Expert Statement: Kai Rossen, Euroapi
Executives and industry experts share their views on drivers as well as barriers for the use of flow chemistry in pharmaceutical manufacturing and the prospect for this technology in their industry sector.
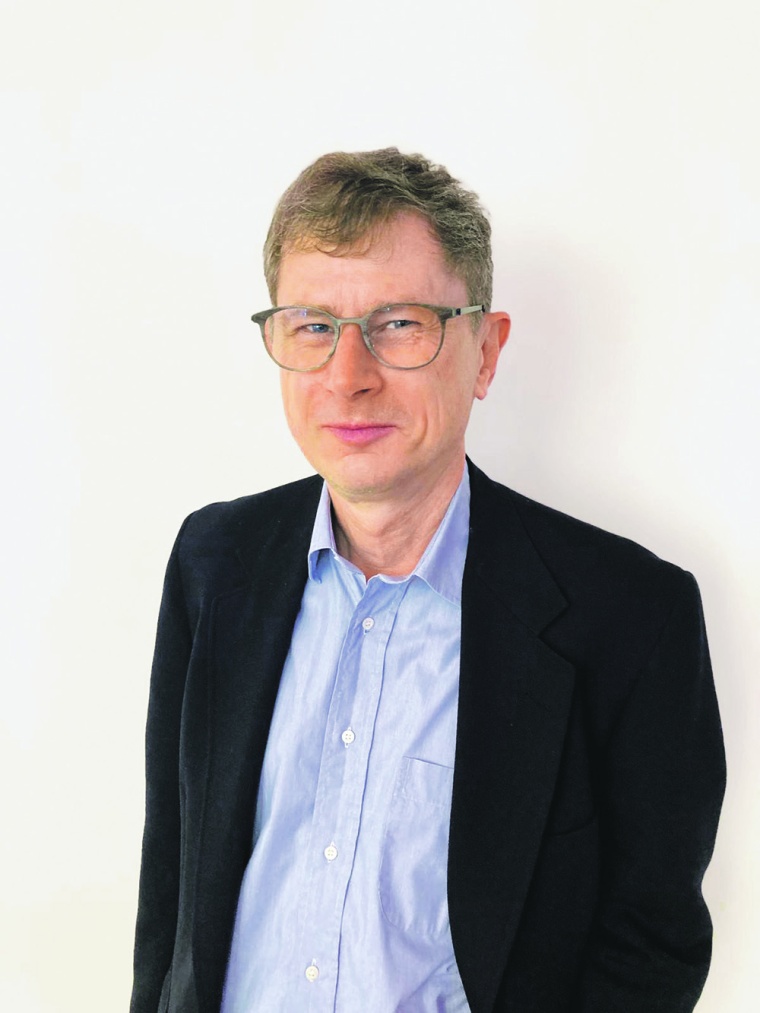
Continuous Manufacturing (CM) — also called Flow Chemistry or Micro Reaction Technology (MRT) — is a technique that has been gaining global importance over the past decade as a result of improved process control and reduced operating costs, leading to increased manufacturing profits and a competitive edge. Recent years have shown that the reason for a company to change from “batch” to “flow” have been varied, often depending on the sector, process type of interest and scale of operation. Supply chain security and improvements in process sustainability are strong emerging drivers for the adoption of CM.
With the product key, the infrastructure needed varies greatly and depends on the available chemistry, cost of goods, volumes required and the hazard profile of a transformation. The modularity and flexibility of continuous flow set-ups enables the development of small, agile production plants that can be used for the manufacture of multiple products — with easy re-configuration allowing for rapid product changeover.
Following on from this, the ease of replicating these small footprint systems represents an opportunity for manufacturers to develop a process and subsequently deliver production units across multiple countries to serve the local product demands. This is in stark contrast to the current approach of a single large-scale plant, with warehousing used to manage supply chain disruptions.
With all of these benefits, a logical question follows: Why the slow adoption of MRT?
CHEManager asked executives and industry experts to share their views on drivers as well as barriers for the use of flow chemistry and the prospect for this technology in their industry sector. We proposed to discuss the following aspects:
- In your opinion, what are the strongest drivers (success factors) of the implementation of flow chemistry processes?
- Which barriers are slowing down or impede the implementation of flow chemistry processes?
- What does it need for flow chemistry to be implemented more widely?
The synthesis of organic compounds is a science that is practiced for the last good 150 years. It had a great influence on the way we live today, as the wide availability of organic compounds is key for the high quality of life as we see it today. We could not imagine our current high quality of life if it were not for the many organic compounds that enable it – and we are talking here about a very wide range of compounds touching every aspect of our life. It starts with the housing of the coffee machine in the morning – made from an organic polymer, colored with organic colors and made resistant to the hot water with polymer additives and continues with the breakfast, made possible by plant protection agents which allowed our food to grow and kept it from being destroyed by fungi, insects, … All these are just very simple examples of how organic compounds effect pretty much every aspect of our life. All this is the extreme power of organic chemistry, which can and does create compounds with desired and required properties to address needs and demands, almost at will.
One of the most impressive success stories are medicines – mostly organic molecules prepared by organic chemistry – which are one of key pillars of our ability to have a much healthier and better quality of life than ever in the history of mankind.
All these compounds, including the active pharmaceutical ingredients (API) forming the basis of our medicines must be produced. The production of organic chemicals in general and API in particular is a complex science and technology, where classical organic chemistry interfaces with chemical engineering, mechanical engineering, digital tools, process analytical technology. Important is also the regulatory context with its strong impact on the quality of the products as well as the environmental responsible control of waste streams.
It is important to find the optimal solution to the technical problem at hand. It had been often the focus on the organic reaction and its optimization. While important, is it mandatory to look at the whole picture and not to ignore the possibilities enabled by technologic solutions. The last 20 years has shown a re-discovery of flow chemistry, which is a deviation from the classical batch process. The classical batch process requires a vessel – be it the small 10 ml glass vial in the laboratory or the big 10 m3 vessel in the plant. All the chemistry happens in that vessel with the reagents added, heated and stirred in a specific and defined manner. There is no doubt that classical batch chemistry works well, but there are many types of reactions and reaction conditions that simply cannot be performed in batch. These would be ignored in an optimization and are thus highly limiting. The application of flow chemistry enables reactions that could not be performed in a simple batch process and are thus a critical tool in finding the optimum for the synthesis of a compound, such as an API.
“There are many types of reactions and reaction conditions
that simply cannot be performed in batch.”
Flow chemistry is not an insurmountable panacea but a process that offers many advantages. Although running in continuous manufacturing does not automatically make a process superior, flow processing can provide access to conditions that are not possible in batch mode. For example, continuous reactions can give access to higher temperatures and pressure, enabling more efficient synthesis routes. From an economic perspective, it is also beneficial to avoid the cost of expensive large-scale batch autoclaves, and improving the yield and quality is always a good thing. Not to mention that batch processing is not always possible, like in bulk chemistry or oil refining.
There is no magic in heating, cooling and mixing faster reaction mixtures. It comes from the increased ratio of surface area to volume in the reactor that leads to an increased interaction with the external environment and allows for easier exchange of energy. In the case of flow chemistry, coming back to well-established chemical engineering principles can improve the safety profile of the reaction as highly exothermic chemistry can be better controlled thanks to high heat and mass transfer. Moreover, the continuous process can generate less hazardous substances and toxic releases. Regarding highly potent active pharmaceutical ingredients, continuous manufacturing can also reduce cross-contamination and cleaning needs.
Things must nevertheless be put in perspective and a comparison has to be fair. The level of development of the processes must be the same and even the safety profile can be challenged as it depends on the volume of hazardous reagents that are used. Demonstrating the robustness of the process requires a fair acknowledgement of topics like form stability, impurities, clogging or fouling. Improving transparency over the valuable continuous process can only help develop complex molecules and thus contribute to healthcare.
It is thus mandatory to be objective – simply putting a poorly designed reaction into a flow reactor, maybe even with additional solvent in order to reduce clogging, is simply false advertisement. It is regrettable when the impression is created that all the problems are solved by claiming implementation of a given chemistry into flow, and these types of claims are seen all too often and should be challenged.
On the other hand, processes that cleverly combine the potential of continuous processes into the design are extremely powerful and enabling. An example from Euroapi is our continuous production of Sevelamer, where the holistic design of a process is now enabling the continuous production of Sevelamer without the use of a solvent.
The Sevelamer example from Euroapi is a very good example that highlights the powerful potential of a flow reaction when excellent understanding of the underlying chemistry is combined with creative engineering. This development is enabled by open communication between the different disciplines of science, something that is helped when organic chemists have at least a basic knowledge of chemical engineering, just as chemical engineers are trained in organic chemistry. It is very good to see that the coming generation of scientists graduating from universities have this training and one can expect that the new generation will discover even more opportunities leading to better processes to produce API.