Anlagenkonzepte für die Chemieproduktion im Vergleich: Kosten, Flexibilität und Effizienz modularer Systeme
Wie modulare Anlagenlösungen die Investitionsentscheidung in der Prozessindustrie beeinflussen und welche Faktoren für „stick-built“, vorgefertigte und flexible Systeme entscheidend sind
Je größer, desto besser, und ausgelegt für eine Laufzeit von mehreren Jahrzehnten – was lange Zeit als Faustregel für wirtschaftliche Investitionsentscheidungen gelten konnte, hat heute an Bedeutung verloren. Für schnelle Produktwechsel, dezentral verfügbare Rohstoffe oder kleinere Produktionsvolumina ist die World-Scale-Anlage nicht geeignet. Flexible und modulare Systeme werden immer wichtiger. Doch wie entscheidet man, in welchem Anlagenkonzept die Investition am besten angelegt ist?
„Die Fortschritte im modularen Anlagenbau führen zunehmend zur Frage, welchen Einfluss dieser auf die Investitionskosten hat“, so Werner Pehlke, Vorsitzender der Dechema/VDI-Fachgruppe Cost Engineering. Dieser Aufgabe haben sich Experten der Dechema/VDI-Fachgruppen Modulare Anlagen und Cost Engineering gestellt und ein Papier veröffentlicht, das die zu evaluierenden Faktoren und geeignete Bewertungsmodelle unter die Lupe nimmt.
Stick-built, modular vorgefertigt oder flexibel
Die verfügbaren Anlagenkonzepte lassen sich im Wesentlichen nach drei Typen unterscheiden:
Konventionelle Anlagen werden an Ort und Stelle Stück für Stück aufgebaut (stick-built). Dafür ist eine große und komplexe Baustelle notwendig, an der von den Anschlüssen an die Infrastruktur über Gebäude bis zur Messtechnik alles nach und nach erstellt wird.
Bei der modular vorgefertigten Anlage werden einzelne Bausteine abseits des finalen Standorts zusammengebaut. Die Größen können von Containerformat bis hin zu Mega-Modulen reichen. Diese werden dann zum Betriebsort transportiert; dieser Transport limitiert gleichzeitig die Größe der Module. Vor Ort werden die Module zusammengestellt und verbunden sowie an die Infrastruktur angeschlossen.
Modulare, flexible Anlagen bestehen aus einzelnen Bausteinen, die jeweils eine bestimmte Prozessfunktionalität abbilden und sich problemlos zusammenstellen und verknüpfen lassen. Dafür sorgen ausgearbeitete Spezifikationen z.B. für Modular Type Packages (MTPs), die genau beschreiben, was im einzelnen Modul enthalten und wie die Schnittstellen beschaffen sein müssen. Die flexiblen Module lassen sich ohne großen Aufwand austauschen oder neu kombinieren, um z.B. andere Produkte herzustellen.
Diese drei Konzepte bringen Vor- und Nachteile mit sich: Modular vorgefertigte Anlagen können bspw. Unterschiede bei Arbeitskosten in der Montage in unterschiedlichen Regionen nutzen, indem möglichst viele Arbeitsschritte an einem Standort mit geringeren Lohnkosten erbracht werden. Allerdings limitieren Transport und Handling je nach Entfernung und Gegebenheiten an der Baustelle die Einsatzmöglichkeiten.
„Während das Gelände noch vorbereitet wird und die Genehmigungsschritte noch laufen, können beim Modulfertiger bereits die Stahlstruktur aufgebaut, Maschinen und Apparate verrohrt und instrumentiert werden. Das führt zu Zeiteinsparungen, die bei manchen Projekten bares Geld ausmachen“, so Pehlke weiter. Modular flexible Anlagen spielen ihre Vorteile vor allem dann aus, wenn viele schnelle Produktwechsel anstehen, sind aber in der Regel in der Skalierung limitiert. Konventionelle Anlagen sind wenig flexibel, können aber vergleichsweise einfach auf eine Produktion und ein Produktionsvolumen optimiert werden. Eine Investitionsrechnung muss solche Faktoren in Bezug auf den geplanten Einsatz in Betracht ziehen und gegeneinander abwägen.
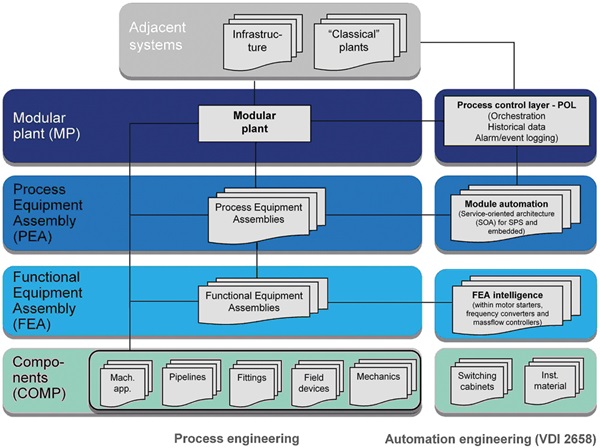
Bewertung „weicher“ Faktoren
Als Grundlage dafür dienen die sechs Dimensionen Markt, Technische Machbarkeit, Capex, Opex, Zeitplan und Risiko. Markt umfasst Faktoren wie Dauer des Produktlebenszyklus, Stabilität des Marktes oder die erwarteten Wachstumsraten. Aber auch die Time-to-Market und die Möglichkeit zu einem besseren IP-Schutz bei der Vorfertigung in geschützten Umgebungen spielen eine Rolle.
Technische Machbarkeit bezieht sich nicht nur auf die Anlage selbst, sondern auch auf die physische Umgebung: Wie viel Platz ist vorhanden, um eine Baustelleninfrastruktur einzurichten? Wie sehen Zufahrtswege und Logistik aus? Das reicht bis hin zu Fragen der Arbeitssicherheit und ist sehr individuell vom jeweiligen Standort abhängig.
Das Capex bezieht sich ebenfalls nicht nur auf die Anlage selbst, sondern auch auf die Gegebenheiten beim Bau: So kann es deutlich günstiger sein, wenn eine Anlage, die für einen Standort auf See vorgesehen ist, zunächst an Land möglichst weitgehend aufgebaut wird. Aber auch Möglichkeiten der Standardisierung können einen Einfluss auf das Capex haben.
Unterschiede im Opex ergeben sich in der Regel aus Inbetriebnahme und Wartung, aber auch aus der Effizienz einer Anlage, da die drei Typen unterschiedlich stark auf einen Prozess optimiert werden können.
Der Zeitplan für Design und Erstellung der Anlage kann je nach Konzept erhebliche Abweichungen haben. Das gilt nicht nur für die reine Bauzeit, sondern auch für die Meilensteinplanung und die Möglichkeiten zu Anpassungen während der Design- und Aufbauphase.
Risiken sind über die gesamte Anlagenlebensdauer zu berücksichtigen. Dazu gehören auch Marktrisiken wie ein Auslaufen von Produkten und Lock-in-Effekte bei wenig flexiblen Anlagen.
Investitionsentscheidungen neu denken
Auch die Entscheidungsprozesse für Investitionen unterscheiden sich. Modular flexible Anlagen eignen sich besonders für künftige Änderungen des Prozesses. Statische Methoden gelangen bei der Berücksichtigung von in der Zukunft liegenden Unsicherheiten nur bedingt zu guten Ergebnissen. Stattdessen helfen hier probabilistische Bewertungsmethoden weiter. Doch auch sie erfassen qualitative Unterscheidungskriterien wie Unsicherheit oder Flexibilität nicht oder nur unzureichend. „Um Faktoren wie Flexibilität angemessen zu berücksichtigen, muss man sich von den herkömmlichen Bewertungsmodellen lösen und Investitionsentscheidungen neu denken“, so Frank Stenger, Vorsitzender der Dechema/VDI-Fachgruppe Modulare Anlagen.
In den letzten Jahren hat sich die Realoptionsanalyse (Real Options Analysis) als Werkzeug etabliert, das Entscheidungsoptionen über den gesamten Lebenszyklus einer Anlage hinaus mitberücksichtigen kann. Alternativ bieten sich Scoring-Modelle an, bei denen sich Parameter je nach Einsatzzweck und -ort einer Anlage gewichten lassen. „Wir zeigen in dem Papier an mehreren praktischen Beispielen, wie stark die Resultate abweichen können, wenn der Fokus unterschiedlich gesetzt wird. Deshalb empfiehlt es sich, mehrere unterschiedliche Methoden zu kombinieren“, so Stenger.
Die vielen neuen Möglichkeiten, die modulare Anlagenkonzepte eröffnen, machen Entscheidungen nicht leichter. Doch mit den innovativen Entwicklungen lassen sich Projekte umsetzen, die in der „klassischen“ Welt nicht denkbar gewesen wären. Es lohnt sich deshalb, Aufmerksamkeit und Zeit in ein angemessenes Cost Engineering zu investieren und Konzepte zu entwickeln, mit denen sich die Anforderungen von Markt, Nachhaltigkeit und Wirtschaftlichkeit bestmöglich erfüllen lassen.
Autoren:
Markus Eckrich, BASF, Mitglied der Dechema/VDI-Fachgruppe Cost Engineering
Werner Pehlke, BASF, Vorsitzender der Dechema/VDI-Fachgruppe Cost Engineering
Frank Stenger, Evonik Operations, Vorsitzender der Dechema/VDI-Fachgruppe Modulare Anlagen
-------------------
Download des Statuspapier: (englischsprachig): https://dechema.de/Cost_Engineering_for_Modular_Plants