Flow Chemistry in Drug Discovery
Exploring the Benefits and Considerations for Synthesis
Flow chemistry enables safe, precise and efficient synthesis of compounds that can be scaled from pilot projects to manufacturing. Automated flow systems can quickly synthesize a wide range of compounds, making it ideal for generating libraries for early stages of drug discovery. This article delves into the key considerations when using continuous or segmented flow chemistry approaches.
Flow chemistry is when reactants are continuously pumped into a flow reactor with efficient mixing, and the product is collected. However, the development of automated flow systems is now allowing segmented flow regimes, using careful coordination of smaller aliquots of reactants to create smaller quantities of products. It is therefore important to carefully consider the appropriate flow regime to match your aims and experimental needs.
Flow Chemistry: Continuous Flow
Continuous flow describes chemical reactions occurring in flow reactor systems with cylindrical geometries, where reactants are continually introduced and mixed radially, effectively functioning as a series of ‘plugs’—or slugs—flowing through the system. Figure 1 highlights this phenomenon, where each coherent plug has a given length (dx) and volume (dV), traveling in the longitudinal direction of the reactor. The ‘ideal’ plug flow model assumes a steady state, no mixing between plugs, a constant density, and that only one reaction occurs.
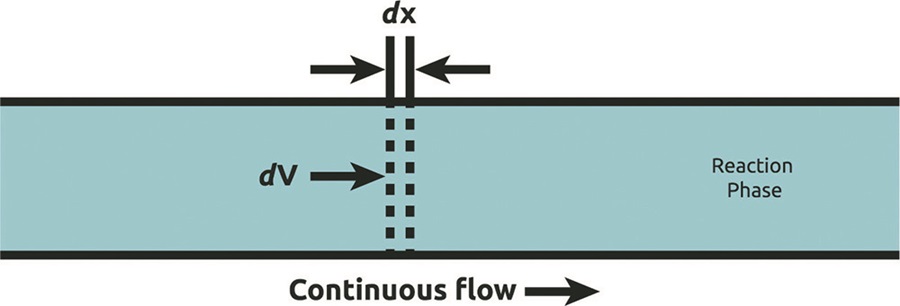
Flow Chemistry: Segmented Flow
Segmented flow is characterized by individual slugs of liquids or gases separated by a carrier fluid (fig. 2). Each discrete slug (Δx) has a defined volumes (ΔV) and the carrier fluid—which can be either liquid or gas is usually the same solvent used for the reaction to reduce solubility issues. This approach creates discrete ‘segments’ that allow screening of reaction conditions or the generation compound libraries.
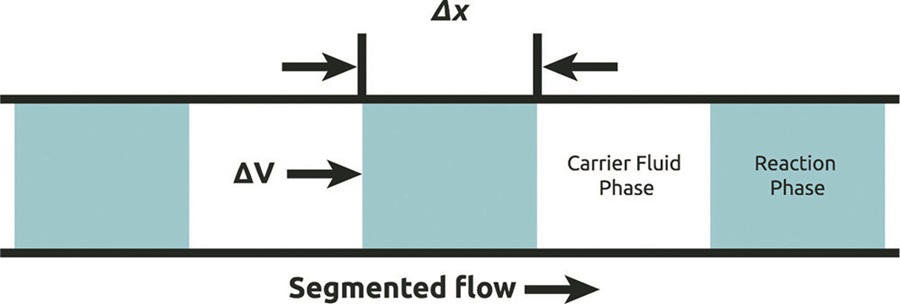
Optimizing Reactions
Traditional batch methods for optimizing reaction conditions can be time consuming and expensive. Modern flow chemistry systems with reagent injection modules—such as the modular Asia Flow Chemistry System [Syrris] controlled by advanced Asia Manager Software [Syrris]—provide a fully automated, walk-away alternative, allowing both continuous and segmented flow applications to save time and resources.
Compared to batch processes, continuous flow regimes enable faster, easier exploration of reaction parameters like time, temperature and reaction stoichiometry. However, continuous flow still requires the system to return to a steady state between experiments—as well as additional thorough cleaning to avoid cross contamination—demanding time and materials. Segmented flow, on the other hand, allows multiple reactions to be conducted sequentially using a single flow reactor setup, as the carrier solvent serves as a wash fluid to clean the reactor between experiments. The combination of reagent injection modules and advanced software makes it possible to efficiently explore both continuous reaction parameters and discontinuous variables, such as reagents and catalysts.
Library Generation
Automated flow chemistry systems can be integrated with process analytical technologies and computational chemistry to synthesize chemical libraries with minimum human intervention. Segmented flow regimes particularly excel in compound synthesis and library generation, and systems equipped with a reagent injection module and liquid handling capabilities can help to quickly evaluate various reactants for compound synthesis. These injectors can introduce reactant segments more quickly than the typical reaction—or residence—time, allowing multiple reaction segments to progress through the system concurrently. This reduces the synthesis time for the desired compounds and enhances overall process efficiency. Segment volumes can also be adjusted to enhance processes, offering maximum efficiency for a range of applications, including the generation of analytical data for reaction optimization and production of screening libraries.
“Automated flow systems can quickly synthesize a wide range of compounds.”
Automation and Software
Automated segmented flow is more efficient and accurate than traditional manual methods. For example, introducing the correct volume aliquot with a manual reagent injector is highly dependent on flow rates, so requires calculating the exact time to switch the injection loop in and out of line. This is often done using a stopwatch and injecting manually, leading to potential errors and inefficiency. Automated reagent injectors help to ensure that this process is consistent and reproducible, as well as accelerating the time to results.
In addition, it is important to track each segment to verify convergence at the correct junctions. When multiple reactants are introduced into a flow system, the segments must converge at the mixing junction for the reaction to occur, as shown in fig. 3. Advanced automation—such as Asia Manager—can accurately track segments to ensure proper convergence at the appropriate location. The injection of known solutions of compounds or dyes—followed by quantitative analysis after automated sample collection—can be used to assess convergence within a flow system.
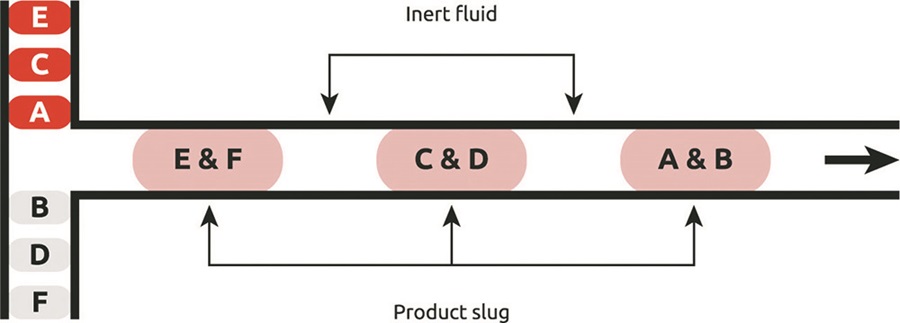
Minimizing Dispersion and Diffusion
It is crucial to minimize dispersion and diffusion within the system when conducting a flow chemistry experiment. Dispersion is minimal relative to the size of the slug in continuous flow reactions, so its impact is generally minor. In contrast, some dispersion—primarily in the longitudinal direction— can occur in segmented flow regimes using a miscible carrier solvent. In many cases, the reaction and carrier slugs mix, leading to the blurred regions at the front and back of the reaction slug. This creates a solute concentration gradient, which can impact reaction rates and residence times for concentration-dependent reactions. To eliminate this issue, an immiscible carrier solvent that prevents dispersion can be used, such as fluorinated solvents that have proven effective under organic reactions conditions.
Dispersion is more likely to occur when using a miscible carrier in combination with small segment volumes and longer residence times. Small samples undergoing significant dispersion will fail to achieve steady state conditions, so a smaller volume flow reactor should be used for these sample types. Increasing segment volume can help to minimize dispersion, as larger segments improve convergence, and typically achieve a steady state condition that provides the desired reaction concentration. Various pre- and post-slug values can also be employed to capture the steady state sample. When these values are zero, the total input volume is collected. Alternatively, additional volume can be added to either the front or the rear of the slug—to increase recovery—or subtracted to achieve greater purity and/or less dilution.
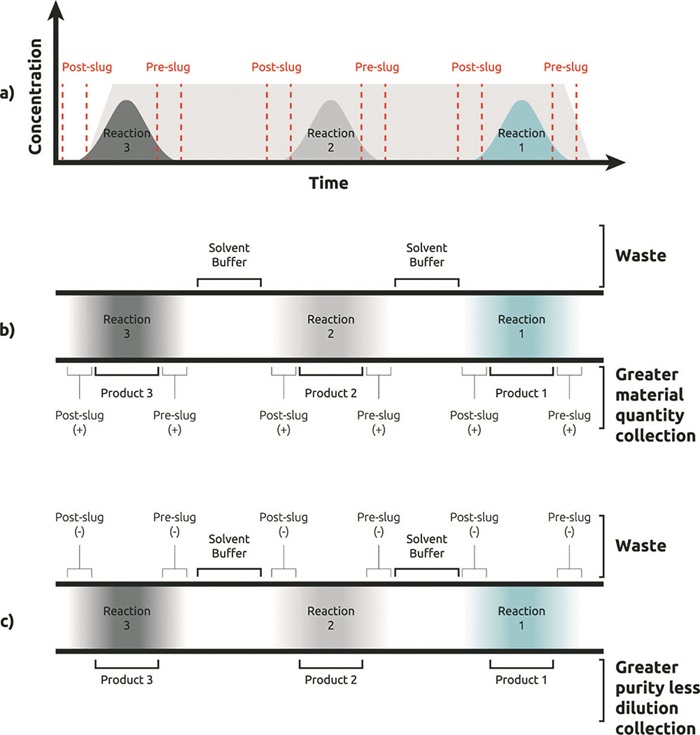
“Compared to batch processes, continuous flow regimes enable faster, easier exploration of reaction parameters.”
Conclusion
It is important to select the most appropriate flow chemistry regime and equipment based on the goals of the application. For segmented flow, automated flow systems and sophisticated software are necessary for accurate segment tracking and effective convergence, helping to ensure optimal results. By carefully selecting these tools, researchers can significantly improve the effectiveness and efficiency of their flow chemistry processes.
Authors: Leandro Carvalho, Senior Product Specialist, and Omar Jina, Chief Commercial Officer, Syrris, Royston, UK
Downloads
Contact
Syrris Head Office
Unit 3, Anglian Business Park
SG8 5TW Royston, Herts
United Kingdom
+44 1763 242555