Expert Statement: Baburaj Krishnan, Aurigene Pharmaceutical Services
Executives and industry experts share their views on drivers as well as barriers for the use of flow chemistry in pharmaceutical manufacturing and the prospect for this technology in their industry sector.
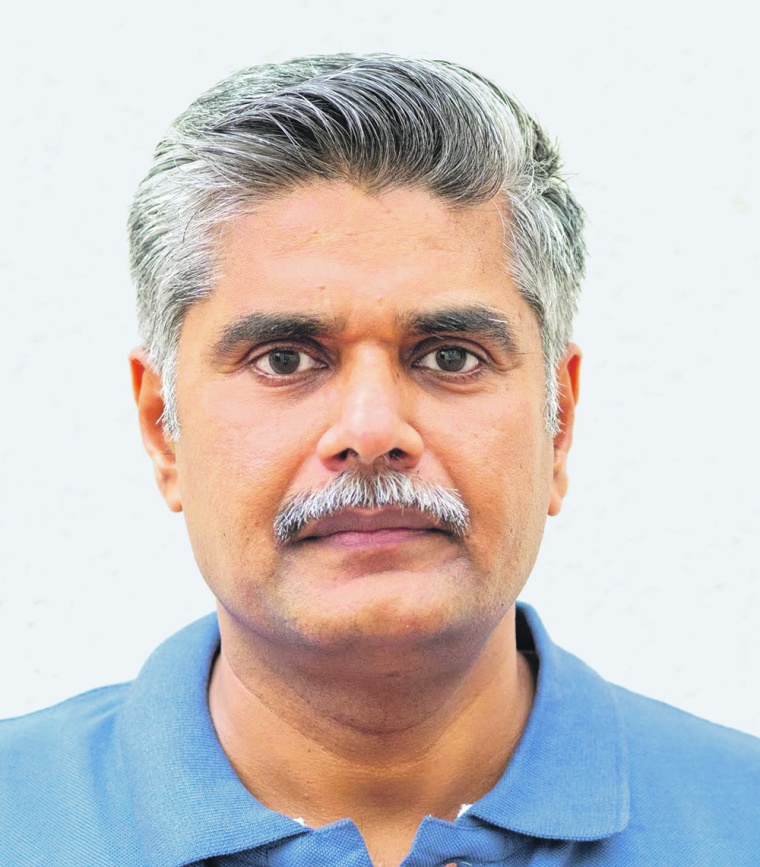
Continuous Manufacturing (CM) — also called Flow Chemistry or Micro Reaction Technology (MRT) — is a technique that has been gaining global importance over the past decade as a result of improved process control and reduced operating costs, leading to increased manufacturing profits and a competitive edge. Recent years have shown that the reason for a company to change from “batch” to “flow” have been varied, often depending on the sector, process type of interest and scale of operation. Supply chain security and improvements in process sustainability are strong emerging drivers for the adoption of CM.
With the product key, the infrastructure needed varies greatly and depends on the available chemistry, cost of goods, volumes required and the hazard profile of a transformation. The modularity and flexibility of continuous flow set-ups enables the development of small, agile production plants that can be used for the manufacture of multiple products — with easy re-configuration allowing for rapid product changeover.
Following on from this, the ease of replicating these small footprint systems represents an opportunity for manufacturers to develop a process and subsequently deliver production units across multiple countries to serve the local product demands. This is in stark contrast to the current approach of a single large-scale plant, with warehousing used to manage supply chain disruptions.
With all of these benefits, a logical question follows: Why the slow adoption of MRT?
CHEManager asked executives and industry experts to share their views on drivers as well as barriers for the use of flow chemistry and the prospect for this technology in their industry sector. We proposed to discuss the following aspects:
- In your opinion, what are the strongest drivers (success factors) of the implementation of flow chemistry processes?
- Which barriers are slowing down or impede the implementation of flow chemistry processes?
- What does it need for flow chemistry to be implemented more widely?
Flow chemistry processes significantly increase productivity and process safety, but a strong driver is the aim to design more sustainable processes, which goes hand in hand with these aspects. Sustainability is also the key focus for large-scale API manufacturing. It can be achieved by combining the green chemistry principle and continuous processes. While green chemistry brings a better atom economy, continuous processes improve reaction selectivity and yield. Flow chemistry can significantly minimize the use of solvents, which usually contribute 50% of the input mass in any batch manufacturing process. Integrating unit reactions and operations reduces the overall processing time and results in energy saving and high-throughput efficiency.
“A strong driver of flow chemistry
is the aim to design more sustainable processes.”
The technical capabilities in performing heterogeneous reactions and continuous crystallizations are an area to evolve. Batch processes provide flexibility for a wide range of reactions. Many homogenous and heterogeneous reactions can be performed in a single batch reactor without altering the equipment configuration. However, the flow process has particular limitations in accommodating different reactions in a single reactor.
Aurigene Pharmaceutical Services has a well-evolved methodology for establishing continuous processes. A recent example is a process that has been successfully developed and performed with continuous flow, which, otherwise, cannot be linearly scaled due to stability issues, its hazardous nature, and byproduct formation.