Sicherheit im Fokus – Arbeitsschutz in der Batterieproduktion
Individuelle Risikoanalyse und Schutzmaßnahmen für Mitarbeitende und Anlagen in der Batterieproduktion
Jede Batteriefabrik ist einzigartig, deshalb beginnt die Sicherheitsbetrachtung mit einer detaillierten und individuellen Risiko- und Gefährdungsbeurteilung. Dabei werden die spezifischen Prozesse, die verwendeten Materialien und die örtlichen Gegebenheiten berücksichtigt. Die Verantwortung für die Risikoanalyse liegt beim Unternehmer. In Deutschland ist dies im Arbeitsschutzgesetz, den zugehörigen Verordnungen sowie in den Regelwerken der Deutschen Gesetzlichen Unfallversicherung (DGUV) verankert. Die Risikoanalyse umfasst unter anderem die Definition des Schutzziels, die Identifikation von Gefahren sowie deren Analyse und Bewertung. Darauf aufbauend werden Schutzmaßnahmen festgelegt, die die Eintrittswahrscheinlichkeit von Gefahrensituationen minimieren und das Ausmaß möglicher Schäden begrenzen. Die Maßnahmen folgen der Maßnahmenhierarchie im Arbeitsschutz.
Staubpartikel bei der Slurry-Herstellung
Die Produktion von Lithium-Ionen-Batterien ist ein komplexer Prozess, der aus mehreren Schritten besteht. Um die Elektroden für Lithium-Ionen-Batterien herzustellen, werden zunächst Wasser, Lösungsmittel und das aktive Material in Pulverform gemischt. Für die Anode wird hauptsächlich Graphit verwendet, für die Kathode Lithium-Nickel-Mangan-Kobalt-Oxid. Diese Mischungen werden zu Pasten, auch Slurry genannt, verarbeitet. Im nächsten Schritt werden die Folien für Anode und Kathode beidseitig mit der Slurry beschichtet. Das Einatmen von Staubpartikeln bei der Herstellung der Slurry kann gesundheitsschädlich sein. Mitarbeitende, die während Abfüll-, Umfüll- oder Mischarbeiten mit den Nanopartikeln in Kontakt kommen können, sollten Atemschutz tragen. Gebläsefiltergeräte sorgen in der richtigen Kombination mit einem Helm, einer Haube oder einem Visier für einen konstanten Luftstrom ohne Einatemwiderstände. Die Tragezeitbegrenzung kann häufig entfallen. Die verwendete Schutzausrüstung sollte entsprechend den festgelegten Explosionsschutzzonen nach ATEX zertifiziert sein.
Brand- und Explosionsrisiko durch Lösungsmitteldämpfe und Elektrolyt-Leckagen
Nach dem Beschichtungsprozess werden die Elektroden getrocknet. Dabei können die zuvor verwendeten Lösungsmittel, wie N-Methyl-2-pyrrolidon (NMP), ausgasen. Lösungsmitteldämpfe sind brennbar und stellen ein Brand- und Explosionsrisiko dar. Im Anschluss an die Herstellung der Elektroden werden die Batteriezellen gefertigt. Nach der Montage werden diese mit Elektrolyt befüllt und anschließend in der sogenannten Formation und Aging-Phase konditioniert. In diesen Prozessschritten kann es zu Elektrolytleckagen kommen. Das Elektrolyt besteht grundsätzlich aus einem Leitsalz und Lösungsmitteln, die spezifischen Bestandteile variieren je nach Batteriehersteller. Elektrolytdämpfe sind brennbar. Um Leckagen frühzeitig zu erkennen und die Bildung einer explosionsfähigen Atmosphäre zu verhindern, werden ortsfeste Gaswarneinrichtungen installiert. Diese Geräte messen brennbare Gase in %-UEG und sollten für den Einsatz im primären Explosionsschutz über ein messtechnisches Gutachten verfügen. Werden kritische Konzentrationen erreicht, alarmiert das Gaswarnsystem und leitet automatisch Gegenmaßnahmen ein, die individuell im Schutzkonzept festgelegt werden.
Schutz der Mitarbeitenden vor giftigen Gasen und Sauerstoffmangel
Neben dem Brand- und Explosionsrisiko können in der Batterieproduktion weitere Sicherheitsrisiken für Mitarbeitende entstehen. Eingesetzte Lösungsmittel wie NMP und Elektrolyte sind oft nicht nur brennbar, sondern auch reizend und giftig. Halb- oder Vollmasken schützen die Atemwege der Menschen, die in Bereichen arbeiten, in denen Ausgasungen auftreten können.
Im Falle einer Elektrolyt-Leckage kann es zu unerwünschten chemischen Reaktionen kommen. Bei der Reaktion des Leitsalzes mit Wasser (z. B. Luftfeuchtigkeit) kann toxischer Fluorwasserstoff entstehen, der ebenso als Folge eines Batteriebrandes auftreten kann. Fluorwasserstoff verursacht schwere Verätzungen der Haut und Augenschäden. Der Arbeitsplatzgrenzwert gemäß TRGS 900 beträgt 1 ppm. Ein weiteres Sicherheitsrisiko entsteht durch den Einsatz von Stickstoff. Einige Prozessschritte, wie die Formation der Batteriezellen, erfolgen in einer inerten Atmosphäre, um eine möglichst hohe Batteriekapazität zu erreichen. Eine Stickstoffleckage kann den Sauerstoff in der Atemluft verdrängen und eine Gefahr für Menschen darstellen.
Um die Mitarbeitenden vor toxischen Gasen, Sauerstoffmangel oder explosionsfähigen Atmosphären zu warnen, werden mobile Mehrgasmessgeräte empfohlen. Diese werden direkt am Körper getragen und überwachen konstant die Umgebungsluft. Bei kritischen Konzentrationen werden die Träger akustisch, optisch und durch eine spürbare Vibration alarmiert. Darüber hinaus sind regelmäßige Stichprobenmessungen mit Analysetechnik wie dem Dräger X-pid 9500 sinnvoll, das direkt präzise Ergebnisse liefert. So können VOC-Konzentrationen in Laborqualität (ppm/ppb) ausgewiesen und ein Großteil von Elektrolyten selektiv detektiert werden.
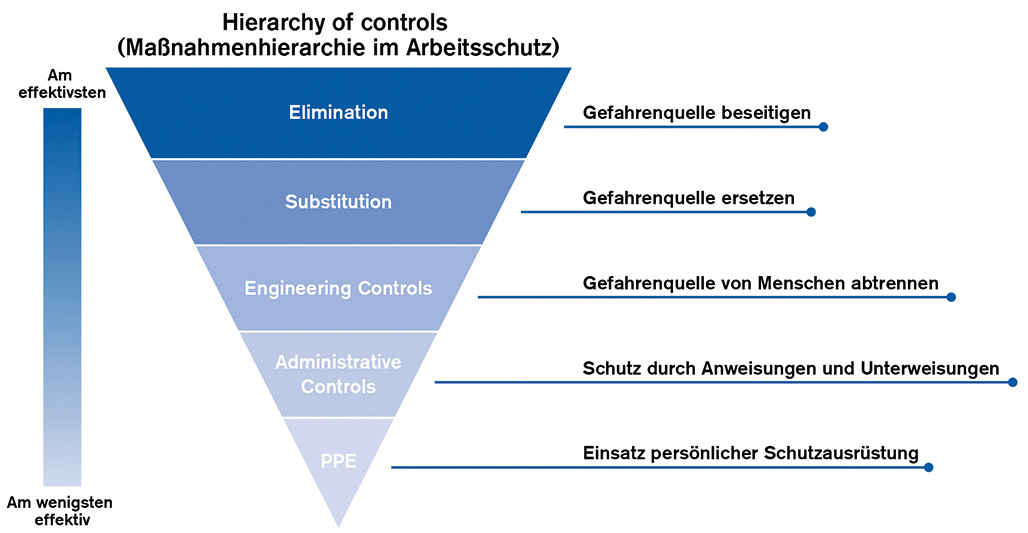
Umfassendes Rettungskonzept mit ausgebildeten Ersthelfern
Arbeitgeber müssen ein sorgfältig ausgearbeitetes Rettungskonzept haben und sicherstellen, dass die Zuständigkeiten klar geregelt und die Mitarbeitenden entsprechend geschult sind. Im Falle eines sicherheitskritischen Ereignisses in der Batterieproduktion wie eines Thermal Runaways müssen klare Abläufe eingehalten werden, die eine schnelle und sichere Evakuierung der betroffenen Bereiche gewährleisten. Dazu gehört auch die Bereitstellung von Fluchthauben, um die Mitarbeitenden vor giftigen Substanzen wie Fluorwasserstoff, Kohlenstoffmonoxid oder Cyanwasserstoff (Blausäure) zu schützen. Ersthelfer können verschiedenen Gefahren ausgesetzt sein, wie z. B. elektrischen Gefahren, Hitze durch Flammen, toxischen Gasen und Explosionsgefahr durch austretende brennbare Gase. Eine große Herausforderung besteht darin, dass verschiedene Bestandteile von Anode, Kathode und Elektrolyt freigesetzt werden können. Die Zellchemie, der Ladezustand und das Alter der Batterie beeinflussen diese Risiken. Für Ersthelfer in der Batterieproduktion ist es wichtig, die Sicherheitsrisiken zu kennen. Sie sollten von Anfang an in die Notfallpläne einbezogen und regelmäßig in Abläufen, Tools und Schutzausrüstung geschult werden. Der Zugang zu speziellen Gasdetektionsgeräten und Wärmebildkameras zur Lokalisierung von Brandherden sowie angemessener Körper- und Atemschutz ist dabei unbedingt zu gewähren.
Jede Batteriefabrik braucht ein individuelles Sicherheitskonzept
Die Produktion von Batterien ist ein komplexer Prozess mit individuellen Sicherheitsanforderungen. Da keine Batteriefabrik der anderen gleicht, ist eine individuelle Risiko- und Gefährdungsbeurteilung erforderlich. Ein ganzheitliches Sicherheitskonzept, das auf die Risiken in den einzelnen Prozessschritten und auf die Umgebungsbedingungen abgestimmt ist, schützt sowohl die Mitarbeitenden als auch die Anlage. Dazu gehören stationäre Gaswarntechnik für den Explosions- und Anlagenschutz, mobile Gasmesstechnik sowie Atem- und Körperschutz für den Personenschutz. Mitarbeitende und Ersthelfer sind mit dem Notfallplan vertraut zu machen und regelmäßig zu schulen.
Für den Notfall sind die Mitarbeitenden mit Fluchthauben und die Ersthelfer mit geeigneter PSA auszurüsten.
Autorin:
Frederike Schnalke, Business Development Managerin, Dräger
Dräger auf der Achema 2024, Halle 11.1 – Stand C75
Downloads
Kontakt
Drägerwerk AG & Co. KGaA
Moislinger Allee 53-55
23558 Lübeck
Deutschland
+49 451 882 0
+49 451 882 2080