Innovative PLA Catalyst Solution
SustainCat impressed the judges at the Discourse on Green Chemistry Interactive Pitch Competition with their innovative catalyst. As Jury Prize winners, they are now featured in CHEManager Innovation Pitch, showcasing their solutions for a sustainable future.
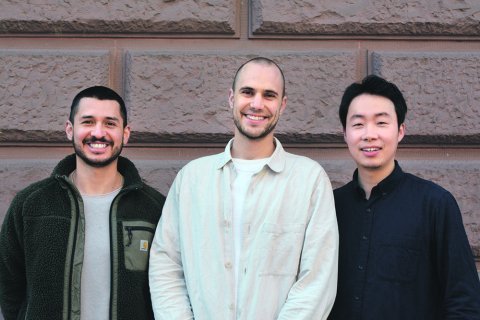
The Discourse on Green Chemistry Interactive Pitch Competition, held on November 5, 2024, at Wiley’s Berlin office, showcased innovative projects from early-stage startups addressing environmental challenges. Cohosted by CHEManager and GreenChem, the event saw SustainCat impress the judges with their approach to sustainable chemistry. Their innovative solutions earned them the Jury Prize. As part of their prize, they are featured in this issues CHEManager Innovation Pitch. As the Jury Prize Winner of The Discourse on Green Chemistry Interactive Pitch Competition, SustainCat demonstrated a high-performance catalyst that streamlines Polylactic Acid (PLA) production, cutting costs and energy consumption while improving the crystallinity and molecular weight. This innovation involves melt-phase condensation followed by solid-phase condensation, utilizing acidic supported solid catalysts, specifically calcined zirconium sulfate supported on carriers like SiO2.
CHEManager: What was the starting point and the motivations of SustainCat?
Johannes Häufler: Our multidisciplinary team was formed in the Treasure Hunting Summer School at the TU Berlin’s Innovation Center. During this program, we discovered the potential of our patent and decided to continue working on it together. We applied to take part in the pitch course and discourse of Berlin Science Week x Wiley x GreenCHEM. As a result, we were able to celebrate our first success with a successful innovation pitch.
What sets SustainCat apart from existing solutions in the market?
Juan Sebastian: We stand out by enabling direct polycondensation of L-lactic acid through melt-phase and solid-phase condensation, simplifying production and cutting PLA manufacturing time by 3 – 5 times. Unlike conventional catalysts, SustainCat is easily removed via mechanical filtration and can be directly reused, eliminating toxic residuals. It also achieves 60 – 80% crystallinity, which enhances heat resistance, speeds up processing, and makes it ideal for fiber applications and injection molding. In contrast, traditional tin-based catalysts rely on ring-opening polymerization, reach only 40% crystallinity, and leave behind impurities that are difficult to remove.
What are the advantages of the solution SustainCat proposed?
J. Sebastian: The development of catalysts that fasten the polymerization without any undesired side effects is of great interest. We are now able to present oxo-anion modified metal oxides as catalysts that fasten the pre-condensation of lactic acid, especially zirconium sulfate tetrahydrate (ZrS2O8) that was calcinated at 450 – 550 °C. A second positive effect is the insolubility of the catalyst within the reaction mass making it easily separable. First experiments produced nearly 100 mol% L-lactic acid units even at high conversion and catalyst concentration.
Who are your target customers, and what specific problems are you solving for them?
Huaiyou Chen: Our primary target customers are PLA manufacturers looking to enhance the sustainability and cost-effectiveness of their production processes. We’re helping them stay competitive against conventional plastics and other bioplastics. By making PLA production greener, non-toxic, and recyclable, we help cut costs in this growing market. High performance catalyst manufacturers could also be our customer per patent licensing. And if needed, we’re also open to supplying products directly to PLA end users.
What’s the vision for SustainCat? Where do you see your team in five years?
J. Häufler & H. Chen: Our immediate goal is to secure funding to validate our business model. We are focusing on conducting a techno-economic analysis to assess the commercial feasibility of our innovative direct polycondensation process for PLA production. Based on the current granted patent, a subsequent patent is in the plan. This will provide a solid foundation for our next steps.
In the next five years, we envision two potential pathways: establishing an SME-industry cooperation or founding a startup to commercialize our technology. By demonstrating the efficiency, cost-effectiveness, and sustainability of our approach, we aim to attract industrial partners interested in sustainable plastic and high-performance catalyst solutions.
Our long-term vision is to make PLA production significantly more sustainable and economically viable, reducing reliance on traditional, energy-intensive methods. With the support of TU Berlin and GreenCHEM, we are positioning SustainCat as a key player for affordable and competitive biodegradable plastics.
Personal Profiles
Huaiyou Chen is a PhD researcher in Material Sciences at TU Berlin, specializing in biomaterials processing, e.g. additive manufacturing of fungal mycelium materials. He holds a binational Master’s degree in Polymer Science and a Bachelor’s in Chemical Engineering and Technology. Combining a strong R&D background with industrial experience at BASF, he is enthusiastic and well-equipped for PLA catalyst development.
Juan Sebastian is a Master’s student in Polymer Science at HU Berlin, with expertise in polymer synthesis and metal-organic frameworks. His current research focuses on the synthesis and post-modification of mesoporous materials. Driven by an entrepreneurial spirit, he is motivated to explore opportunities in chemical innovation and business development.
Johannes Häufler is a Master’s student in Civil Systems Engineering at TU Berlin with expertise in life cycle analysis and computer-aided engineering. He has 3 years of experience in circular engineering consulting for the real estate sector, applying circular economy and cradle-to-cradle principles to develop sustainable solutions and drive innovation.

Greener PLA, Smarter Production
The global PLA market is growing due to the rising demand for biodegradable plastics and sustainable materials, expected to reach USD 3.3 billion by 2028. Conventional PLA production relies on energy-intensive ring-opening polymerization of lactide, which increases costs and limits scalability. SustainCat addresses these industry challenges through an innovative catalytic process that allows direct polycondensation of lactic acid to PLA, offering substantial improvements over existing technologies:
- Cost & Time Efficiency: Reduces PLA production time by 3 – 5 times, improves manufacturing efficiencies, cuts time and energy consumption, enhances industrial competitiveness.
- Improved Material Properties: Achieves high molecular weight and 60 – 80% crystallinity, enhancing mechanical strength, suitable for applications requiring high mechanical strength and hardness, such as packaging, automotive components, and medical devices like resorbable surgical sutures.
- Environmental and Health Safety: Unlike traditional tin-based catalysts, which can introduce toxic residues into the final product, this process uses non-toxic, solid catalyst, ensuring both the production process and final products are free from harmful substances.
- Recyclability: The solid catalyst can be easily removed from the final product and can be reused, significantly reducing waste and further contributing to a circular economy.
The technology behind SustainCat is protected by a granted patent, providing a strong foundation for commercialization. Further development continues to refine catalyst performance, assess long-term stability, and expand potential industrial applications.
In addition to PLA producers and catalyst providers, SustainCat also seeks collaborations with end-users in industries such as packaging, textiles, biomedicine, and 3D printing, to offer a timely, high-performance, and environmentally superior alternative to conventional plastics while making sustainable PLA a viable option for mass production.
SustainCat, Berlin, Germany
sustaincat@gmail.com
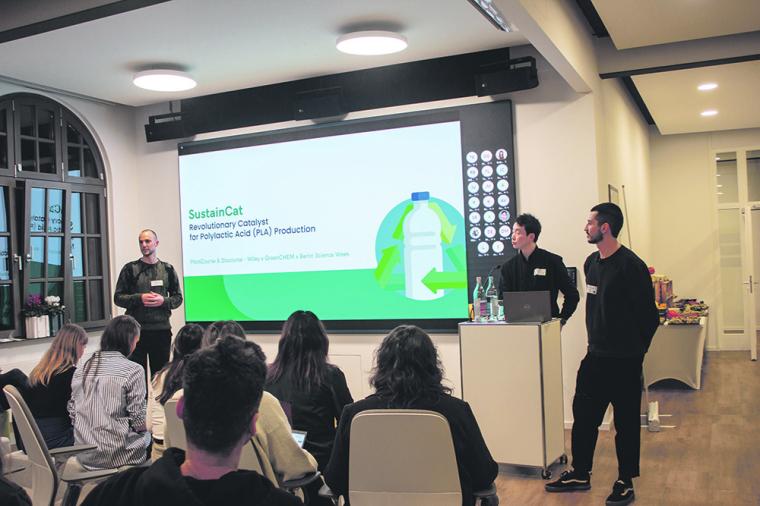
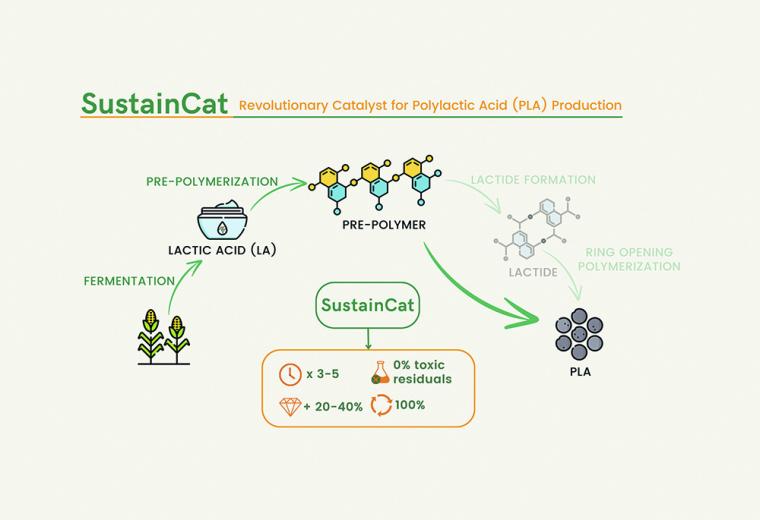

Catalyzing a Sustainable Future
SustainCat is driven by a commitment to addressing the pressing global challenges of plastic pollution through innovative chemical engineering. Our diverse, multidisciplinary team combines expertise in chemistry, material science, engineering, and sustainability, focused on redefining PLA production methods to set a new benchmark for industrial sustainability. By continuously advancing our catalytic technologies and fostering strong industrial and academic partnerships, we aim to lead the transition towards more sustainable plastic manufacturing process.
Milestones
- 2023
The concept of SustainCat was born during the Treasure Hunting Summer School at the TU Berlin’s Innovation Center, based on the patent on sustainable catalysis in polylactic acid manufacturing.
- 2024
Participated in the PitchCourse & Discourse Workshop by Wiley and GreenCHEM.
Winner of the Jury Prize at the Green Chemistry Interactive Pitch Competition in Berlin Science Week, validating our technology’s potential and appeal to both academia and industry.
- 2025
Collaboration with TU Berlin laboratories to further develop of the catalytic process and material characterizations.
Roadmap
- 2025
Actively pursuing strategic funding opportunities.
Establish industry partnerships with leading players in PLA manufacturing and catalyst production, targeting early pilot deployment in existing supply chain.
- 2026
Submission of a subsequent patent to expand and protect the core innovation, covering novel synthesis pathways.
Official product launching, including first commercial licensing agreements and direct sales.
- 2027
Scale manufacturing capabilities through joint ventures or contract manufacturing.
Diversification of applications across emerging sectors.