Kunststoffgranulate sanft trocknen
Energiesparend mit Wärmepumpe trocknen bringt Qualität, Sicherheit und Fördergelder
Wer seine Kunststoffe sanft entfeuchten möchte, benötigt eine Niedertemperaturtrocknung. Eine alternative Technologie auf Basis einer Wärmepumpe kann die Trocknung schonend und zugleich sehr energiesparend machen.
Auf den ersten Blick schienen beide Themen für lange Zeit gar nichts gemein zu haben. Inzwischen ist aber im Fokus, dass heiße Luft Kunststoffe nicht nur belastet, sondern natürlich auch viel Energie benötigt. Und so greifen zwei Themen ineinander, die für Harter schon immer praktische Realität waren. Der Trocknungsbauer hat bereits vor über 30 Jahren eine alternative Trocknungstechnik entwickelt, die auf Basis einer Wärmepumpe arbeitet. Das Hauptkriterium, in die sogenannte Kondensationstrocknung mit Wärmepumpe zu investieren, war immer, dass sich Trocknungserfolge erzielen ließen, die mit herkömmlichen Verfahren nicht möglich waren. Für das Energiesparen hat sich über Jahrzehnte niemand interessiert. Sie war lediglich eine nette Beigabe. Das hat sich inzwischen sehr verändert. So sehr, dass diese stets weiter optimierte Art der Trocknung heute mit staatlichen Fördergeldern unterstützt wird.
Mit Versuchen zur richtigen Trocknungslösung
Bei einer Anwendung, die all dies verdeutlich, handelt es sich um die Trocknung von Kunststoffgranulaten. Ein renommierter Hersteller von Polymer-Werkstoffen hatte einen Abluft-Heißluft-Trockner im Einsatz, der nicht die gewünschten Ergebnisse erbrachte. Eine neue und vor allem zeitgemäße Technologie sollte angeschafft werden. Die Granulate werden zu unterschiedlichen Produkten weiterverarbeitet, die in der Medizintechnik und in der Automobilindustrie ihren Einsatz finden. Für die jeweiligen Fertigungsprozesse benötigen die Granulate Restfeuchten von < 3 bzw. < 1 %. Zu dieser bereits sehr hohen Anforderung kam noch hinzu, dass die Granulate bei der Trocknung teilweise verklumpten. Somit entstand ständig ein gewisses Maß an Ausschuss. Mit dem Augenmerk auf die Energie und betriebsinterne Einsparpotentiale wurde schnell klar, dass der bisherige Heißlufttrockner mit Abluft zudem eine wahre Energieschleuder war.
Um die Machbarkeit gemäß den Anforderungen des Kunststoffspezialisten zu prüfen, wurden im Technikum des Trocknerhersteller erste Versuche durchgeführt und anschließend die Parameter für eine erfolgreiche Trocknung bestimmt. Diese sind Temperatur, Feuchte, Zeit, Luftvolumenstrom und Luftgeschwindigkeit. Ein weiterer Faktor ist die Luftführung, die vor allem bei Schüttgütern eine zentrale Rolle spielt. Um sicherzugehen, dass das Granulat nicht wieder verklumpen würde, wurden zusätzlich Testreihen beim Anwender vor Ort durchgeführt. Mit einer Leihanlage und nach Einweisung durch einen Techniker konnte der Granulathersteller nun selbst Versuche im größeren Maßstab vornehmen. Diese bestätigten die bisherigen Ergebnisse.
Während der Werkstoffhersteller eigentlich eine kontinuierliche Trocknung, einen Trockner mit Förderband, im Kopf hatte, zeigte sich in den Versuchen ein völlig anderes Bild. Mit dem richtigen Luftstrom und der passenden Luftführung war es tatsächlich möglich, das Schüttgut in einem Container zu trocknen. Diese Variante war nicht nur bedeutend günstiger, sondern auch von der betriebsinternen Logistik sehr viel einfacher.
Endlich homogen und vollständig trocken
Die heute eingesetzte Lösung ist ein Kammertrockner mit zwei fahrbaren Containern. Der Kammertrockner selbst besteht aus einer Trockenkammer und einem Wärmepumpenmodul. Die Trockenkammer nimmt den Container mit dem zu trocknenden Produkt auf. Dort findet die Trocknung statt. Die Container bei diesem Kammertrockner haben ein Volumen von 1,5 m³. Das Wärmepumpenmodul bereitet die erforderliche Prozessluft auf und ist ebenso für den Kondensationsprozess verantwortlich. Der Kammertrockner ist mit einer SPS-Steuerung ausgestattet, in der verschiedene Rezepte hinterlegt sind. Sie sind erforderlich, weil es Granulate in sehr unterschiedlicher Form und Größe gibt.
Der Trocknungsprozess läuft folgendermaßen ab: Die Kunststoffgranulate befinden sich in Big Bags, die auf einem erhöhten Gestell gelagert sind. Ein Mitarbeiter schiebt einen Trocknungscontainer darunter und befüllt diesen mit Granulat. Anschließend schiebt er den Container in die Trockenkammer und startet die Trocknung mit dem passenden Rezept. Sobald der geforderte Trockenstoffgehalt erreicht ist, gibt ein Feuchtesensor Meldung und der Trockner schaltet sich automatisch ab. Der Kammertrockner ist zudem mit einem Acetonsensor ausgestattet. Befindet sich zu viel Lösemittel in der Prozessluft, schaltet die Anlage automatisch ab. Nach Ende der Trocknung schiebt ein Mitarbeiter den Container wieder aus der Kammer heraus, entleert ihn mit Hilfe einer Kippvorrichtung und führt das trockene Granulat der Weiterverarbeitung zu. Währenddessen wird der zweite Container mit Granulat befüllt. So sind beide Trocknungscontainer abwechselnd im Einsatz.
Die vom Anwender geforderte Temperaturgrenze für die Trocknung lag bei maximal 40 °C. Bis zu dieser Grenze ist die Temperatur bei der heutigen Anlage variabel einstellbar. Auch der Luftvolumenstrom ist variabel. Beide Parameter sind, je nach Granulattyp, entsprechend in den Rezepten angepasst.
Die Wasserentzugsleistung liegt bei circa 840 l pro 24 h. Natürlich hängt sie stark von der Art des Granulats und dessen Feuchtegehalt ab und variiert dadurch. Alle Granulatvarianten sind jetzt nach dem Entfeuchtungsprozess homogen trocken und können somit direkt weiterverarbeitet werden. Qualitätsprobleme und Ausschuss gehören der Vergangenheit an.
Jonas List, Harter
„Eine zielgenaue Luftführung ist von großer Bedeutung. Sie bedarf großer Expertise. Und sie ist die Grundlage für eine vollständige und auch homogene Trocknung."
Energie sparen, Fördergelder erhalten
Der Kunststoffspezialist hat heute eine Trocknungstechnik im Einsatz, die alle Wünsche an die Qualität erfüllt. Die abluftfreie Trocknung macht überdies unabhängig von klimatischen und jahreszeitlichen Veränderungen. Somit ist der Trocknungsprozess reproduzierbar, was dem Betreiber eine sichere Produktion gewährleistet. Zudem ist die Wärmepumpentechnologie sehr energiesparend. Während Heißlufttrockner 1,3 kW pro Liter Wasserentzug benötigen, liegt der Vergleichswert bei dieser Art von Wärmepumpentrocknern bei nur 0,4 kW. Der Kammertrockner hat eine Nennleistung von nur 13,4 kW im Produktionsbetrieb. Im Vergleich zum alten Trockner erzielte der Anwender eine Einsparung von 60 %.
„Wer sich zu einer Investition in einen energiesparenden Kondensationstrockner mit Wärmepumpe entschließt, kann in den Genuss staatlicher Zuschüsse kommen“, erläutert Jonas List vom technischen Vertrieb bei Harter. Die in den Trocknern integrierte Wärmepumpentechnik arbeitet so
energie- und CO2-sparend, dass sie bereits 2017 in der DACH-Region als zukunftsorientierte Technologie und damit für die entsprechenden Förderprogramme eingestuft wurde. „Bis zu 85 % Energie- und 79 % CO2-Einsparung können im Vergleich zu herkömmlichen Systemen nachweislich erreicht werden. Auch der Anwender im beschriebenen Beispiel erhielt einen Zuschuss von 40 % auf das Investitionsvolumen“, so List.
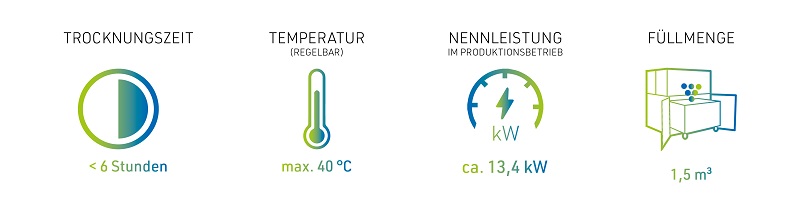
Abschließend lässt sich sagen, dass durch die abluftfreie Entfeuchtung mit extrem trockener Luft Produkte schnell, sicher und auch noch energiesparend getrocknet werden. Die Trocknung findet in einem variablen Temperaturbereich von 20 bis 75 °C statt, je nach Produkt und Prozess. Das Verfahren ist flexibel einsetzbar – für Batchbetrieb oder kontinuierliche Anwendungen. Die Anwendungen sind vielfältig so wie auch die konzipierten Systeme. Produkte aus Metall, Kunststoff und Glas lassen sich mit dieser Art der Trocknung entfeuchten. Das gilt auch für pharmazeutische und medizintechnische Güter. Die Schweizer Uhrenindustrie zählt zu den Anwendern, ebenso wie Hersteller von Medizinal-Cannabis. Ein weiteres Standbein des Unternehmens sind Trockner für Lebens- und Futtermittel. Auch die Trocknung von Industrieschlämmen und neuerdings auch kommunalen Klärschlämmen gehört zum Portfolio. Alle Anwendungen eint die energie- und CO2-sparende Wärmepumpentechnologie mit ihrer hohen Effizienz als Herzstück jeder Anlage.
Autorin:
Petra Schlachter, Technische Redakteurin,Harter