Prozessautonomie mit künstlicher Intelligenz
KI steuert komplexe Anlage und automatisiert Prozesse komplett ohne manuelle Eingriffe
Wenn es um die Einführung neuer Technologien geht, ist die chemische Prozessindustrie nachvollziehbarerweise eher konservativ aufgestellt. Änderungen an der Anlagenhardware und den Steuerungssystemen sind kostspielig, und es besteht die Gefahr von gravierenden Verlusten oder Zwischenfällen bedingt durch Technologieversagen. Andererseits ermöglichen jüngste Entwicklungen deutliche Produktionsverbesserungen bei geringeren Kosten. Aufgrund dieser positiven Erfahrungen suchen Chemieunternehmen und Zulieferer zunehmend nach neuen Möglichkeiten.
Kommt eine neue, konzeptionell andersartige, vielversprechende Technologie auf den Markt, wollen sich die meisten Unternehmen erst von ihrer Praxistauglichkeit überzeugen und warten ab, bis sie andernorts getestet und erprobt wurde.
Ein wichtiger Meilenstein für Unternehmen, die das Potenzial der autonomen Prozesssteuerungstechnologie nutzen möchten, wurde nun mit einer innovativen Technologie zur Steuerung eines Destillationsprozesses in einer Chemieanlage erreicht. Die besondere Herausforderung bestand darin, dass sich die Destillationskolonne mit herkömmlichen Proportional-, Integral- und Derivat-Regelkreisen oder gar fortschrittlichen Prozesssteuerungsstrategien nicht vollständig automatisieren ließ. Die Bediener mussten immer wieder kritische Ventile manuell betätigen, um die Flüssigkeitsstände in den Kolonnenböden zu regulieren und eine spezifikationsgerechte Produktion für alle Fraktionen zu gewährleisten. Zudem sollten durch die Nutzung von Abwärme in der Kolonne Kosteneinsparungen erzielt werden, doch die Abwärmeversorgung war unbeständig und nicht automatisch steuerbar.
Projektdetails
Das Projekt wurde von Yokogawa im Werk der Eneos Materials Corporation (ehemals JSR Corporation Elastomer Business Unit) in Japan durchgeführt. Ziel war es, dass Yokogawa seine Technologie der künstlichen Intelligenz (KI) zur Steuerung eines Destillationsprozesses einsetzt, um Stabilitätsprobleme zu überwinden, die bei dieser speziellen Anwendung aufgrund mehrerer komplexer Betriebsbedingungen auftreten:
- Das kritische Produkt und das Nebenprodukt sind aufgrund ihrer ähnlichen Siedepunkte schwer zu trennen.
- Die Kolonne wird mit einem herkömmlichen Kessel und Abwärme aus anderen Prozessen beheizt, um die Kosten zu senken und die Nachhaltigkeit zu verbessern. Die Abwärmeversorgung ist jedoch unbeständig, d.h. die Betreiber müssen ein Gleichgewicht zwischen den beiden Energiequellen herstellen.
- Die Anlage ist wechselnden Witterungsbedingungen ausgesetzt wie z.B. täglichen Temperaturschwankungen, Regen usw., die die Bedingungen in der Kolonne beeinträchtigen.
- Um spezifikationsgerechte Produktströme aus der Kolonne sicherzustellen, ist eine sehr strenge Regelung von Temperatur, Sumpfniveau und Durchsatz erforderlich.
KI-Implementierung
Für diese Art der Prozesssteuerung verwendet Yokogawa einen konzeptionell einfachen Ansatz. Ausgangspunkt ist ein Anlagensimulator. Dabei kann es sich um eine bestehende Plattform handeln, die zuvor für Analyse- und Trainingszwecke erstellt und dann für diese Projektform modifiziert wurde, oder um eine Plattform, die für ein spezielles KI-Projekt in Auftrag gegeben wurde.
KI verwendet Factorial Kernel Dynamic Policy Programming (FKDPP), einen auf Reinforcement Learning basierenden Algorithmus, mit dem der Simulator so lange arbeitet, bis nach etwa 30 Lernzyklen ein robustes Steuerungsmodell entsteht. Dann testet das Team die Validität des Modells durch Anwendung auf tatsächliche historische Betriebsdaten und Echtzeitdaten des Prozesses. Nach erfolgreichem Test sorgt das technische Team der Anlage für die ordnungsgemäße Anbindung an alle entsprechenden Sicherheits- und Alarmsysteme. Nun ist das Modell bereit zur Steuerung des eigentlichen Prozesses.
Der FKDPP-Algorithmus von Yokogawa wurde 2018 gemeinsam mit dem Nara Institute of Science and Technology entwickelt. Durch die Reinforcement-Learning-Techniken des Algorithmus kann das System mehrere Trial-and-Error-Zyklen durchführen, mit dem Prozess experimentieren und so seine Funktionsweise anpassen. Bei Praxistests mit Simulatoren und Implementierungen konnten die meisten Anwendungen genügend Wissen erwerben, um in nur 30 Zyklen einen stabilen Betrieb zu erzielen.
In vielerlei Hinsicht ähnelt dies einer modellbasierten Steuerungsstrategie. Die Fähigkeit zum Selbstlernen und die Robustheit des störungsresistenten Steuerungsmodells sind jedoch wesentliche Merkmale der Autonomie – insbesondere im Vergleich zu Modellen, die laufend vom Anlagenpersonal aktualisiert werden müssen, um effektiv zu bleiben.
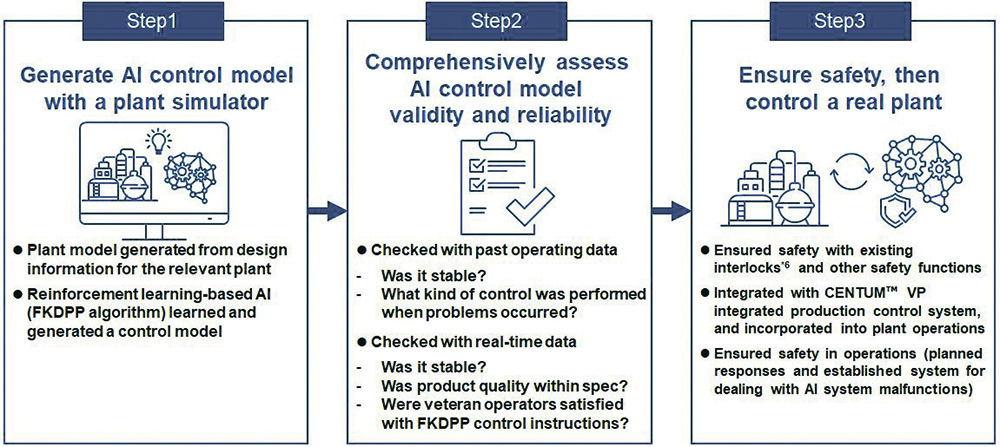
Aktive Zusammenarbeit
Yokogawa und Eneos Materials haben das Projekt gemeinsam durchgeführt. Eneos hat dazu den Standort der Produktionseinheit mit detaillierten Anlageninformationen, Betriebsstatus und historischen Prozessdaten sowie die Konnektivität mit dem bestehendem integrierten Produktionsleitsystem Centum VP bereitgestellt. Weiterhin wurden die spezifischen Prozessherausforderungen für das KI-Steuerungssystem sowie die Bewertung der Sicherheits- und Alarmschnittstellen aus Sicht des KI-Steuerungssystems vorgegeben.
Yokogawa übernahm die komplette Planung und Terminierung, die Erstellung des KI-Systems und das komplette Engineering für die Integration mit Centum VP sowie alle Wartungsarbeiten zur Vorbereitung der Instrumentierung und der Steuerungsinfrastruktur der Anlage.
Als zusätzliche Technologien wurden der OmegaLand Anlagensimulator von Yokogawas Tochtergesellschaft Omega Simulation, das Exaopc OPC-Schnittstellenpaket zur Verwaltung externer unterstützender Datenbanken über OPC Foundation-konforme Schnittstellen und die GA10 Datenerfassungssoftware für Bildschirm, Eingabegerät und Datenaufzeichnung bereitgestellt.
Definition von Erfolg
Für derartige Projekte muss es eine klare, quantifizierbare Definition von Erfolg geben, um die Investition zu rechtfertigen. Mit dem bestehenden Verfahren von Eneos Materials konnten abgesehen von gelegentlichen, kurzen Ausreißern die meiste Zeit über kosteneffizient spezifikationsgerechte Produkte hergestellt werden. Die Produktion wurde jedoch durch kleinere, aber kritische Prozessinkonsistenzen beeinträchtigt, und die Kolonne musste zur Optimierung regelmäßig manuell nachjustiert werden – was je nach Fachkenntnissen des Bedieners zu unterschiedlichen Ergebnissen führte.
Folglich wurde der Projekterfolg definiert als stabiler, vollständig selbstgesteuerter Prozess, der kontinuierlich qualitativ hochwertige, spezifikationsgerechte Produkte erzeugt, vornehmlich durch rückgewonnene Abwärme betrieben wird und ohne manuelle Bedienereingriffe auskommt.
Dies erhöht die Produktionsleistung und senkt gleichzeitig die Energiekosten, wobei die Bediener Zeit für höherwertigere Aufgaben haben als das Nachjustieren der Destillationskolonne. Für das Demonstrationsprojekt sollte die Anlage mindestens 30 Tage lang vollständig vom KI-System gesteuert werden. Wie sah das Ergebnis aus?
Durchschlagender Erfolg
Das KI-System hat den Destillationsprozess 35 Tage lang (17. Januar bis 21. Februar 2022) kontinuierlich gesteuert, bis die Anlage für die regelmäßige jährliche Wartung heruntergefahren wurde. Es lieferte ausnahmslos qualitativ hochwertige Produkte und die Betriebszeit entsprach der durchschnittlichen Betriebszeit einer herkömmlichen Anlage. Das System maximierte die Nutzung von Abwärme, verringerte die Kohlendioxidemissionen und verbesserte die allgemeine Nachhaltigkeit, wobei keinerlei manuelle Bedienereingriffe erforderlich waren.
Das enorme Potenzial der KI mit Reinforcement Learning für Systeme und Abläufe wurde dank dem Know-how beider Unternehmen und der Vollautomatisierung bislang automatisierungsresistenter Bereiche aufgezeigt. KI, Reinforcement Learning und FKDPP als Steuerungstechnologie der nächsten Generation werden die Entwicklung von der Automatisierung hin zur Autonomie deutlich vorantreiben. Zugleich lassen sich so die Kapitalrendite (ROI) und die ökologische Nachhaltigkeit von Anlagen maximieren.
Masataka Masutani, Bereichsleiter für Produktionstechnologie bei Eneos Materials, äußerte sich wie folgt: „Wir leben in einem Umfeld, das sich aufgrund der flächendeckenden Einführung von 5G und anderen Entwicklungen hin zur Digitalgesellschaft sowie der Überalterung des Personals, das die Anlagensicherheit derzeit gewährleistet, und des Mangels an Nachwuchskräften stark verändert. Die petrochemische Industrie steht unter massivem Druck, die Sicherheit und Effizienz ihrer Produktionsaktivitäten durch den Einsatz neuer Technologien wie IoT und KI zu verbessern. Eneos Materials möchte die Produktion durch den proaktiven Einsatz von Drohnen, IoT-Sensoren, Kameras und anderen neuen Technologien intelligenter machen. Bei diesem Projekt haben wir uns der Herausforderung gestellt, die Prozesssteuerung von Anlagen mit Hilfe von KI-Steuerungstechnologie zu automatisieren. Wir haben nachgewiesen, dass KI alle Prozesse, die bislang von erfahrenem Personal manuell ausgeführt werden mussten, autonom steuern kann. Wir sind fest überzeugt von der Effektivität und dem Zukunftspotenzial der KI-Steuerung. Wir werden KI-gesteuerte Prozesse weiter ausbauen und die Sicherheit, Stabilität und Wettbewerbsfähigkeit von Chemieanlagen optimieren.“

Auf in die Zukunft
Dieser Praxisversuch hat gezeigt, dass sich KI zur autonomen Steuerung eines kritischen Anlagenprozesses hervorragend eignet. Die Ergebnisse dürften andere Unternehmen in Japan und weltweit dazu ermutigen, ähnliche Projekte durchzuführen. Für Offshore-Bohrinseln, Fertigungs- und Prozessanlagen usw. besteht ein dringender Bedarf an ferngesteuerten autonomen Abläufen, und verschiedene Anbieter bieten bereits entsprechende Lösungen an.
Yokogawa und NTT Docomo z. B. haben einen Proof-of-Concept-Test einer ferngesteuerten KI-Technologie für die Prozessindustrie durchgeführt. Dieser Test demonstrierte die Anwendung einer autonomen KI-Steuerungstechnologie unter Verwendung des FKDPP-Algorithmus. Sie wurde in einer Cloud-Umgebung gehostet, wobei die Konnektivität über ein 5G-Mobilfunknetz von NTT bereitgestellt wurde. Dieser Test, bei dem ein simulierter Anlagenbetrieb erfolgreich gesteuert wurde, hat gezeigt, dass 5G für die Fernsteuerung von realen Anlagenprozessen bestens geeignet ist.
Die oben beschriebenen Ergebnisse und viele andere erfolgreiche Projekte belegen, dass KI für autonome Steuerungssysteme, die vor Ort oder in der Cloud gehostet werden, eine vielversprechende Zukunft hat.
Autor: Kenji Hasegawa, Vice President Yokogawa Electric und Leiter des Yokogawa Products Headquarters
„Ein wichtiger Meilenstein für KI und die autonome Prozesssteuerung wurde nun mit einer innovativen Technologie zur Steuerung eines Destillationsprozesses in einer Chemieanlage erreicht.“
Downloads
Kontakt
Yokogawa Deutschland GmbH
Broichhofstr. 7-11
40880 Ratingen
Deutschland
+49 2102 4983 0
+49 2102 4983 22