Going Green in the Cleanroom
Did you know that a million plastic bottles are thrown away every minute? In other words, 400 billion single-use plastic bottles are discarded globally every year. That‘s according to data from the United Nations, which indicate that if the current situation continues, by the year 2050 the oceans will be home to more plastic than fish. In 1987, the United Nations Brundtland Commission defined sustainability as “meeting the needs of the present without compromising the ability of future generations to meet their own needs.” Sustainability forms one part of Contec’s Corporate Social Responsibility programme and includes processes, packaging, products and more. Contec commits to using alternative energy sources, preventing waste from going to landfill, utilizing recycled packaging and develop new and innovative recycled products.
lternative energy
In 2016 Contec installed 2,888 solar panels on the roof of one of its manufacturing sites in Spartanburg, South Carolina. This use of solar power prevented approx. 2 million pounds per year of CO2 being exhausted into the atmosphere from fossil fuels and provided the power needed to operate our manufacturing equipment. In 2021, two further installations added another 1,668 panels onto the roof of our Wingo Park facility and in a stand-alone solar farm, which is estimated to produce 944,600 kWh and offset Contec’s electricity usage by 53 %. Contec’s President, Avi Lawrence noted, “We’ve already begun tracking and sharing the results of these efforts with our associates and customers; framing the data in a way that is easy to understand by using analogies to personal energy use.”
Sustainability in a cleanroom
Being sustainable in critical and cleanroom manufacturing environments presents a challenge; not only because there are high energy costs involved in running cleanrooms, but the concept of reduce, reuse and recycle is difficult to put into practice. Cleanrooms use consumable products that cannot be recycled because of the ingredients they contain or because they have been contaminated with hazardous materials. For example, protected trigger spray bottles can neither be manufactured from recycled materials nor be recycled.
One option cleanroom users could consider to reduce the amount of single-use contamination control materials used is to launder and resterilise them. This is not a new concept; gowns and garments are regularly laundered and reused. However, there are risks associated with this option for wipes and mops used in high-grade areas.
Relaundering cleanroom consumables
Best practice for both wipes and mops in a cleanroom environment is to use single-use disposable products. This reduces the risk of cross contamination and ensures that contamination is physically removed from the cleanroom environment at the end of a session. However, many facilities are considering laundering and reusing mops to reduce costs and provide a more sustainable alternative to single-use disposable products.
Since disposable mops are made from new materials and follow a validated process, their performance and results are consistent and predictable. This remains constant even over a long period of time, as a new mop with the same parameters is used each time. Studies show that the effect of relaundering a mop can lead to the performance and quality changing over time due to inevitable degradation.
The laundry process can cause irreversible damage to the delicate structures of the wipe or mop. When evaluating a reusable mop, it is necessary to project the performance and quality over time to estimate the life cycle and therefore related costs. As the actual quality, contamination profile and performance of reusable mops will change over time, such deviation could result in unintended and potentially unacceptable risk to the customer’s environment and the product they produce.
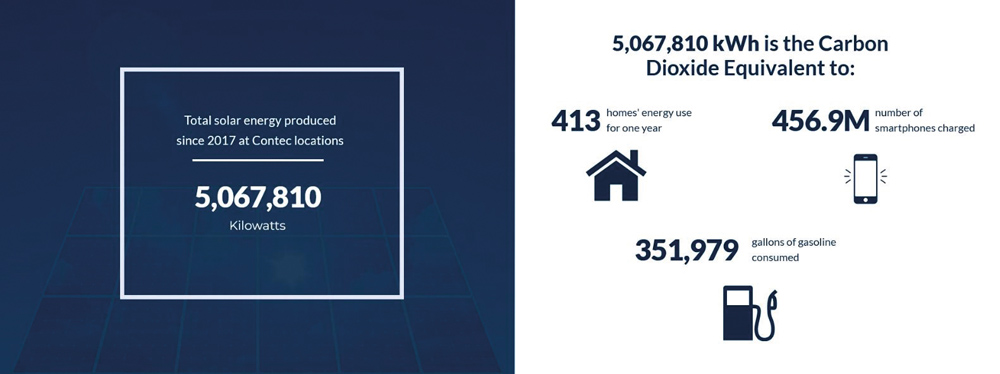
From waste to cleanroom wipe
There is now another way to be sustainable in a cleanroom; knitted cleanroom wipes, are manufactured from polyester (polyethylene terephthalate — PET). Plastic beverage bottles are also made from PET and products made from rPET (recycled polyester from post-consumer plastic bottles) are becoming more prevalent, so why not cleanroom wipes?
Contec is excited to expand the ReFIBE range of wipes, made from recycled plastic water bottles, these wipes are made from 100 % knitted standard weight polyester with heat sealed edges. These are ideal for cleanroom environments, with the additional benefit that they stop 35 plastic bottles per pack going to landfill or polluting our oceans; therefore, a case of wipes saves up to 840 bottles from contributing to environmental pollution. Incorporating sustainability into the upstream wipe manufacturing process means ReFIBE reliably provides a sustainable single-use option for critical environment manufacturers without jeopardising quality or performance. The wipes are exceptionally clean, low in releasable particles and fibres and are compatible with a wide range of cleanroom solutions and disinfectants. Now available presaturated with 70 % IPA, these wipes can be used in place of traditional polyester wipes. Like Contec’s standard polyester wipes, they have been laundered and packaged in cleanroom. ReFIBE wipes are subject to the same quality and process control protocols as virgin polyester products, removing any doubt of quality being compromised for sustainability. There are multiple steps taken to make ReFIBE wipes.
- Recycled plastic bottles are collected
- They are then chopped into flake and cleaned
- The bottle flake is melted, filtered and formed into chips
- The chips are melted and made into yarn
- The yarn is then knitted, cut and laundered to manufacture ReFIBE wipes.
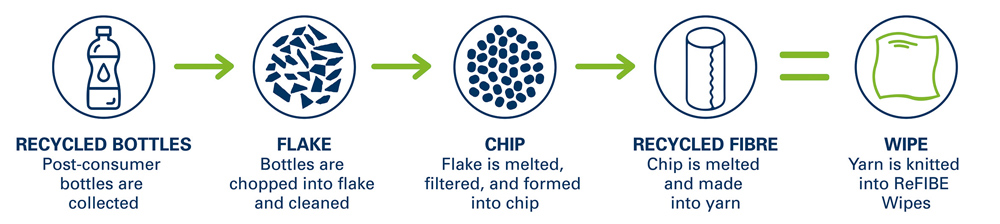
Sustainable options for cleanroom manufacturers are not without challenges and not all “green” initiatives pass the risk assessment for cleanroom use, certainly in higher grade cleanrooms. A facility will need to perform thorough research and risk assessments to evaluate all possible outcomes before embarking on green initiatives such as relaundering. However, as Contec is doing, all companies must strive to do more to reduce their environmental impact; to become more sustainable. The use of cleanroom wipes manufactured from post-consumer plastic is a small step towards this. Every step, big or small, can help.
Author:
Karen Rossington, Contec