The Subscription Revolution in Flow Chemistry
End-to-End Platforms for Flow Manufacturing On-Demand by Subscription
Flownetics Engineering designs, develops, manufactures, and operates end-to-end platforms for continuous synthesis on behalf of customers. The on-demand offering covers the complete cycle from inquiry to product and includes proof-of-concept as well as process development and machine learning (ML)-supported production system.
CHEManager: Mr. Balaram, you are the head of a manufacturer of machines and software for additive manufacturing. With Flownetics as a “game changer”, you now want to help flow chemistry to flourish globally. How does that fit together?
Sridhar Balaram: Technically, the answer is simple. The micro-reactors for our flow manufacturing platforms are additively manufactured and a key element of the end-to-end promise to our customers. The longer story: I first came into contact with flow chemistry more than a decade ago at a trade fair. You didn’t have to be a chemist to recognize the fascinating possibilities. I never lost sight of the topic and kept asking myself why the process had not achieved an industrial breakthrough. This question eventually led to the idea of founding a specialized start-up in order to revolutionize the industry as a “game changer” and virtually on a subscription basis.
Revolution is a huge word …
S. Balaram: And we use it very confidently! Not to provoke as a newcomer, but as a problem solver on behalf of customers to produce relevant raw materials, active ingredients and their intermediates — either as a factory-as-a-service at the customer’s site or as a contract manufacturer in a performance-as-a-service model. We know what we can do! Our end-to-end platforms deliver what users expect from us. And customers only pay for what they get from us. The risk of moving into flow chemistry, which has been repeatedly used for years as an argument against moving away from traditional batch chemistry, is therefore completely lost.
“Customers only pay for what they get. The risk of moving into flow chemistry, which has been used for years as an argument against moving away from traditional batch chemistry, is therefore completely lost.”
So you are predicting the beginning of the end of batch chemistry?
S. Balaram: No. The batch process has its merits in the past and certainly has a future. But the process is also well known for its limitations and restrictions. This, in turn, makes flow manufacturing the better solution from a technical, economic and ecological point of view in countless areas of application. Industry experts speak of up to 40 percent of applications to which this could apply. I think it will be closer to 50 percent. The future will provide the answer.
You presented the end-to-end range for the first time at this year’s ACHEMA. How was the response from the market?
S. Balaram: As a start-up, we can be very satisfied with how the trade fair went. As expected, the pharmaceutical industry was strongly represented. However, we were pleasantly surprised by the many inquiries from the cosmetics sector. Something else we had not expected in this form: The fundamental aspects and advantages of the flow process were less the subject of discussion in the trade fair talks than very specific questions about our subscription models.
What do you conclude from that?
S. Balaram: On the one hand: A lack of knowledge about the advantages of flow manufacturing does not appear to be the reason for the still low market presence of the process. Secondly: Subscription models still need to be explained to customers despite, or perhaps because of, their simplicity.
What was the most frequently asked question?
S. Balaram: Why we as a start-up are able to assume the financial and operational risk for the systems.
And what did you answer?
S. Balaram: That such an offering is only possible if a company combines all areas of excellence, in particular systems engineering, mechanical engineering, process engineering, process development, additive manufacturing, control technology and artificial intelligence or machine learning, under one roof. Otherwise, the friction losses between the individual competencies would be far too high and the coordination processes across company boundaries far too time-consuming.
-----------------------
Personal Profile
Sridhar Balaram has more than 30 years of experience in leading positions in the field of metal processing. He describes himself as a foundryman with roots in core manufacturing processes in various industries and services. He has founded and built several companies. Among others, he founded the company Intech Additive Solutions in 2012, which is today a leading manufacturer of machines and software for metal 3D printing. In April 2023, he founded Flownetics Engineering with the mission to revolutionize manufacturing in the chemical industry.
-----------------------
“Limitations and restrictions of batch processes make flow manufacturing the better solution from a technical, economic and ecological point of view in countless areas of application.”
Business Idea
Transformation in Flow
The chemical industry is still dominated by batch processing, even though the process is associated with inefficiency, high costs and considerable waste. In addition, batch processes are labor-intensive, prone to quality fluctuations and have limited scalability. The multitude of limitations are increasingly calling for more sustainable, efficient and resilient manufacturing methods.
In contrast, flow manufacturing is a revolutionary alternative as it enables continuous production that minimizes waste, improves quality control and reduces operating costs. In contrast to batch production, flow manufacturing also enables real-time monitoring and adjustment, resulting in consistent product quality and a significant reduction in production time and costs.
This is where Flownetics’ mission begins. By integrating mechanical engineering, process chemistry, AI and advanced control technologies, the company offers scalable and efficient solutions that democratize access to cutting-edge manufacturing technologies. Flownetics also addresses the arguments of high initial investment, technological complexity and the need for specialists. To this end, the end-to-end solutions are offered as Factory-as-a-Service (FaaS) and Performance-as-a-Service (PaaS) models.
Factory-as-a-Service (FaaS) is a subscription model in which Flownetics installs and operates flow manufacturing solutions at the customer’s site. This model enables localized production, reduces upfront costs and provides scalability. Flownetics provides continuous on-site support, including maintenance and upgrades, to ensure that production systems are state of the art. FaaS improves supply chain stability by enabling local production and reducing reliance on centralized suppliers.
Performance-as-a-Service (PaaS) is a subscription model in which Flownetics provides continuous flow manufacturing capacity. Companies outsource their production requirements to Flownetics, which manages the entire process from input material to final product based on its end-to-end platform. This model reduces capital expenditure, provides flexibility to scale production and leverages advanced technology for optimized performance and quality control.
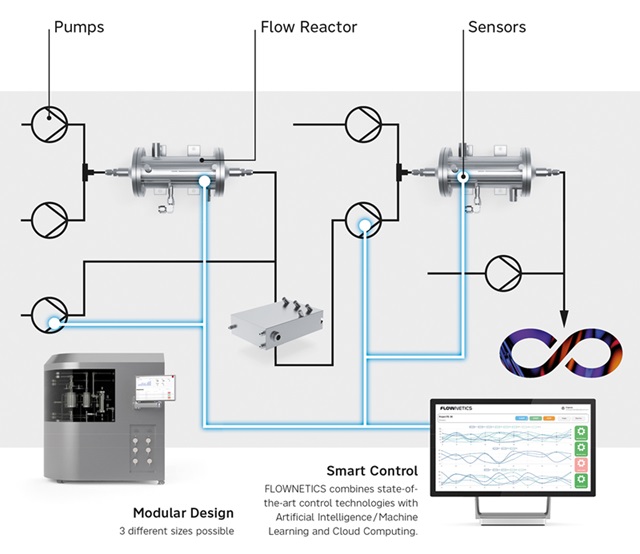
Elevator Pitch
Milestones and Roadmap
Flownetics Engineering was founded in April 2023 after an innovative pre-launch phase. The company, based in Bengaluru (also known as Bangalore), the capital and largest city of the southern Indian state of Karnataka, is on a mission to revolutionize pharmaceutical and cosmetic chemistry by providing scalable, efficient and sustainable end-to-end flow manufacturing solutions.
By combining expertise in mechanical engineering, process chemistry, 3D printing, control engineering and artificial intelligence, Flownetics unlocks a unique multidisciplinary approach for its customers that optimizes every aspect of their production. This synergy increases process efficiency, reduces waste and ensures high-quality production that overcomes the limitations of traditional batch production.
This is especially true for the business model: Flownetics’ offers Factory-as-a-Service (FaaS) and Performance-as-a-Service (PaaS), two subscription models that can democratize access to advanced manufacturing technologies in the chemical industry. Most importantly, these business models lower the financial barriers and enable companies of all sizes to revolutionize the future of chemical manufacturing without large upfront investments. By promoting local production, the inherent benefits of the process and improving supply chain resilience, Flownetics lowers costs for companies and promotes environmental sustainability.
Milestones & Roadmap
- 2022
– Vision and research activities
– MVP presentation at Achema 2022 Frankfurt, Germany
- 2023
– Launch of Flownetics Engineering
– Establishment of a Flow R&D Lab in Bengaluru, India
– Integration of the Software Flow Control Suite
– Integration of the FlowScale Suite
- 2024
– Flownetics Operational Suite
– World premiere of the End-to-End-Platform-Subscription at Achema, Frankfurt, Germany
– Several proofs-of-concept in progress as well as scale-up/FaaS commercialization projects
Downloads
Contact
FLOWNETICS Engineering
148/A, Industrial Suburb 1st Stage,
Yeswanthpura-560022 Bangalore
India
+91 9035021855