Effizientes Recycling von Lithiumbatterien
Engineering und Bau von Batterierecyclinganlagen
Der überwiegende Anteil der Zellen im Markt für mobile Anwendungen sind Lithium basierte Akkumulatoren aufgrund ihrer hohen Energiedichte bei hoher Zellenspannung. Die Lithiumakkumulatoren variieren in ihrem Aufbau, insbesondere bezüglich der Kathodenmaterialen und der Elektrolyte. Die Vielfalt an Lithiumakkumulatoren bedingt die unterschiedliche Zusammensetzung der Recyclingzuströme. Die größte Varianz liegt im Typ des Kathodenmaterials (CAM = Cathode Active Materials). Bestrebungen zur Standardisierung und Kennzeichnung der Typen wie z.B. dem Battery Passport laufen aktuell. Die Akkumulatoren basieren alle auf den Lithium-Grundchemikalien Lithiumcarbonat (Li2CO3) oder Lithiumhydroxid (LiOH•H2O).
Trennung der Akkumulatoren in Recyclingströme:
Akkumulator Zellen werden nach dem Stand der Technik zuerst mechanisch in folgenden Prozessschritten behandelt: (i) Demontage aus der Peripherie, (ii) totales Entladen der Zellen, (iii) Entfernen der Elektrolyte und (iV) Zuführung in spezielle Zerkleinerer. Zusätzlich zu den Zellmaterialien kommen die Stoffe der Peripherie hinzu.
Nach der mechanischen Zerkleinerung wird mit mechanischen Trennverfahren in die Stoffklassen Kupfer, Aluminium, Stahl und Kunststoff getrennt. Diese Ströme werden in die bereits etablierten Produktionsschritte und Lieferketten zurückgeführt.
Es verbleibt die sogenannte Black Mass (schwarze Massen), eine Mischung aus Anoden- und Kathodenmaterial mit kritischen Rohmaterialien. Besonders wertvolle Rohstoffe wie Lithium, Nickel, Kobalt, Kupfer und Mangan sind zu ca. ein Viertel enthalten und sollen zurückgewonnen und der Kreislaufwirtschaft zurückgeführt werden.
Aufschluss der kritischen Rohmaterialien aus der schwarzen Masse
Das hydrometallurgische Verfahren beginnt mit einem Aufschluss mit Schwefelsäure (engl.: Leaching), sodass die Rohstoffe in Lösung überführt werden. (siehe Grafik)
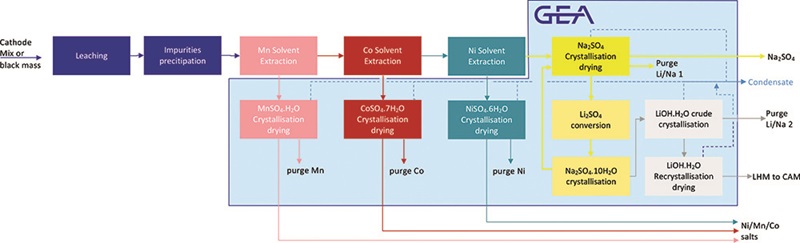
Aus diesen Lösungen werden anschließend Verunreinigungen ausgefällt. Die kritischen Rohmaterialien bleiben in Lösung und werden mit selektiven Lösemitteln, meist unpolaren organischen Lösemittel einzeln zurückgewonnen. Deren Zusammensetzung wird von Anbietern entwickelt und zumeist geheim gehalten. Erfahrungen gibt es hierbei aus der Erzaufbereitung. Nach der Lösemittelextraktion wird der Rohstoff für den nächsten Prozessschritt in Wasser gelöst und das Lösemittel zum Extraktionsschritt zurückgeführt.
Die kritischen Rohmaterialien lassen sich durch das thermische Trennverfahren Kristallisation abscheiden und reinigen. In diesen Schritten werden Mangan-, Cobalt- und Nickelsulfate gewonnen. Die weitere Prozessführung zur Gewinnung von hochreinen Lithiumverbindungen (Lithiumhydroxid-Monohydrat (LHM) oder Lithiumcarbonat) umfasst eine Rohkristallisation aus der verunreinigten Lösung. Durch spezielle Reinigungstechnologie wird ein optimales Verhältnis zwischen Wertstoff und Verunreinigungen eingestellt. Anschließend werden die Kristalle in Wasser aufgelöst und erneut aus dieser reinen Lösung kristallisiert.
Für die Anwendung in Akkumulatoren werden hochreine Verbindungen aus Lithium mit kritischen Rohmaterialien zu CAM weiterverarbeitet. In den letzten Jahren zeigte sich der Trend zu immer höheren Anforderungen an die Reinheit. Mittlerweise sind ca. 20 chemische Elemente spezifiziert mit Maximalkonzentration im ppm Bereich.
Viele Aspekte sprechen für eine Maximierung der Recyclingansätze. Recyclingmaterial aus internen Abfallströmen kann der Batterieproduktion direkt rückgeführt werden und zu neuen Anoden- und Kathodenmaterial verarbeitet werden. Dadurch sinkt der primäre Lithiumbedarf, was ökonomische Vorteile bringt und geopolitische Abhängigkeit von kritischen Ressourcen reduziert.
Prozessentwicklung und -ablauf im Batterierecycling
GEA verfügt über langjährige Erfahrung und zahlreiche Referenzanlagen für die Gewinnung und Reinigung von Batteriematerialien konventionellen Ursprungs. Weltweit sind bereits zehn aktive Anlagen für Lithiumhydroxid in Battery Grade Quality in Betrieb. Eine Referenzanlage für Batterierecycling ist in Südkorea in Betrieb. Dort wird ein unreines Lithiumsulfat zu Lithiumcarbonat aufbereitet.
Der Anlagebauer GEA bietet von umfangreichen Machbarkeitsstudien („feasibility Study“) über Pre-Engineering bis hin zum Bau von Anlagen im Pilot- bis großtechnischen Maßstab das gesamte Engineering-Spektrum an. Die Anforderungen an die Prozesse sind dabei sehr komplex und die Entwicklung muss immer als maßgeschneiderte Anlage für den Zweck durchgeführt werden. Besonders Hersteller die LHM bzw. ganze Akkumulatorzellen produzieren zeigen frühzeitig Interesse, Prozessabfälle aufzubereiten und als Rohstoffe wieder einzusetzen.
Für die Prozessentwicklung ist eine interdisziplinäre Zusammenarbeit unerlässlich, um die optimale Prozesslösung zu erreichen, wobei die numerische und chemische Simulation sowie die experimentelle Verifizierung ineinandergreifen und eine Schlüsselrolle spielen. Die Effizienz der Prozesse hängt von der Optimierung für die Anwendung, d.h. das Ausgangsmaterial ab. Die maßgeschneiderten Lösungen zielen auf die wichtigsten Optimierungsziele: Ausbeute, Energiebedarf und Reinheit. Die Anforderungen der Auftraggeber sind vielfältig und umfassen zudem Emissionen, Investitionskosten, Betriebskosten, Sicherheit und Produkteigenschaften.
Mittels numerischer Simulation wird der komplexe Prozess mit über 100 Equipments komplett von Anfang bis Ende in einer Massen- und Wärmebilanz simuliert. Dazu wird dieser aus einzelnen Prozessschritten zusammengesetzt (sog. „Unit Operations“). Für die chemische Simulation müssen alle Stoffe selbst im Spurenbereich in der Simulation berechnet werden. Veränderungen der Prozessströme, wie im Kristallisationsprozess, müssen realitätsnah implementiert werden. Hier findet zeitgleich ein Wärme- und Stofftransport statt. An dieser Stelle sind exakte Stoffwerte für z.B. Löslichkeiten notwendig. Die in kommerzieller Simulations-Software genutzten Modelle können diese jedoch nicht mit einer ausreichenden Genauigkeit in der Multi-Komponenten-Matrix der Black Mass berechnen. Daher werden die entsprechenden Parameter durch Laboruntersuchungen ermittelt und verifiziert. Besonders bedeutend sind dabei die Prozessschritte, in denen die Elemente voneinander getrennt werden, wie z.B. Kristallisation von reinen Kristallen aus einer verunreinigten Lösung.
Mit dem vorhandenen Know-how aus über 70 Jahren Erfahrung in der Kristallisation kann GEA ein Scale-up vom Laborversuch direkt zu einer großtechnischen Anlage durchführen. Durch die ineinandergreifenden Simulationsverfahren ist es möglich, die Reinheit des Endproduktes in der großtechnischen Anlage zu simulieren und später zu garantieren.
Der Anlagenbauer hat in ein neues Labor für Kristallisationsanwendungen investiert. Dieses Labor bietet zahlreiche Vorteile für die Weiterentwicklung und Optimierung von Recyclingprozessen, insbesondere im Bereich der Rückgewinnung kritischer Rohmaterialien aus gebrauchten Lithiumakkumulatoren.
Mit der experimentellen Verifikation können kritische Prozessschritte wie die Trennung von Elementen durch Kristallisation im Labor überprüft werden. Dies stellt sicher, dass theoretische Modelle durch praktische Daten unterstützt werden. Das Labor ermöglicht die Verifizierung numerischer und chemischer Simulationen der Prozesse und deren Massen- und Wärmebilanzen in detaillierten Versuchsaufbauten. Es sind auch mehrstufige Trennungs- und Aufreinigungsanwendungen abbildbar. Mit modernen Geräten und erfahrenen Anwendern kann die Analytik in einer Multi-Komponenten-Matrix durchgeführt werden, selbst wenn einige Stoffe nur im ppm-Bereich vorliegen. Dies ist entscheidend für die genaue Bestimmung der Reinheit der zurückgewonnenen Metalle.
Autor:
Philip Niggemann,Process Engineer, GEA
Downloads
Kontakt
GEA Group Aktiengesellschaft
Peter-Müller-Str. 12
40468 Düsseldorf
Deutschland
+49 211-9136-0
+49 211-9136-31087