuable materials and reducing the amount of new raw materials used in our environment, we can contribute to decreasing GHG emissions as well as waste.
As a leader in engineering thermoplastics, our strongest focus in our circularity programs is on producing high-quality materials made entirely or partially from recycled content, but we also offer many products with bio-content. Customers increasingly want solutions with recycled or renewable materials but also need to maintain high standards for performance and reliability. Celanese is committed to helping meet those needs. With experience and expertise across most end-markets, Celanese is helping customers meet complex material requirements with grades containing recycled or renewable content in the most cost-effective ways possible.
Through those product efforts as well as other advancements, we are able to renew and restore materials through all phases of our production. From 2013 to 2018 we reduced our solid waste intensity by 35% with over 40% of total waste recycled; reduced our greenhouse gas intensity by 28%; VOC intensity by 29% and global energy intensity by 15%.1
By establishing an ESG Council driving our environmental, social and governance commitment, Celanese continues to drive sustainable practices to protect our natural resources while helping our partners and their customers to do the same.
1 Note: Numbers are estimates and may be based on assumptions.
Partnerships Along the Value Chain Are Crucial
Bettina Siggelkow, EcoCircle Program Manager, Clariant
For answering the challenges of CO2 reduction and the scarcity of resources, the circular economy approach is inevitable. Circularity hereby should value plastic waste as raw material. This includes the full waste hierarchy, supporting reduction of plastic waste as well as recycling. Combining circularity and sustainability offers new product and business opportunities through a broadened scope of product properties.
Clariant offers products along the full plastic value chain, including mechanical and chemical recycling. To support the reduction of plastic waste, our experts support the development of concentrated product solutions, e.g. for home care and cosmetics. For reusing packaging Clariant additives increase the plastic lifetime, e.g. through light stabilization. Other additives support to increase the usage of recycled polymers from mechanical recycling, by keeping product properties and processing efficiency during the conversion. And finally, for dissolution and chemical recycling Clariant’s processing aids can be used in the purification steps.
Within Clariant we have defined circularity as one of the pillars of sustainability, with EcoCircle as the corporate initiative to enable a circular plastics economy. We can jointly develop, with our customers, new solutions by product expertise as well as using Clariant’s experience in agile innovation management techniques for co-creation. As we believe in the transformation towards a circular plastics economy, partnerships along the value chain are crucial and Clariant’s expertise in leading such partnerships will support the required change. Through joint development of new products, the primary focus on the intended use can be extended to additional advantages in their behavior within and beyond the end-of-use phase.
Chemical Distributors Enable Circular Economy
Robert Späth, CEO, CSC Jäklechemie
Circular Economy goes hand in hand with the global sustainability goals and became a key issue of EU politics recently. Chemical distributors as essential links in the supply chain deal with this topic since quite a while – long before it became so popular. If we look to the commodity business in Germany, there is a deposit return scheme for the packaging of chemicals. This, founded in 1996, established a closed loop for all drums, IBC’s and other packaging of liquids to enable multiple use. The reuse of packaging is one aspect of Circular Economy.
Many distributors like us are certified waste management companies and establish an important link in the recycling of chemicals. They offer the logistics to take back and collect used solvents or other chemicals for the recycling industry. In addition, distributors provide innovative business models like chemical leasing that strongly support the recycling aspect of the Circular Economy. If we look to the specialties business, there is a rising demand for renewable feedstock from our customers. Our task as chemical distributor is to find innovative new products that meet these expectations and promote them in the market. For example, there are coating hardeners whose carbon base is derived mainly from renewable raw materials. I see all these activities under the umbrella of the global Responsible Care initiative to improve health, safety and sustainability. As a result, chemical distributors enable Circular Economy.
Improved Possibilities for Recycling of Plastic Waste
Andreas Holzner, Global Head Business Unit Special Additives, Baerlocher
The plastics industry is facing perhaps the greatest changes in its history – driven by an increasing adoption of the circular economy approach. This trend is propelled by increasingly stricter global regulations and a growing consumer awareness for sustainability and the environment.
As a result, the plastics industry is seeking new technologies which will allow recycled plastics to enter new applications, or significantly increase the content of recycled polymers in existing products – but this is not as easy as it sounds. For example, recycling the film fraction of post-consumer plastics presents an obstacle. Even with careful raw material preparation in a modern recycling facility with state-of-the-art equipment, the end-product may only be suitable for simple applications.
The problem is the reprocessing, requiring melt filtration through fine filters to get rid of contaminants. There the high temperature inflicts so much damage to the polymer that it is left with very poor film blowing properties. To avoid this, it is key to re-stabilize the recyclate to protect the polymer.
Sustainability has always been an issue for Baerlocher – we played a formative role in the transition to Ca-organic PVC stabilizers. It is hence only logical that we devote our innovative strength to the recycling sector as well. During last year's K show, the company was able to present several case studies. Leveraging Baerlocher’s Baeropol T-Blend Resin Stabilizer, KNF Flexpak, a US packaging manufacturer, can now run 100% recycled film using post-industrial polyethylene film, helping to improve sustainability and reduce costs. The technology resolved issues of variable film quality by preventing gels, bubble instability and haze.
In a live demonstration at the exhibition grounds, plastics processor APK and Erema, a recycling equipment manufacturer, showcased how adding Baeropol T-Blend stabilizer to low-value consumer film waste on the Erema Intarema TVEplus film recycling line can upcycle this material into a product suitable for film blowing.
Industry is the Key to Driving forward Sustainability
Holger Hoecker, Head of Safety, Strategy & Controlling, Evonik
One thing is clear: Plastics and other products manufactured by the chemical industry make an important contribution to climate protection. They help to use energy and other resources efficiently, for example, in transportation, where lightweight construction reduces fuel consumption, and in foam-insulated building facades, which improve energy efficiency. Without high-performance polymers, it would not be possible to build durable wind turbines, which make a key contribution to the energy mix. In view of the public debate about sustainability, waste avoidance and the use of resources, the idea of a circular economy is gaining importance.
At Evonik, our expert circle on the circular economy is working on specific and sustainable solutions. For instance, our specialists are undertaking a quantitative evaluation of the circularity of selected Evonik products. We use the material circularity indicator developed by the Ellen MacArthur Foundation and Granta Design to assess the potential circularity of selected products. In addition, we use life cycle assessments to evaluate the environmental impact of our products. The results support the sustainability analysis of our business.
Moreover, as a specialty chemicals company, our R&D is looking at solutions for mechanical and chemical recycling. That includes recycling both plastics and rubber. In this context, we are also looking into the feasibility of chemical recycling of PET plastics. Researchers at Evonik and Siemens are jointly exploring options for the use of CO2 as a production input. Taking nature as their model, their research included looking closely at photosynthesis. By combining electrolysis and fermentation processes, they have developed a carbon-based technology that uses green electricity to generate valuable chemicals. This technology is currently being tested in a pilot plant as part of the Rheticus project, which receives funding from the Federal Ministry of Education and Technology (BMBF). In the future, this innovative technology could be installed wherever carbon dioxide is generated. CO2 would then play an important part as a starting product in the chemical industry, analogously to photosynthesis in the natural world.
We are convinced that industry is the key to driving forward sustainability, environmental protection, and the circular economy. And that is in the interest of society and would benefit us all.
Circular Economy Is not a One-Size-Fits-All Solution
Thorsten Harke, CEO, Harke
The circular economy approach certainly is a good idea in some areas but of course not a one-size-fits-all solution. We have to be careful in certain cases, not to waste more energy and resources by circulating products, than we save by it, which would be counterproductive. In some of these cases a thermal utilization by waste-to-energy could be a more rational alternative.
As distributor and hence “transaction cost specialist” our role is per se to minimize the consumption of resources and hence the environmental impact in the sale and distribution process. We achieve this, by combining many products form different producers to a larger portfolio for our customers and hence reduce visits and shipments by combination synergies.
Furthermore, the environmental aspect is playing an important role when we consider adding products to our portfolio. Our strategy is to constantly expand our product lines with sustainable (from renewable resources), recyclable and/or recycled products and raw materials.
As internationally acting distributor, we deliver a wide range of plastic raw materials and products all over Europe, Russia and Turkey, of which a growing number are already either made from renewable raw materials, are recyclable or produced as or from by-products or from recycled raw materials.
Examples range from our Green Mantra product range of specialty polymers and synthetic waxes made from recycled plastics, our Q-Milk beads, produced from waste of the milk industry as substitute for micro plastics, over a larger range of oleo chemicals, solvents and polyols produced out of natural and therefore renewable raw materials. Furthermore, plastic products like films and containers that dissolve and/or are biodegradable, this way reducing plastic waste. In addition, we take back plastic waste from our customers in order to refeed it into our production process of plastic products like films.
Besides the high logistics costs and bureaucratic burdens for returning used material for recycling, especially in international trade, one big challenge is the still lacking acceptance and willingness to use recycled materials, due to partly higher costs of the recycled raw materials, technical and visual challenges and/or optical or qualitative compromises. Furthermore, the productivity sometimes can be a problem due to e. g. a worse melt flow rate. Yet we consult our customers how to adapt and optimize production processes accordingly.
At the Forefront to Deliver a More Sustainable Future
Maurits van Kolck, Group Director Regulatory, Quality and Sustainability, IMCD
The chemical industry is at the forefront of making their value chains both sustainable and circular. Developments in this area are increasing at an unprecedented pace.
IMCD plays an important role in the value chain for a wide range of raw materials, half fabricates, and formulations. The basis of our business model is that we can supply to the majority of the SME market, promoting the products of our suppliers to a much broader audience than they would ordinarily be able to themselves.
This enables us to introduce a circular approach and achieve a deeper market penetration, ranging from large to very small customers. We are then able to influence the use of these products across the wider, more fragmented economy. Our unique position allows us to contribute directly towards our partners’ efforts to become more sustainable.
We see the challenges for maintaining a healthy industry and environment in the future. However, we also see great potential and an industry that is galvanized to make a real difference. If we can also align with other sectors (like governmental, manufacturing, and waste processing), I personally believe the chemical industry will be at the forefront of a movement to deliver a more sustainable future.
Finding Innovative Solutions to Create a Circular Economy
Mark Vester, Circular Economy Leader, SABIC
At SABIC, we are helping to avoid plastic from becoming waste. Our vision is that plastic remains in the value chain to be reused and remade into new products and does not end up in our environment or landfills.
We are committed to finding innovative solutions to create a circular economy and close the loop on used plastic. We have already started making this a reality. Just over a year ago, we became the first in the industry to implement an investment project for the feedstock recycling of used plastic back to the original polymer. We recently launched our TRUCIRCLE portfolio and services for circular solutions that enable our customers to produce more sustainable products. Since then, we have helped several of our partners to successfully launch products using our circular solutions, most of which are already available on supermarket shelves.
Whilst we believe we can play a crucial role in closing the loop, no company can address these issues alone. We need to collaborate with players across the entire value chain and reshape our society, industry, frameworks and governing structures. We also need to encourage people globally to view plastic as a material which is on loan from the value chain. In doing so, we’ll create the right conditions to become truly circular.
This challenge has created fertile ground for groundbreaking innovations to enable this change. We now have new collaborations on the horizon that build on our TRUCIRCLE portfolio and will help to make our value chain a more circular one. We must continue to work together to transform everything we do and the way we do it, so we can all work together towards a sustainable, circular future for our business, our people, and the planet.
Circular Economy Means more than just Recycling Waste
Auguste Willems, Executive Board Member, Wacker Chemie
I am convinced that a circular economy on a global level is necessary to cope with the environmental challenges we are facing, such as the limited availability of natural resources and maritime littering, just to name two examples. In my opinion, there is no alternative to closing economic loops and turning "linear" material flows into cycles, enabling as much recycling as possible. However, we can only exploit these potentials with a comprehensive understanding of how to recycle waste and conserve resources as effectively as possible. We also need reasonable regulation which fosters technological openness and innovation. And last but not least, we need renewable energy at competitive prices for reducing the industry’s carbon footprint globally.
However, circular economy means more than just recycling waste. We need to look at the entire lifecycle of a product, including the materials used for manufacturing. The chemical industry is an important enabler in this respect. Our contribution here is more than just making our production processes more efficient and reducing waste and emissions by closing loops and reusing by-products. Our materials also enable innovations and technologies which significantly enhance the sustainability of products avoiding overall net emissions tremendously.
To initiate new ideas and grasp new opportunities, we started a program called Wacker Sustainable Solutions. The goal is to find out how our materials are able to optimize lifecycles of everyday products. The program has a long-term character of course, but already now, after a short period of time, we were able to identify and start a number of projects. For example, increasing the share of biobased and renewable raw materials in our products – be it polymer binders or silicone fluids – helps to effectively reduce the carbon footprint in a wide range of industries. And there is more to come. By 2030, nine out of ten products in our portfolio will be at least neutral or even better than neutral when evaluated according to generally valid sustainability standards. This will be a significant milestone in our roadmap and on our path towards CO2 neutrality in 2050.
Circular Economy Is Programmed into our DNA
Ansgar Pohl, Executive Officer, & CEO, Regional Headquarters EMEA, Mitsubishi Chemical
Circular economy is directly programmed into our company’s DNA by our vision of KAITEKI, which strives for the sustainable well-being of people, society and our planet Earth. That vision influences our whole company culture as well as technologies, products and solutions we develop for our customers. The circular approach and circular technologies will decide upon the future availability of our resources. It is the ideal way to do business and will be paramount for the sustainability of all industries, not only for the chemical industry.
As Mitsubishi Chemical we are placing an emphasis on three cornerstones: the use of bio-based and bio-degradable materials, the mechanical and chemical recycling of materials and solutions designed for recyclability.
Our bio-sourced portfolio includes many materials, both bio-based and biodegradable. This is complemented by our recent cooperation with Lactips, a company that promotes a bio-sourced, biodegradable and even water-soluble solution providing a response to the issue of micro-plastics ending up in the oceans.
The acquisition of the Swiss Minger Group which offers superior proprietary recycling technologies for engineering plastics illustrates our cornerstone of recycling. It will allow us to establish an integrated business model for engineering plastics including collection and reuse, hence contributing to the realization of a recycling-based society.
Last but not least we are convinced that only a joint approach of the whole industry will ensure success for the circular economy approach.
That is why we collaborate with partners and support many alliances, e.g. we act as a member of the Executive Committee for the Alliance to End Plastic Waste (AEPW) and we are part of the Ellen MacArthur Foundation’s Circular Economy 100.