Emissionsreduzierung in der chemischen Industrie
Strategien zur Dekarbonisierung umfassen die Elektrifizierung von Nieder- und Hochtemperaturprozessen
Die Industrie ist derzeit für etwa 29 % der weltweiten Treibhausgasemissionen verantwortlich. Nie war der Druck auf schwer zu dekarbonisierende Sektoren größer, nachhaltige Praktiken wie die Nutzung alternativer Brennstoffe einzuführen. Praxistaugliche Verfahren zur Emissionsreduktion stehen heute bereits zur Verfügung, wobei Energieeffizienz und Elektrifizierung eine wichtige Rolle spielen.
Das Whitepaper „Your route from A to Zero – Technologies to cut emissions in five hard-to-abate sectors“ des ABB-Geschäftsbereichs Motion und des Fraunhofer-Instituts für Produktionstechnik und Automatisierung (IPA) informiert über Möglichkeiten zu Emissionssenkungen in den fünf Sektoren Eisen und Stahl, Zement, Chemie, Bergbau sowie Öl und Gas und enthält praxistaugliche kurz- und langfristige Lösungsvorschläge für Unternehmen, die im komplexen Umfeld der industriellen Dekarbonisierung unterwegs sind.
Schlüssellösungen Elektrifizierung, Kohlenstoffabscheidung und Wasserstoff
Markus Kröll, Leiter des Geschäftsbereichs Kreislaufwirtschaft und Klimaneutrale Produktion am IPA, erläutert: „Unsere Analyse identifiziert die emissionsintensivsten Prozesse innerhalb der einzelnen Industriesektoren und zeigt Technologien zur Minderung dieser Emissionen auf. Sie legt den Schwerpunkt auf Schlüssellösungen: Elektrifizierung der Prozesswärme, Kohlenstoffabscheidung und Wasserstoff. Es gibt kein Patentrezept für die Dekarbonisierung, aber es stehen heute schon verschiedene Möglichkeiten zur Verfügung. Dieser Bericht dürfte es Führungskräften leichter machen, den besten Weg zu finden.“
Chris Poynter, Leiter der Division System Drives des ABB-Geschäftsbereichs Motion, betont: „Unser Bericht macht deutlich, dass der Weg zu Netto-Null mehr ist als ein Umweltziel, er ist eine strategische Geschäftschance. Die Dekarbonisierung der Industrie steigert die Effizienz, senkt die Kosten und sichert Unternehmen einen Vorsprung im Bereich nachhaltiger Innovationen. Durch Elektrifizierung und die Einführung von energieeffizienten Motoren, Frequenzumrichtern und alternativen Technologien kann die Industrie Emissionen reduzieren und gleichzeitig ihre betriebliche Wettbewerbsfähigkeit verbessern. Mit den Ergebnissen des Berichts helfen wir ihr, produktiver und nachhaltiger zu werden und kontinuierlich hohe Leistungen zu erbringen.“
Die Öl- und Gasindustrie bemüht sich verstärkt um die Reduzierung von Leckagen und die Elektrifizierung von Prozessen – Schlüsselmaßnahmen für deutliche Fortschritte in Richtung Dekarbonisierung. Zudem untersucht der Sektor alternative Brennstoffe wie Wasserstoff. Auf ähnliche Weise führt die Eisen- und Stahlindustrie Technologien wie direkt reduziertes Eisen und Elektrolichtbogenöfen ein, die emissionsärmer sind als herkömmliche Produktionsverfahren. Die Elektrifizierung ist auch eine Option für die Dekarbonisierung der Bergbau- und Zementindustrie. Dort kann eine Vielzahl von Geräten elektrifiziert werden, darunter alle neuen und alten Muldenkipper, Transportfahrzeuge, Bandförderer, Brecher, Mühlen und Pumpen.
Und welche Wege zur Emissionsminderung gibt es in der chemischen Industrie? Laut Studie lassen sich die Treibhausgasemissionen der chemischen Industrie drei verschiedenen Quellen zuordnen: direkten, wärme- und strombedingten Emissionen. Jede dieser Quellen erfordert einen anderen Ansatz zur Dekarbonisierung.
Chris Poynter, ABB
„Der Weg zu Netto-Null ist mehr als ein Umweltziel, er ist eine strategische Geschäftschance."
Direkte Emissionen
Direkte Emissionen beziehen sich auf die Treibhausgase, die direkt aus chemischen Prozessen und der Brennstoffverbrennung freigesetzt werden – sie machen in der Chemieindustrie 42 % der gesamten Treibhausgasemissionen aus.
Die Ammoniakproduktion trägt etwa zwei Drittel zu diesen Emissionen bei und ist für über 1 % der weltweiten Treibhausgasemissionen verantwortlich. Das Haber-Bosch-Verfahren, die wichtigste Methode der chemischen Industrie zur Herstellung von Ammoniak, trägt erheblich zu den CO2-Emissionen bei. Dies ist hauptsächlich auf das zur Wasserstoffherstellung benötigte Erdgas zurückzuführen, das ein wichtiger Reaktant im Prozess ist. Die Dekarbonisierung der Ammoniakproduktion konzentriert sich auf die Verwendung von kohlenstoffarmem Wasserstoff anstelle von synthetischem Wasserstoff. Der Bau der ersten Anlage zur Umwandlung von grünem Ammoniak in Strom ist ein wichtiger Meilenstein für die chemische Industrie. Viele hoffen nun auf eine breitere Verfügbarkeit von grünem Ammoniak. Andererseits verursacht die Produktion von Salpetersäure (hergestellt aus Ammoniak) etwa ein Drittel der direkten CO2-Emissionen der chemischen Industrie.
Die Methanolproduktion trägt ebenfalls erheblich zu den direkten CO2-Emissionen bei. Glücklicherweise ist es möglich, Methanol mithilfe von CO2 und kohlenstoffarmem Wasserstoff herzustellen. Das dafür benötigte CO2 kann aus nahegelegenen Kraftwerken oder anderen Emissionen abgeschieden werden. Diese Methode vermeidet direkte Emissionen und recycelt CO2, was zu einem geschätzten Reduktionspotenzial von 65 % bis 95 % führt.
Wärmebedingte Emissionen
Wärmebedingte Emissionen machen einen erheblichen Anteil der gesamten Treibhausgasemissionen der chemischen Industrie aus. Der Einsatz industrieller Wärmepumpen kann bei Niedertemperaturanwendungen hilfreich sein – Studien zufolge können sie in der chemischen Industrie weltweit jährlich etwa 119 TWh Wärmeenergie erzeugen. Und in Prozessen wie der Ethanoldestillation kann der gesamte benötigte Dampf mithilfe von Wärmepumpen erzeugt werden. Eine geplante Wärmepumpe in Ludwigshafen soll CO2-freien Dampf produzieren, der dann zur Herstellung von Ameisensäure eingesetzt wird. In diesem Fall könnte die Wärmepumpe die Treibhausgasemissionen der Anlage um bis zu 98 % reduzieren. Hochtemperaturprozesse über 150 °C stellen größere Herausforderungen dar, vor allem, weil Wärmepumpen und auch Kraft-Wärme-Kopplungsanlagen in diesem Temperaturbereich weniger praktikabel sind. Dennoch gibt es Technologien zur Erzeugung von Hochtemperaturdampf, z.B. Elektrifizierung durch elektromagnetische Erwärmung, Lichtbogenverfahren und Widerstandserhitzung.
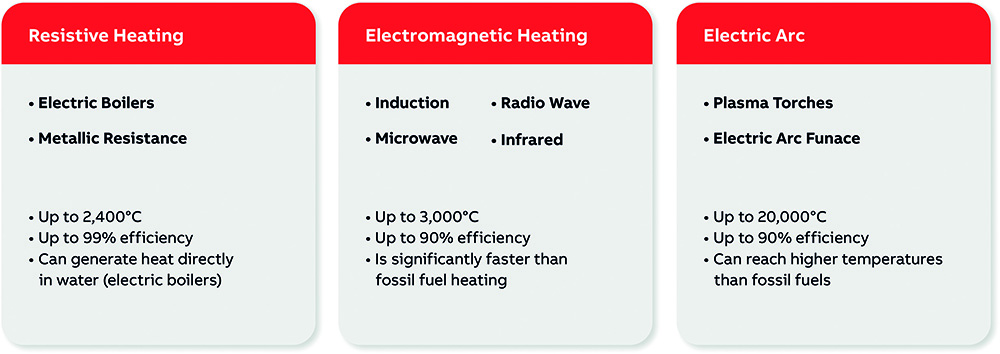
Elektrifizierung der Prozesswärmeerzeugung
Wärmepumpen sind die erste Wahl für die Elektrifizierung von Niedertemperatur-Prozesswärme (bis 150°C); sie können drei- bis siebenmal mehr Wärmeenergie erzeugen als sie elektrische Energie verbrauchen. Das macht sie zu einer praktikablen Option zur Reduzierung der Treibhausgasemissionen in allen Branchen. Sie erreichen besonders effektiv Temperaturerhöhungen von 30 bis 50°C, was sich für Anwendungen im mittleren Temperaturbereich eignet. Für den industriellen Einsatz sind Wärmepumpen mit einer Temperatur von bis zu 200°C erhältlich, die ein breites Spektrum an Anforderungen erfüllen – von der Gebäudeheizung bis hin zur Niedertemperatur-Prozesswärme. Effiziente Antriebe für elektrische Kompressionsmotoren können die Effizienz von Wärmepumpen zusätzlich steigern.
Auch für Hochtemperatur-Prozesswärme (Temperaturen über 150°C) gibt es heute praktikable Alternative zu fossilen Brennstoffen: die Direktelektrifizierung. Dabei wird Strom zur Wärmeerzeugung genutzt, bspw. durch Widerstandserhitzung, elektromagnetische Erwärmung oder Lichtbogenerhitzung. Diese Technologien sind marktreif und können die CO2-Emissionen deutlich reduzieren. Direktelektrifizierung kann zudem auf spezifische Temperaturbereiche und industrielle Prozesse zugeschnitten werden, was sie zu einer vielseitigen Lösung macht.
Mit Widerstandsheizung (Elektroboiler, metallischer Widerstand) kann bei einem Wirkungsgrad von bis zu 99 % im Temperaturbereich bis zu 2.400°C gearbeitet werden. Mit Verfahren der elektromagnetischen Heizung (Induktion, Mikrowelle, Radiowellen, Infrarotheizung) sind Temperaturen bis zu 3.000°C erreichbar, ebenfalls mit bis zu 99 % Wirkungsgrad. Die Verfahren haben zusätzlich den Vorteil, dass sie deutlich schneller sind als das Heizen mit fossilen Brennstoffen. Mit Plasmabrennern oder Lichtbogenöfen sind Temperaturen bis zu 20.000°C erreichbar bei einem Wirkungsgrad bis zu 90 % Wirkungsgrad – das geht weit über die Möglichkeiten fossiler Brennstoffe hinaus.
Strombedingte Emissionen
Strombedingte Emissionen machen derzeit etwa 35 % der gesamten CO2-Emissionen der chemischen Industrie aus. Davon sind 79 % auf Prozesse mit elektrischen Antriebssträngen (die Komponenten, die Strom in Bewegung umwandeln, einschließlich Motoren und Antrieben) zurückzuführen. Die Verbesserung der Effizienz elektrischer Antriebsstränge reduziert den Strombedarf für industrielle Prozesse – und senkt so den Stromverbrauch und die Emissionen. Untersuchungen haben gezeigt, dass IE5-Motoren im Vergleich zu vergleichbaren Induktionsmotoren bis zu 40 % geringere Energieverluste aufweisen. Dies würde die Dekarbonisierungsbemühungen unterstützen und zudem die Betriebskosten senken. Nach der Einführung beträgt die typische Amortisationszeit eines IE5-Motors nur ein bis zwei Jahre. Eine weitere wichtige CO2-Einsparmaßnahme ist der Einsatz von drehzahlgeregelten Antrieben, die den Stromverbrauch im Vergleich zu Antrieben mit fester Drehzahl um bis zu 25 % senken.
Markus Kröll, Fraunhofer IPA
„Es gibt kein Patentrezept für die Dekarbonisierung, aber es stehen viele Möglichkeiten zur Verfügung."
Wasserstoff
Wasserstoff dient vielfältigen industriellen Anforderungen. Er kann direkt genutzt oder in Derivate umgewandelt werden. Es wird erwartet, dass Wasserstoff in zukünftigen Netto-Null-Energiesystemen eine bedeutende Rolle spielen wird, insbesondere in Sektoren mit schwierigen Emissionsminderungspotenzialen, in denen eine Elektrifizierung nicht unmittelbar möglich ist.
Die Farben grün, grau und blau beschreiben die Wasserstoffproduktion und die damit verbundenen CO2-Emissionen. Grauer Wasserstoff wird aus fossilen Brennstoffen gewonnen und führt zu hohen Treibhausgasemissionen (10 – 16 g CO2-Äquivalent/g H2). Blauer Wasserstoff wird ebenfalls aus fossilen Brennstoffen gewonnen, dessen Auswirkungen jedoch durch CO2-Abscheidung und -Speicherung gemildert werden. Grüner Wasserstoff hingegen wird durch Elektrolyse aus Wasser hergestellt, die wiederum aus erneuerbaren Energiequellen wie Wind, Sonne und Wasserkraft gewonnen wird. Die Herstellung von grünem Wasserstoff kostet derzeit zwei- bis dreimal so viel wie die von blauem Wasserstoff. Die Wirtschaftlichkeit von grünem Wasserstoff hängt von der Senkung der Produktionskosten von 4 – 6 USD pro kg auf 1 – 2 USD pro kg ab. Laut der Internationalen Agentur für erneuerbare Energien könnten Leistungssteigerungen und eine Ausweitung der Produktion die langfristigen Kosten um bis zu 80% senken.
BASF nimmt 54-Megawatt-Wasserelektrolyseur in Betrieb
Am Standort der BASF in Ludwigshafen hat Deutschlands größter Protonenaustausch-Membran-Elektrolyseur (PEM) im März 2025 den Betrieb aufgenommen. Die Anlage zur Herstellung von grünem Wasserstoff hat eine Anschlussleistung von 54 MW und eine Jahreskapazität von bis zu 8.000 t Wasserstoff. Der in Zusammenarbeit mit Siemens Energy errichtete Wasserelektrolyseur ist eingebettet in die Produktions- und Infrastruktur am Standort Ludwigshafen und damit in seiner Schnittstelle und Integration in ein chemisches Produktionsumfeld weltweit einzigartig. Insgesamt wurden 72 sog. Stacks – Module, in denen der eigentliche Elektrolysevorgang stattfindet – in der Anlage verbaut. Der Elektrolyseur hat das Potenzial, die Treibhausgasemissionen am Stammwerk der BASF um bis zu 72.000 t pro Jahr zu senken.
Der hergestellte Wasserstoff wird in das H2-Verbundnetz des Standorts eingespeist und von hier aus den Produktionsanlagen als Rohstoff zur Verfügung gestellt. Neben dem Einsatz als Ausgangsstoff für chemische Produkte plant BASF den Wasserstoff bspw. für die Mobilität in der Metropolregion-Rhein-Neckar bereitzustellen, um die Entwicklung einer regionalen Wasserstoffwirtschaft zu unterstützen.
Katja Scharpwinkel, BASF
„Die Inbetriebnahme des Elektrolyseurs ist ein weiterer Schritt bei der Transformation des Stammwerks in Ludwigshafen."
Fazit
Die wichtigsten Strategien zur Dekarbonisierung der chemischen Industrie umfassen:
kurzfristig:
- Elektrifizierung von Niedertemperaturprozessen durch den Einsatz von Wärmepumpen
- Elektrifizierung von Hochtemperaturprozessen durch Widerstands- oder Strahlungsheizung
- Implementierung hocheffizienter elektrischer Antriebe
mittel- und langfristig:
- Nutzung von kohlenstoffarmem Wasserstoff zur Wärmeerzeugung
- Ersatz von Erdgas durch kohlenstoffarmen Wasserstoff für die Ammoniakproduktion.
Das englischsprachige Whitepaper „Your route from A to Zero“ von ABB und Fraunhofer IPA zeigt: Die Dekarbonisierung der Industrie ist komplex, aber es stehen schon heute umsetzbare Lösungen zur Verfügung. Durch Elektrifizierung und den Einsatz energieeffizienter Technologien und alternativer Brennstoffe kann die Industrie Emissionen reduzieren und gleichzeitig ihre Effizienz und Wettbewerbsfähigkeit erhöhen. In der chemischen Industrie bieten Niedrigtemperaturanwendungen wie Wärmepumpen die Möglichkeit zur Effizienzsteigerung und Emissionssenkung. Die Erkenntnisse aus dem Bericht geben Unternehmen einen Fahrplan an die Hand, um nachhaltigen Wandel voranzutreiben und zu einer kohlenstoffarmen Zukunft beizutragen.
Autor: Volker Oestreich, CHEManager